Paper:
Disposable Robotic Finger Driven Pneumatically by Flat Tubes and a Hollow Link Mechanism
Junya Tanaka* and Nobuto Matsuhira**
*Corporate Research & Development Center, Toshiba Corporation
1 Komukai Toshiba-cho, Saiwai-ku, Kawasaki-shi, Kanagawa 212-8582, Japan
**Shibaura Institute of Technology
3-7-5 Toyosu, Koto-ku, Tokyo 135-8548, Japan
We propose a robotic finger with an exoskeleton-type structure that bends and extends by the deformation force of flat tubes. Our objective is to realize a disposable robot hand for gripping unsanitary objects. To reduce the cost of disposing of the robotic finger, a commercially available cable carrier chain was used for the exoskeleton component, and the flat tubes used in the pneumatic actuator were prepared by thermal processing of a commercially available tube. The driving joint of the robotic finger consists of a hollow link mechanism and two flat tubes, which are respectively arranged inside the hollow link mechanism and at the joint boundary. The proposed joint structure achieves both smooth drivability and good load-bearing capacity. The developed robotic finger weighs approximately 85 g and generates a fingertip force of approximately 4 N when a pressure of 0.25 MPa is applied. Because the developed robotic finger is pneumatically driven, it conforms to the object shape and is compliant to external force. Verification of the mechanism demonstrated that the developed robotic finger is useful because it was able to grasp six types of assumed objects.
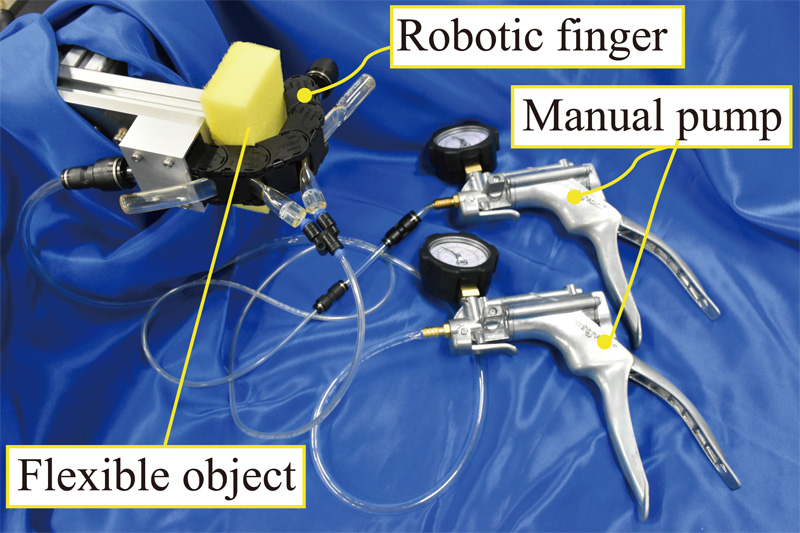
Developed disposable robotic finger
- [1] M. T. Mason and J. K. Salisbury, “Robot Hands and the Mechanics of Manipulation,” The MIT Press, 1985.
- [2] T. Watanabe, K. Yamazaki, and Y. Yokokohji, “Survey of robotic manipulation studies intending practical applications in real environments – object recognition, soft robot hand, and challenge program and benchmarking –,” Adv. Robot., Vol.31, Nos.19-20, pp. 1114-1132, 2017.
- [3] K. Tai, A.-R. El-Sayed, M. Shahriari, M. Biglarbegian, and S. Mahmud, “State of the Art Robotic Grippers and Applications,” Robotics, Vol.5, No.2, 11, 2016.
- [4] S. Hasegawa, K. Wada, K. Okada, and M. Inaba, “A Three-Fingered Hand with a Suction Gripping System for Warehouse Automation,” J. Robot. Mechatron., Vol.31, No.2, pp. 289-304, 2019.
- [5] A. D. Marchese, C. D. Onal, and D. Rus, “Autonomous soft robotic fish capable of escape maneuvers using fluidic elastomer actuators,” Soft Robotics, Vol.1, No.1, pp. 75-87, 2014.
- [6] A. D. Marchese and D. Rus, “Design, kinematics, and control of a soft spatial fluidic elastomer manipulator,” The Int. J. of Robotics Research, Vol.35, No.7, pp. 840-869, 2016.
- [7] C. Eppner, R. Deimel, J. Álvarez-Ruiz, M. Maertens, and O. Brock, “Exploitation of environmental constraints in human and robotic grasping,” The Int. J. of Robotics Research, Vol.34, No.7, pp. 1021-1038, 2015.
