Paper:
Impedance Control Considering Velocity Saturation of a Series Elasticity System with a Motor
Ren Fukui*, Yasuhito Kusakabe**, Ryojun Ikeura**, and Soichiro Hayakawa**
*Sinfonia Technology Co., Ltd.
Shiba NBF Tower, 1-30 Shibatdaimon 1-chome, Minato-ku, Tokyo 105-8564, Japan
**Faculty of Engineering, Mie University
1577 Kurimamachiya, Tsu, Mie 514-8507, Japan
Human-machine cooperative robots are required to drive their arms with low impedance and high torque. As a compact mechanism that generates a large torque and has low impedance characteristics, the series elastic drive system, in which an elastic element is inserted between the motor and driving unit, has been proposed. In this paper, we propose a method of applying impedance control to a series elasticity system with a torque-compensating motor that uses a torsion bar as an elastic body that enables its use under high loads. The stability of the system was verified via simulation and experiment by considering the allowable speed and maximum torque of the motor. The experimental results from the conventional system and the proposed system were compared. The proposed system was confirmed to be superior to the conventional system in terms of both stability and tracking performance. Consequently, the effectiveness of our proposed system was confirmed.
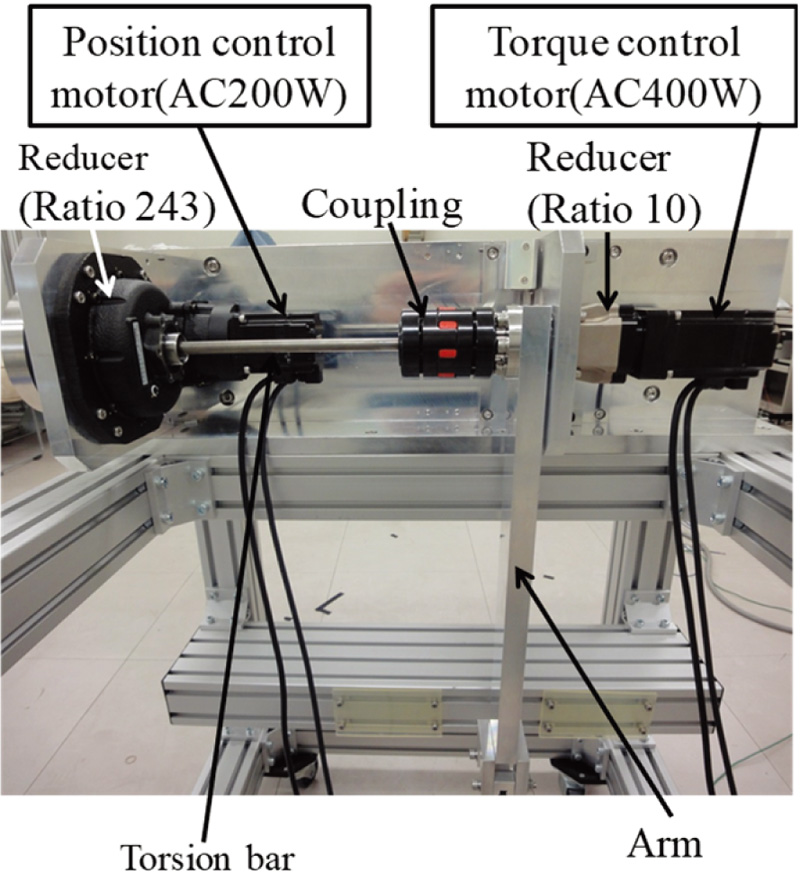
Series elasticity system with a torsion bar and a motor
- [1] Statistics Bureau of Japan, “Population estimation (2016/12/1),” 2018.
- [2] Cabinet Office, “Expert Committee on Economic and Social Structure Potential Growth Rate Expert Team Meeting Materials for the 4th meeting,” 2012.
