Paper:
Application of a MIMO-PID Controller for a Hydraulic Excavator Considering the Velocity of CoM
Masatoshi Kozui*, Toru Yamamoto*, Masaki Akiyama**, Kazushige Koiwai**, and Yoichiro Yamazaki**
*Graduate School of Advanced Science and Engineering, Hiroshima University
1-4-1 Kagamiyama, Higashi-hiroshima, Hiroshima 739-8527, Japan
**KOBELCO Construction Machinery Co., Ltd.
2-1 Itsukaichikou 2-chome, Saeki-ku, Hiroshima 731-5161, Japan
There are many machines that require human operation in industry, and high operational skills are required to operate these machines efficiently. However, the number of highly skilled workers is decreasing due to the recent trends of falling birthrate and population aging. This decline is particularly pronounced in the construction industry, while the demand for construction workers remains high owing to the increasing number of developed infrastructures. To reduce this mismatch between the supply and the demand, it is important to achieve high efficiency in tasks using hydraulic excavators, because these machines can greatly increase the productivity at construction sites. Accordingly, it is necessary to improve productivity even if unskilled operators use hydraulic excavators. This paper proposes a control system that achieves efficient motions based on the velocity of the center of mass (CoM) of the hydraulic excavator’s attachments, which reflects the characteristics of skilled workers’ operations. The motions of multiple attachments give rise to interference terms owing to the characteristics of the hydraulic system. A two-input two-output control system, in which the input consists of the lever input and the output is the CoM velocity is constructed. The fictitious reference iterative tuning (FRIT) method is used to calculate the controller parameters. The proposed method was verified by comparing the results of a simulated digging motion and an experiment with an actual hydraulic excavator operated by an unskilled operator.
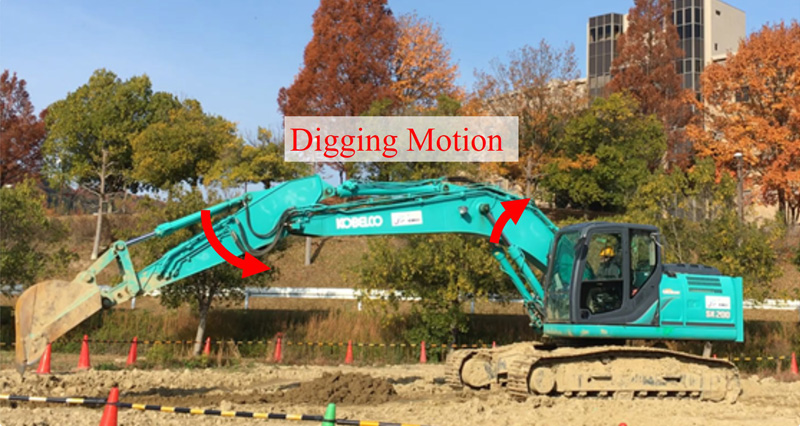
Digging operation of hydraulic excavator
- [1] S. Tsuneyama, S. Takeshita, H. Tsutsumi, and M. Shirosawa, “The practical usage of i-CONSTRUCTION for enhancing the safety of the construction site,” J. of Japan Society of Civil Engineers, Ser. F6 (Safety Problem), Vol.73, No.2, pp. I1-I6, 2017 (in Japanese).
- [2] K. Koiwai, Y. Liao, T. Yamamoto, T. Nanjo, Y. Yamazaki, and Y. Fujimoto, “Feature Extraction for Excavator Operation Skill Using CMAC,” J. Robot. Mechatron., Vol.28, No.5, pp. 715-721, 2016.
- [3] K. Ootsubo, D. Kato, T. Kawamura, and H. Yamada, “Support System for Slope Shaping Based on a Teleoperated Construction Robot,” J. Robot. Mechatron., Vol.28, No.2, pp. 149-157, 2016.
- [4] T. Tanimoto, R. Fukano, K. Shinohara, K. Kurashiki, D. Kondo, and H. Yoshinada, “Research on Superimposed Terrain Model for Teleoperation Work Efficiency,” J. Robot. Mechatron., Vol.28, No.2, pp. 173-184, 2016.
