Paper:
Wrapping Objects with an Automatic Contraction Ring
Takashi Mitsuda
Ritsumeikan University
1-1-1 Noji-higashi, Kusatsu, Shiga 525-8577, Japan
The rubber band gripper is an automatic contraction ring that is used to wrap and fix objects of various shapes by vacuuming the inside of the ring. It can be used to handle objects as a robot gripper, as well as fix bodies to pedestals, and objects to bodies. This study geometrically analyzes object shapes that can be wrapped using the ring, without causing gaps in the gripping mechanism. The analysis and experimental results show that the object shapes that can be wrapped without gaps are determined by the maximum shrinkage rate after the ring contacts the object as well as the circumference of the object. The range of object shapes that can be wrapped without gaps narrows as the object position moves away from the center of the ring. However, this influence is small, except when the object is small or has a large aspect ratio. In particular, when the object shape is cylindrical, it can be wrapped without gaps regardless of its position within the ring.
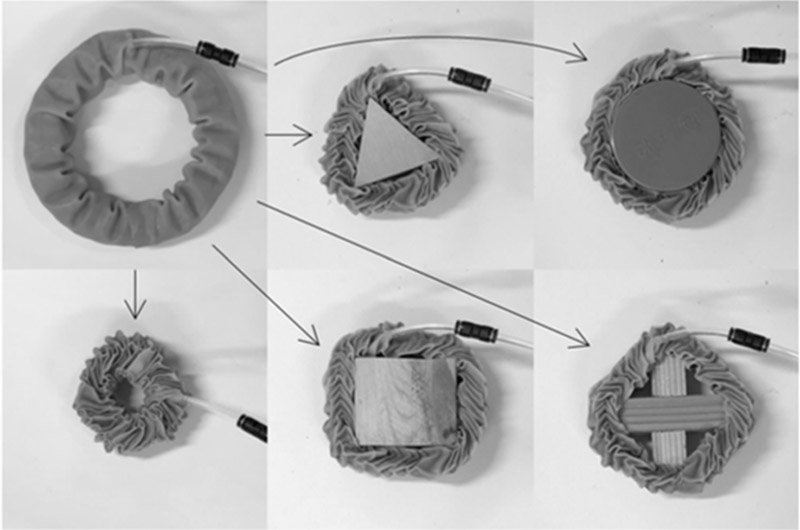
Wrapping around various objects
- [1] S. Zaidi, M. Maselli, C. Laschi et al., “Actuation technologies for soft robot grippers and manipulators: a review,” Curr. Robot. Rep., Vol.2, pp. 355-369, 2021.
- [2] S. Ross, O. Korostynska, L. E. Cordova-Lopez, and A. Mason, “A review of unilateral grippers for meat industry automation,” Trends Food Sci. Technol., Vol.119, pp. 309-319, 2022.
- [3] Q. Marwan, S. Chua, and L. Kwek, “Comprehensive review on reaching and grasping of objects in robotics,” Robotica, Vol.39, No.10, pp. 1849-1882, 2021.
- [4] A. Pal, V. Restrepo, D. Goswami, and R. V. Martinez, “Exploiting mechanical instabilities in soft robotics: control, sensing, and actuation,” Adv. Mater., Vol.33, Article No.2006939, 2021.
- [5] K. Yamada and T. Mitsuda, “A vacuum-driven rubber-band gripper,” ROBOMECH J., Vol.8, Article No.16, 2021.
- [6] Y. Dang, M. Stommel, L. K. Cheng, and W. Xu, “A soft ring-shaped actuator for radial contracting deformation: design and modeling,” Soft Robot., pp. 444-454, 2019.
- [7] F. Schreiber, M. Manns, and J. Morales, “Design of an additively manufactured soft ring-gripper,” Procedia. Manuf., Vol.28, pp. 142-147, 2019.
- [8] Z. Wang, R. Kanegae, and S. Hirai, “Circular shell gripper for handling food,” Soft Robot., pp. 542-554, 2021.
- [9] S. Otsuka and T. Mitsuda, “Development of a mechanical element that changes the shape and rigidity by vacuum pressure,” Trans. JSME, Vol.85, No.876, 2019 (in Japanese).
- [10] C. Mack and H. M. Taylor, “The fitting of woven cloth to surfaces,” J. Text. Inst., Vol.42, T477, 1956.
- [11] T. H. Kwok et al., “Rope caging and grasping,” 2016 IEEE Int. Conf. on Robotics and Automation, pp. 1980-1986, 2016.
- [12] T. Tamamoto, K. Takeuchi, and K. Koganezawa, “Development of gripper to achieve envelope grasping with underactuated mechanism using differential gear,” J. Robot. Mechatron., Vol.30, No.6, pp. 855-862, 2018.
- [13] K. Nishikawa, K. Hirata, and M. Takaiwa, “Development of Pneumatically Driven Hand Capable of Grasping Flexible Objects,” J. Robot. Mechatron., Vol.32, No.5, pp. 923-930, 2020.
- [14] Z. Wang, Y. Makiyama, and S. Hirai, “A Soft Needle Gripper Capable of Grasping and Piercing for Handling Food Materials,” J. Robot. Mechatron., Vol.33, No.4, pp. 935-943, 2021.
- [15] G. Endo, K. Yamagishi, Y. Yamanaka, and K. Tadakuma, “Development of High-Durability Flexible Fabrics Using High-Strength Synthetic Fibers and its Application to Soft Robots,” J. Robot. Mechatron., Vol.34, No.2, pp. 266-269, 2022.
This article is published under a Creative Commons Attribution-NoDerivatives 4.0 Internationa License.