- [3] Next Generation Robot Vision Roundtable, Ministry of Economy, Trade, and Industry, “Toward a society where humans and robots coexist in 2025,” 2002.
- [4] T. Mukai, S. Hirano, H. Nakashima, and Y. Sakaida, “Realization of Patient-Transfer Tasks Using Nursing-Care Assistant Robot RIBA and Its Safety Measures,” Proc. of the 2010 JSME Conf. on Robotics and Mechatronics, 1A1-E24(1)-1A1-E24(4), 2010.
- [5] R. Kurozumi, T. Yamamoto, S. Fujisawa, and O. Sueda, “Development of Training Equipment with Adaptive and Learning Using a Balloon Actuator-Sensor System,” J. Robot. Mechatron., Vol.21, No.1, pp. 156-163, 2009.
- [6] E. Tanaka, T. Ikehara, H. Yusa, Y. Sato, T. Sakurai, S. Saegusa, K. Ito, and L. Yuge, “Walking-Assistance Apparatus as a Next-Generation Vehicle and Movable Neuro-Rehabilitation Training Appliance,” J. Robot. Mechatron., Vol.24, No.5, pp. 851-865, 2012.
- [7] D. Tanaka and T. Nakamura, “Compliance control of Artificial Muscle Manipulators,” Proc. of the 2009 JSME Conf. on Robotics and Mechatronics, 1A2-M02(1)-1A2-M02(4), 2009.
- [8] H. Saitoh and H. Satoh, “Vibration Control of Flexible Robot Arm for Tip Mass Variations,” Proc. of the 55th Japan Automatic Control Conf., pp. 1721-1726, 2012.
- [9] T. Okazaki, M. Yamamoto, M. Komatsu, Y. Tsusaka, and Y. Adachi, “Development of a Human Safe, Multi-Degree-of-Freedom Robot Arm Technology using Pneumatic Muscles,” J. of the Robotics Society of Japan, Vol.28, No.3, pp. 302-310, 2010.
- [10] K. Nishibori and Y. Amano, “Torque Control of Robot Arm Using Magnetic Fluid Actuator,” Proc. of the 56th Japan Society of Mechanical Engineers Tokai Branch Conf., No.073-1, pp. 5-6, 2007.
- [11] R. Ozawa, H. Kobayashi, and R. Ishibashi, “Adaptive impedance control of a variable stiffness actuator,” Advanced Robotics, Vol.29, No.4, pp. 273-286, 2015.
- [12] S. Sugano, H. Iwata, and T. Sugiwa, “Appearance Design of Human-Symbiotic Robot TWENDY-ONE,” Proc. of the 2008 JSME Conf. on Robotics and Mechatronics, 2A1-D23(1)-2A1-D23(2), 2008.
- [13] T. Tsumugiwa, M. Yura, A. Kamiyoshi, and R. Yokogawa, “Development of Mechanical-Impedance-Varying Mechanism in Admittance Control,” J. Robot. Mechatron., Vol.30, No.6, pp. 863-872, 2018.
- [14] M. Zinn, B. Roth, O. Khatib, and J. K. Salisbury, “A New Actuation Approach for Human Friendly Robot Design,” The Int. J. of Robotics Research, Vol.23, No.4-5, pp. 379-398, 2004.
- [15] M. Zinn, O. Khatib, B. Roth, and J. K. Salisbury, “Workspace Haptic Devices – A New Actuation Approach,” Proc. of the IEEE Symp. on Haptic Interfaces for Virtual Environment and Teleoperator Systems, pp. 185-192, Reno, NV, USA, 2008.
- [16] K. Nishino, “Multifunctional New Alloys ‘Gum Metal’,” J. of the Society of Mechanical Engineers, Vol.106, No.1020, p. 899, 2003.
- [17] K. Hirai, H. Haneda, and S. Kitamura, “System control engineering,” Morikita Publishing, 1980.
This article is published under a Creative Commons Attribution-NoDerivatives 4.0 Internationa License.