- [8] R. K. Katzschmann, A. D. Marchese, and D. Rus, “Autonomous object manipulation using a soft planar grasping manipulator,” Soft Robotics, Vol.2, No.4, pp. 155-164, 2015.
- [9] S. Kikuchi, Y. Yamada, R. Higashi, and T. Morita, “Super Multi-Joint Manipulator by Using Creased Plate and Pneumatic Actuators Arranged Antagonistically,” J. Robot. Mechatron., Vol.27, No.3, pp. 276-285, 2015.
- [10] H. F. Schulte, “The Characteristics of the McKibben Artificial Muscle,” National Research Council, “The Application of External Power in Prosthetics and Orthotics,” National Academy of Sciences, pp. 94-115, 1961.
- [11] K. Iwata, K. Suzumori, and S. Wakimoto, “Development of Contraction and Extension Artificial Muscles with Different Braid Angles and Their Application to Stiffness Changeable Bending Rubber Mechanism by Their Combination,” J. Robot. Mechatron., Vol.23, No.4, pp. 582-588, 2011.
- [12] A. Hitzmann, H. Masuda, S. Ikemoto, and K. Hosoda, “Anthropomorphic musculoskeletal 10 degrees-of-freedom robot arm driven by pneumatic artificial muscles,” Adv. Robot., Vol.32, No.15, pp. 865-878, 2018.
- [13] S. Kurumaya, K. Suzumori, H. Nabae, and S. Wakimoto, “Musculoskeletal lower-limb robot driven by multifilament muscles,” Robomech J., Vol.3, 18, 2016.
- [14] D. Nakanishi, Y. Sugimoto, H. Honda, and K. Osuka, “Measurement Experiments and Analysis for Modeling of McKibben Pneumatic Actuator,” J. Robot. Mechatron., Vol.28, No.6, pp. 830-836, 2016.
- [15] C. Ferraresi, W. Franco, and A. Bertetto, “Flexible Pneumatic Actuators: A Comparison between The McKibben and the Straight Fibres Muscles,” J. Robot. Mechatron., Vol.13, No.1, pp. 56-63, 2001.
- [16] T. Noritsugu, M. Kubota, and S. Yoshimatsu, “Development of Pneumatic Rotary Soft Actuator Made of Silicone Rubber,” J. Robot. Mechatron., Vol.13, No.1, pp. 17-22, 2001.
- [17] W. Felt, M. A. Robertson, and J. Paik, “Modeling vacuum bellows soft pneumatic actuators with optimal mechanical performance,” IEEE Int. Conf. on Soft Robotics (RoboSoft), pp. 534-540, 2018.
- [18] N. S. Usevitch, A. M. Okamura, and E. W. Hawkes, “APAM: Antagonistic pneumatic artificial muscle,” Proc. of IEEE Int. Conf. on Robotics and Automation (ICRA), pp. 1539-1546, 2018.
- [19] G. Belforte, G. Eula, A. Ivanov, and A. L. Visan, “Bellows textile muscle,” The J. of the Textile Institute, Vol.105, No.3, pp. 356-364, 2014.
- [20] J. Lee and H. Rodrigue, “Origami-based vacuum pneumatic artificial muscle with large contraction ratio,” Soft Robotics, Vol.6, No.1, pp. 109-117, 2019.
- [21] T. Yanagida, K. Adachi, and T. Nakamura, “Development of Bellows-Type Artificial Rubber Muscle and Application to Peristaltic Crawling Endoscopic Robot,” J. Robot. Mechatron., Vol.25, No.4, pp. 748-754, 2013.
- [22] H. Tsukagoshi, A. Kitagawa, and Y. Kamata, “Wearable Fluid Power Composed of Transformed Flat Tube Actuators,” IEEE/RSJ Int. Conf. on Intelligent Robots and Systems (IROS), pp. 1178-1183, 2002.
- [23] Y. Mori, H. Tsukagoshi, and A. Kitagawa, “Fluid Powered Ropeway: Self-Propelled Probe Sliding Along Flexible Tube,” J. Robot. Mechatron., Vol.23, No.2, pp. 215-224, 2011.
- [24] A. Dameitry and H. Tsukagoshi, “Lightweight and Large Force of Underactuated Pneumatic Two-Fingers with a Wide Range of Grasping,” Adv. Robot., Vol.31, Nos.23-24, pp. 1253-1266, 2017.
This article is published under a Creative Commons Attribution-NoDerivatives 4.0 Internationa License.