Paper:
Development of Hydraulic Pump Drive System Using Switched Reluctance Motor with Servo Function
Ha Tham Phan*, Seiya Itagaki*, and Yasukazu Sato**
*Department of Mechanical Engineering, Graduate School of Engineering, Yokohama National University
79-5 Tokiwadai, Hodogaya-ku, Yokohama, Kanagawa 240-8501, Japan
Yokohama National University
79-5 Tokiwadai, Hodogaya-ku, Yokohama, Kanagawa 240-8501, Japan
A switched reluctance motor (SRM) generates a reluctance torque without the power of a permanent magnet, rendering it a candidate for rare-earth free motors. Compared with a permanent magnet synchronous motor (PMSM), SRMs also offer operational advantage in high-temperature environments owing to their robust structure. However, SRMs are generally inferior to PMSMs in terms of torque ripple, noise, and speed control, in particular. Therefore, this study attempts to improve the controllability of SRMs by proposing an SRM driving method in the form of a bidirectional rotation torque and a speed-controllable servomotor. The advantage of this method is evaluated experimentally using a closed-loop hydraulic system (valveless control system), which includes a hydraulic pump driven by an SRM to supply hydraulic power to actuators. The results show that the pump flow rate and hydraulic motor speed are consistent with the sinusoidal commands corresponding to the forward and reverse rotations of the SRM.
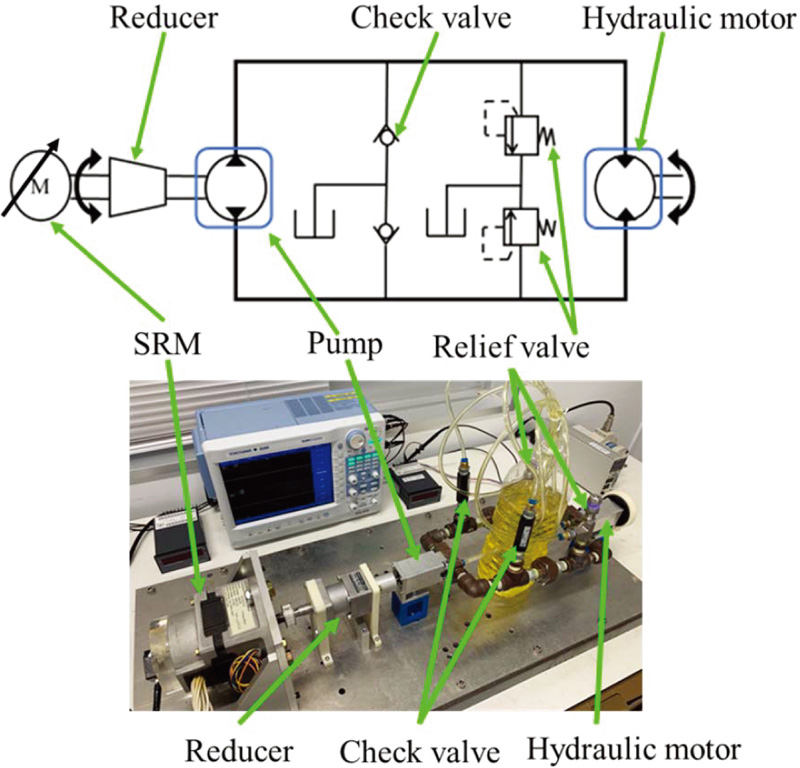
Bidirectional rotational speed control system of SRM with hydraulic pump/motor
- [1] H. Yamai, M. Kaneda, K. Ohyama,Y. Takeda, and N. Matsui, “Optimal Switched Reluctance Motor Drive for Hydraulic Pump Unit,” IEEE Conf. on Industry Applications, Vol.3, pp. 1555-1562, doi:10.1109/IAS.2000.882089, 2000.
- [2] R. Hamdy, J. Fletcher, and B. W. Williams, “Bidirectional Starting of a Symmetrical Two-Phase Switched Reluctance Machine,” IEEE Trans. on Energy Conversion, Vol.15, No.2, pp. 211-217, doi:10.1109/60.867002, 2000.
- [3] L. Gu, W. Wang, B. Fahimi, A. Clark, and J. Hearron, “Magnetic Design of Two-Phase Switched Reluctance Motor With Bidirectional Startup Capability,” IEEE Trans. on Industry Applications, Vol.52, No.3, pp. 2148-2155, doi:10.1109/TIA.2016.2514356, 2016.
- [4] S. Wei, S. Zhao, and J. Zheng, “Self-Tuning Fuzzy Control of Switched Reluctance Motor Directly-driven Hydraulic Press,” WRI World Congress on Software Engineering, Xiamen, pp. 461-465. doi:10.1109/WCSE.2009.164, 2009.