- [5] T. Hirabayashi, “Examination of Information Presentation Method for Teleoperation Excavator,” J. Robot. Mechatron., Vol.24, No.6, pp. 967-976, 2012.
- [6] H. Yoshinada, K. Okamura, and S. Yokota, “Master-Slave Control Method for Hydraulic Excavator,” J. Robot. Mechatron., Vol.24, No.6, pp. 977-984, 2012.
- [7] H. Muramoto, K. Tomita, and T. Morita, “Compliance Analysis of Construction Machinery Front by Direct Stiffness Method,” J. Robot. Mechatron., Vol.20, No.3, pp. 481-489, 2008.
- [8] H. Yamada, K. Takeichi, and T. Muto, “Sliding Mode Control of Hydraulic Power Shovel,” J. Robot. Mechatron., Vol.15, No.1, pp. 47-53, 2003.
- [9] S. Yokota, H. Kobayashi, R. Hirukawa, J. Tsumura, and E. Egawa, “Robust Trajectory Control of 3-axis Arm System of Hydraulic Excavators (The Effectiveness of the Control Using a Disturbance Observer),” Trans. of the Japan Society of Mechanical Engineers, Series C, Vol.66, No.648, pp. 2549-2556, 2000 (in Japanese).
- [10] M. Akiyama, M. Kozui, K. Koiwai, T. Yamamoto, K. Ueda, K. Yamashita, and Y. Yamazaki, “A Consideration on Extraction for Operating Skill Based on the Center of Mass for a Hydraulic Excavator,” IEEJ Proc. of Smart System and Control Technology Symp. 2018, pp. 1-4, 2018 (in Japanese).
- [11] M. Kozui, K. Koiwai, T. Yamamoto, K. Ueda, K. Yamashita, and Y. Yamazaki, “Construction of the Index to Evaluate the Operating Skill Based on the Motion of CoM for a Hydraulic Excavator,” IEEJ Trans. on Electronics, Information and Systems, Vol.139, No.4, pp. 388-394, 2019 (in Japanese).
- [12] Y. Oshima, T. Kinoshita, K. Koiwai, T. Yamamoto, T. Nanjo, Y. Yamazaki, and Y. Fujimoto, “Data-Driven Torque Controller for a Hydraulic Excavator,” J. Robot. Mechatron., Vol.28, No.5, pp. 752-758, 2016.
- [13] N. Hara, “Torque Control of a Redundant Manipulator Mounted On a Flexible Base Using the Pseudoinverse Matrix,” Proc. of the Japan Joint Automatic Control Conf., Vol.50, pp. 62-62, 2007.
- [14] K. Shigematsu, T. Tsubouchi, and S. Sarata, “Tip-over prevention control for teleoperated excavator based on CoG and ZMP prediction,” Trans. of the Japan Society of Mechanical Engineers, Vol.83, No.850, 17-00040, 2017.
- [15] S. Soma, O. Kaneko, and T. Fujii, “A new method of controller parameter tuning based on input-output data – Fictitious Reference Iterative Tuning(FRIT) –,” IFAC Workshop on Adaptation and Learning in Control and Signal Processing, and IFAC Workshop on Periodic Control Systems, Vol.37, No.12, pp. 789-794, 2004.
- [16] K. Hayashi and T. Yamamoto, “Design of a Data-Oriented Multivariable PID Control System,” IEEJ Trans. on Electronics, Information and Systems, Vol.133, No.12, pp. 2229-2235, 2013 (in Japanese).
- [17] T. Yamamoto, H. Ishihara, S. Omatsu, and T. Kitamori, “A Construction of Multivariable Self-Tuning Controller with Two-Degree-of-Freedom PID Structure for Discrete-Time System,” Trans. of the Society of Instrument and Control Engineers, Vol.28, No.4, pp. 484-491, 1992 (in Japanese).
- [18] Japan Fluid Power Association, “Practical hydraulic pocket book,” 2012 (in Japanese).
This article is published under a Creative Commons Attribution-NoDerivatives 4.0 Internationa License.