Paper:
HMI Design when Using Level 2 Automated Driving Function - Effects of System Status Presentation Considering the Risk of Malfunction on Driver Behavior –
Keisuke Suzuki, Joohyeong Lee, and Atsushi Kanbe
Kagawa University
2217-20 Hayashi-cho, Takamatsu-shi, Kagawa 761-0396, Japan
This study examined the effect of system status presentation on driver behavior when driving with ACC and LKA, which are classified as level 2 automated driving. First, we analyzed the driving behavior of 40 test participants in a driving simulator study under three HMI conditions: without safety level, correct safety level, and incorrect safety level which does not work properly and becomes inactive. The driver behavior database constructed in this experiment, was used to quantify the accident avoidance probability under each HMI condition using the state transition probabilistic model proposed by the author in a previous study. Finally, we quantified the degree of reduction in the probability of accident occurrence when using this HMI device in consideration of the risk of malfunction based on the integrated error model proposed by the author. Based on these results, it was shown that the HMI device that acts as a real-time interface at the system safety level between the driver and the automated driving using ACC and LKA is effective in reducing traffic accidents regardless of the increased probability of traffic accidents due to malfunctions of HMI device.
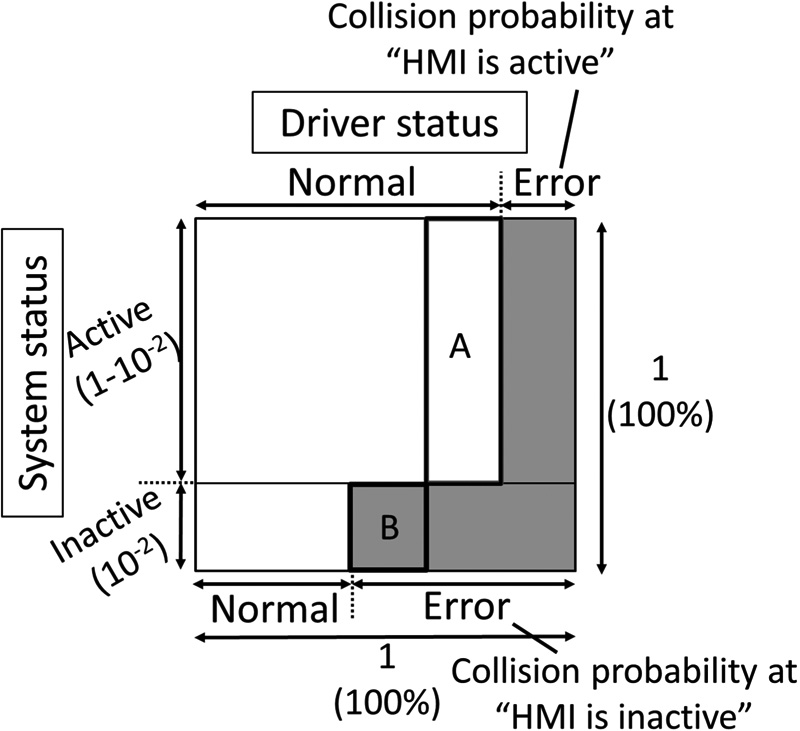
”Integrated Error Model” that estimates total errors as the human-machine system taking into account the risk of inactive of the system
- [1] SAE On-Road Automated Driving committee (ORAD), “J3016_201806, Taxonomy and Definitions for Terms Related to Driving Automation Systems for On-Road Motor Vehicles,” SAE Int. Ground Vehicle Standard, 2018.
- [2] H. Yoshida, M. Omae, and T. Wada, “Toward Next Active Safety Technology of Intelligent Vehicle,” J. Robot. Mechatron., Vol.27, No.6, pp. 610-616, 2015.
- [3] National Highway Traffic Safety Administration, “A Framework for Automated Driving System Testable Cases and Scenarios,” DOT HS 812 623, 2018.
- [4] N. Moray and T. Inagaki, “Laboratory studies of trust between humans and machines in automated systems,” Trans. of the Institute of Measurement and Control, Vol.21, Nos.4-5, pp. 203-211, 1999.
- [5] K. Suzuki, K. Kawatani, H. Mori, and Y. Sakaguchi, “Analysis of the driving behavior when the system safety level during automated driving is presented to drivers,” Mechanical Engineering J., The Japan Society of Mechanical Engineers, Vol.6, No.4, 19-00191, 2019.
- [6] K. Suzuki, “JSAE handbook, Human Factor,” Vol.3, JSAE, pp. 522-527, 2016 (in Japanese).
- [7] K. Suzuki and M. Mochizuki, “Acceptable System Error of Collision Avoidance System Based on the Integrated Error of Driver and System,” Proc. of 15th Int. Conf., HCI Int. 2013, Las Vegas, NV, USA, pp. 568-576, 2013.
- [8] S. Tsutsumi, T. Wada, T. Akita, and S. Doi, “A Method to Increase Drivers’ Trust in Collision Warning Systems Based on Reliability Information of Sensor,” Trans. of the Society of Instrument and Control Engineers. Vol.47, No.11, pp. 557-562, 2011 (in Japanese).
- [9] M. Ito, “Deceleration Meter for Enhancing Driver Situation Awareness and Understanding of Functional Limit of an Adaptive Cruise Control System,” Trans. of the Society of Instrument and Control Engineers, Vol.44, No.11, pp. 863-870, 2008 (in Japanese).
- [10] S. Nakamura, H. Suganuma, K. Kikuchi, and R. Homma, “Effect Evaluation of Vehicle-Infrastructure Cooperative Right-Turn Collision Prevention System,” Trans. of Society of Automotive Engineers of Japan, Vol.46, Issue 2, pp. 449-454, 2015 (in Japanese).
- [11] R. Honma, K. Kikuchi, T. Wakasugi, A. Uno, Y. Urai, and S. Uno, “Evaluation of Forward Vehicle Collision Mitigation Systems,” Trans. of Society of Automotive Engineers of Japan, Vol.45, Issue 2, pp. 393-398, 2014 (in Japanese).
- [12] K. Suzuki, H. Tanaka, Y. Miichi, and M. Aga, “Effectiveness of Collision-avoidance Support System Based on the Time Series Reliability Model,” Trans. of Society of Automotive Engineers of Japan, Vol.44, Issue 2, pp. 593-598, 2013 (in Japanese).
- [13] H. Jeong and P. Green, “SAE and ISO Standards for Warnings and other Interface Elements: A Summary,” Technical Report UMTRI-2013-16, The University of Michigan Transportation Research Institute (UMTRI), 2013.
- [14] Automobile Electronic Technology Association, “Study session on standardization related to new ITS technology,” 2002 (in Japanese).
- [15] M. Abe, “Vehicle Handling Dynamics,” Elsevier, 2009.
- [16] K. Suzuki and H. Jansson, “An analysis of driver’s steering behaviour during auditory or haptic warnings for the designing of lane departure warning system,” JSAE Review, Vol.24, Issue 1, pp. 65-70, 2003.
- [17] ISO/TC 22/SC 39 Ergonomics, “ISO/TR 21959-1:2018, Road vehicles – Human performance and state in the context of automated driving – Part 1: Common underlying concepts,” 2018.
- [18] ISO/TC22/SC32, Electrical and electronic components and general system aspects, “ISO 26262-7:2011 Road vehicles – Functional safety – Part 7: Production and operation,” 2011.
This article is published under a Creative Commons Attribution-NoDerivatives 4.0 Internationa License.