- [5] J. Ahn and G. F. Lukman, “Switched reluctance motor: Research trends and overview,” CES Trans. on Electrical Machines and Systems, Vol.2, No.4, pp. 339-347, doi:10.30941/CESTEMS.2018.00043, 2018.
- [6] T. J. E. Miller, “Switched Reluctance Motors and Their Control,” Clarendon Press, 1993.
- [7] B. Bilgin, J. W. Jiang, and A. Emadi, “Switched Reluctance Motor Drives – Fundamentals to Applications,” CRC Press, doi:10.1201/9780203729991, 2019.
- [8] T. Husain, W. Uddin, and Y. Sozer, “Performance Comparison of Short Pitched and Fully Pitched Switched Reluctance Machines Over Wide Speed Operations,” IEEE Energy Conversion Congress and Exposition (ECCE), doi:10.1109/TIA.2018.2839627, 2016.
- [9] K. Aiso and K. Akatsu, “High Speed SRM using vector Control for Electric Vehicle,” CES Trans. on Electrical Machines and Systems, Vol.4, No.1, pp. 61-68, doi:10.30941/CESTEMS.2020.00009, 2020.
- [10] H. Tanaka, H. Kaminaga, and Y. Nakamura, “Pressure feedback control based on singular perturbation method of an electro-hydrostatic actuator for an exoskeletal power-assist system,” J. Robot. Mechatron., Vol.24, No.2, pp. 354-362, 2012.
- [11] H. Zhang, X. Liu, J. Wang, and H. E. Karimi, “Robust H∞Sliding Mode Control with Pole Placement for a Fluid Power Electrohydraulic Actuator (EHA) System,” Int. J. of Advanced Manufacturing Technol., Vol.73, No.5, pp. 1095-1104, doi:10.1007/s00170-014-5910-8, 2014.
- [12] S. Hyo and S. Tanimoto, “Joint Torque Control of a Hydraulic Manipulator with Hybrid Servo Booster,” The 10th Japan Fluid Power System Society (JFPS) Int. Symp. on Fluid Power, 1C11-16, 2017.
- [13] K. Rongjie, J. Zongxia, W. Shaoping, and C. Lisha, “Design and Simulation of Electro-hydrostatic Actuator with a Built-in Power Regulator,” Chinese J. of Aeronautics, Vol.22, Issue 6, pp. 700-706, doi:10.1016/S1000-9361(08)60161-2, 2009.
- [14] Y. Wang, S. Guo, and H. Dong, “Modeling and Control of a Novel Electro-Hydrostatic Actuator with Adaptive Pump Displacement,” Chinese J. of Aeronautics, Vol.33, Issue 1, pp. 365-371, doi:10.1016/j.cja.2018.05.020, 2020.
- [15] T. Sourander, T. Minav, M. Pietola, and H. Hänninen, “Sensorless Position Control of Direct Driven Hydraulic Actuators,” The 10th Japan Fluid Power System Society (JFPS) Int. Symp. on Fluid Power, 2A10, doi:10.5739/jfpsij.11.26, 2017.
- [16] A. Navatha, K. Bellad, S. S. Hiremath, and S. Karunanidhi, “Dynamic Analysis of Electro Hydrostatic Actuation System,” Global Colloquium in Recent Advancement and Effectual Researches in Engineering, Science and Technology, Vol.25, pp.1289-1296, doi:10.1016/j.protcy.2016.08.223, 2016.
- [17] K. Tsuda, K. Umeda, I. Kota, S. Sakaino, and O. Tsuji, “Analysis on Rigidity of Hydraulic Hoses for Electro-Hydrostatic Actuators,” 43rd Annual Conf. of the IEEE Industrial Electronics Society, pp. 2828-2833 doi:10.1109/IECON.2017.8216477, 2017.
- [18] A. Navatha, S. S. Hiremath, S. Makaram, K. Subramaniam, and A. Talukdar, “Review on Electro Hydrostatic Actuator for Flight Control,” Int. J. of Fluid Power, Vol.17, No.2, pp. 125-145, doi:10.1080/14399776.2016.1169743, 2016.
- [19] Y. Sato, K. Murakami, and Y. Tsuboi, “Sensorless Torque and Thrust Estimation of a Rotational/Linear Two Degrees-of-Freedom Switched Reluctance Motor,” IEEE Trans. Magnetics, Vol.52, No.7, pp. 1-4, doi:10.1109/TMAG.2016.2536682, 2016.
- [20] Y. Sato, “Development of a 2-Degree-of-Freedom Rotational/Linear Switched Reluctance Motor,” IEEE Trans. Mag, Vol.43, No.6, pp. 2564-2566, doi:10.1109/TMAG.2007.892854, 2007.
This article is published under a Creative Commons Attribution-NoDerivatives 4.0 Internationa License.