Paper:
PDMS Soft Skin Device with Deformable Micro-Diaphragm Array Fabricated with Rapid Substrate-Releasing Process
Hideyuki Mitsui*, Hiroshi Kashiwazaki**, and Takashi Mineta*
*Graduate School of Science and Engineering, Yamagata University
4-3-16 Jounan, Yonezawa, Yamagata 992-8510, Japan
**Faculty of Engineering, Yamagata University
4-3-16 Jounan, Yonezawa, Yamagata 992-8510, Japan
This paper describes the fabrication and characterization of a prototype wettability switching soft skin device that dynamically switches its surface morphology between flat and rough states. The device, which consists of a 1-μm-thick polydimethylsiloxane (PDMS) deformable diaphragm on a PDMS substrate with a micro-bump arrays, was successfully formed with a high fabrication yield by a novel method of device releasing from a dummy substrate. In buffered hydrofluoric acid (BHF) solution, a sacrificial layer of a novolak-resin-based resist was able to be rapidly released from the OH-terminated SiO2 surface of the dummy substrate, probably due to the breaking of hydrogen bonds at the interface. The wettability of the fabricated device was reversibly switched using micro-diaphragm deformation by varying the inner pressure. When a droplet was placed on the surface in the rough state, a large contact angle of approximately 140° was obtained, close to the Cassie mode with air in the concave-deformed PDMS micro-diaphragms, which indicated a high surface hydrophobicity. During cyclic switching between the rough and flat states after second switching, the contact angle reversibly changed between 106° and 120°, in good agreement with the Wenzel mode, where the micro-diaphragm surfaces were fully wet. Additionally, we observed that the droplet did not move even on the tilted device.
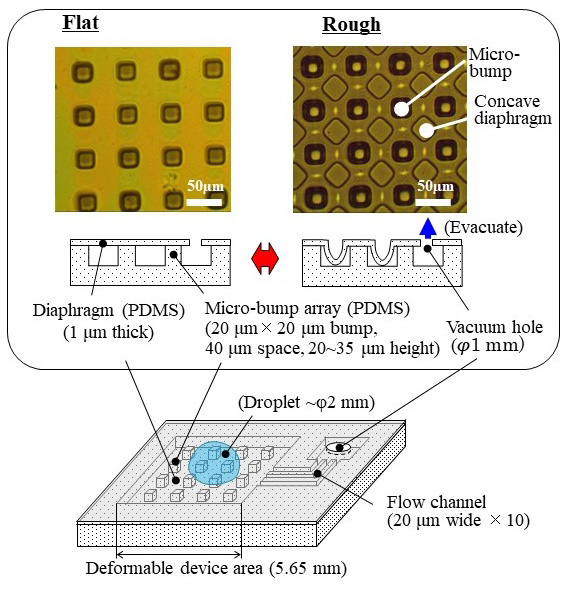
Soft skin device with deformable micro-diaphragm array
- [1] A. Nakajima, “Science and technology of hydrophobic solid surface,” J. Surface Finishing Soc. of Japan, Vol.60, No.1, pp. 2-8, 2009 (in Japanese).
- [2] S. K. Sethi and G. Manik, “Recent Progress in Super Hydrophobic/Hydrophilic Self-Cleaning Surfaces for Various Industrial Applications: A Review,” J. Polymer-Plastics Technol. and Eng., Vol.57, Issue 18, pp. 1932-1952, 2018.
- [3] C. F. Chen, S. C. Kuo, C. C. Chu, and F. G. Tseng, “Power-free liquid driven method for micro mixing application,” IEEE MEMS 2003, pp. 100-103, 2003.
- [4] A. Ghosh, R. Ganguly, T. M. Schutzius, and C. M. Megaridis, “Wettability patterning for high-rate, pumpless fluid transport on open, non-planar microfluidic platforms,” Lab on a Chip, Vol.14, No.9, pp. 1538-1550, 2014.
- [5] D. Öner and T. J. McCarthy, “Ultrahydrophobic surfaces. effect of topography length scale on wettability,” Langmuir, Vol.16, No.20, pp. 7777-7782, 2000.
- [6] L. Zhu, Y. Y. Feng, X. Y. Ye, and Z. Y. Zhou, “Tuning wettability and getting superhydrophobic surface by controlling surface roughness with well-designed microstructures,” Digest of Technical Papers, the 13th Int. Conf. on Solid-State Sensors, Actuators and Microsystems, 2005 (Transducers ’05), pp. 1481-1484, 2005.
- [7] Y. C. Jung and B. Bhushan, “Wetting transition of water droplets on superhydrophobic patterned surfaces,” Scripta Materialia, Vol.57, pp. 1057-1060, 2007.
- [8] S. Kobayashi, E. Makino, T. Mineta, and T. Komatsuzaki, “Effects of microstructure geometry and plasma modification on wetting properties of SU-8 surface,” Microelectronic Eng., Vol.88, No.8, pp. 1775-1778, 2011.
- [9] A. Nakajima, “Design of hydrophobic surfaces for liquid droplet control,” NPG Asia Materials, Vol.3, pp. 49-56, 2011.
- [10] J. Lee, B. He, and N. A. Patankar, “A roughness-based wettability switching membrane device for hydrophobic surfaces,” J. Micromech. and Microeng., Vol.15, No.3, pp. 591-600, 2005.
- [11] T. Mineta, S. Kobayashi, and S. Kobayashi, “Fabrication of deformable micro-pillar-array and dynamic wettability characterization,” Proc. of the 31st Sensor Symp. on Sensors, 21pm3-PS032, pp. 1-4, 2014 (in Japanese).
- [12] R. N. Wenzel, “Resistance of solid surfaces to wetting by water,” Industrial and Eng. Chemistry, Vol.28, No.8, pp. 988-994, 1936.
- [13] A. B. D. Cassie and S. Baxter, “Wettability of porous surfaces,” Trans. Faraday Soc., Vol.40, pp. 546-551, 1944.
- [14] J. Engel, J. Chen, and C. Liu, “Development of polyimide flexible tactile sensor skin,” J. Micromech. and Microeng., Vol.13, pp. 359-366, 2003.
- [15] D. R. Hines, N. P. Siwak, L. A. Mosher, and R. Ghodssi, “MEMS lithography and micromachining techniques,” R. Ghodssi and P. Lin (Eds.), “MEMS materials and Process Handbook,” pp. 667-753, Springer, 2011.
- [16] B. Bhushan, Y. C. Jung, and K. Koch, “Micro-, nano- and hierarchical structures for superhydrophobicity, self-cleaning and low adhesion,” Phil. Trans. R. Soc. A., Vol.367, pp. 1631-1672, 2009.
- [17] A. Nakajima, “Surface Wettability Control – Superhydrophilicity, superhydrophobicity and dynamic hydrophobicity –,” J. Surface Finishing Soc. of Japan, Vol.58, No.11, pp. 417-423, 2015 (in Japanese).
This article is published under a Creative Commons Attribution-NoDerivatives 4.0 Internationa License.