Paper:
Development of Lifting System for High-Elevation Inspection Robot Targeting Hanger Ropes
Yoshinori Fujihira, Naohiko Hanajima, Kentarou Kurashige, Hidekazu Kajiwara, and Masato Mizukami
Muroran Institute of Technology
27-1 Mizumoto-cho, Muroran, Hokkaido 050-8585, Japan
In this paper, we show the development of a lifting system and frame body for an inspection robot targeting hanger ropes of a suspension bridge. Infrastructure now requires regular inspection and such robots are expected to be used in places where manual inspection is difficult. The problems associated with the lifting system for the hanger-rope inspection robot studied in this paper include a long lifting distance (up to 100 m), postural stability against the influence of wind, and risk of falling. To solve these problems, we propose a lifting system with an alternating rotation mechanism, which takes advantage of the lifting mechanism of a climbing doll. In this paper, we explain the design and control methods of the lifting mechanism and alternating rotation hoist to realize the proposed lifting system. For the moving frame body, we designed and made a mechanism and frame structure to maintain stability of its posture. Performing an operation test in our laboratory and in the field with the proposed system incorporated into an actual unit, we checked the action of the proposed mechanism. In particular, we could confirm in the field test that the postural stability necessary for shooting inspection images could be ensured in an environment with wind speed of 5 m/s and that ascending and descending motions could be successfully performed with the current output of the alternating rotation hoist, even in an environment with a mean wind speed of 10 m/s.
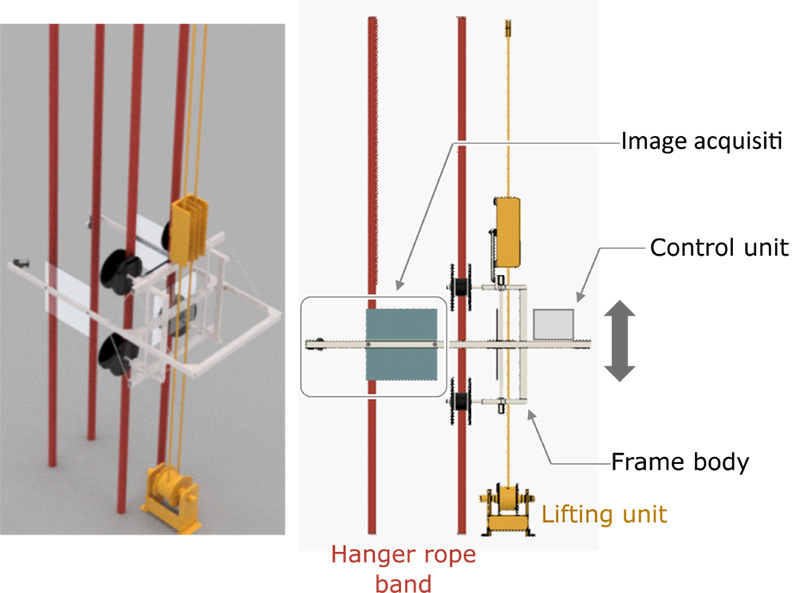
Developed inspection robot system
- [1] R. Takada and N. Oishi, “Priority issues of infrastructure inspection and maintenance robot: A part of COCN 2012 project “disaster response robot and its operational system”,” Proc. of 2013 IEEE Region 10 Humanitarian Technology Conf., pp. 166-171, doi: 10.1109/R10-HTC.2013.6669035, August 2013.
- [2] W. Guo, L. Soibelman, and J. H. Garrett, “Imagery enhancement and interpretation for remote visual inspection of aging civil infrastructure,” Tsinghua Sci and Tech., Vol.13, No.S1, pp. 375-380, doi: 10.1016/S1007-0214(08)70177-9, 2008.
- [3] N. Metni and T. Hamel, “A UAV for bridge inspection: Visual servoing control law with orientation limits,” Automation in Construction, Vol.17, No.1, pp. 3-10, doi: 10.1016/j.autcon.2006.12.010, 2007.
- [4] B. Chan, H. Guan, J. Jo, and M. Blumenstein, “Towards UAV-based bridge inspection systems: A review and an application perspective,” Structural Monitoring and Maintenance, Vol.2, No.3, pp. 283-300, doi: 10.12989/SMM.2015.2.3.283, 2015.
- [5] D. Schmidt and K. Berns, “Climbing robots for maintenance and inspections of vertical structures – A survey of design aspects and technologies,” Robotics and Autonomous Systems, Vol.61, No.12, pp. 1288-1305, doi: 10.1016/j.robot.2013.09.002, 2013.
- [6] R. T. Pack, J. L. Christopher, and K. Kawamura, “A Rubbertuator-based structure-climbing inspection robot,” Proc. of IEEE Int. Conf. on Robo. and Autom., Vol.1, pp. 1869-1874, doi: 10.1109/ROBOT.1997.619060, 1997.
- [7] M. Tavakoli, C. Viegas, L. Marques, J. N. Pires, and A. T. de Almeida, “OmniClimbers: Omni-directional magnetic wheeled climbing robots for inspection of ferromagnetic structures,” Robotics and Autonomous Systems, Vol.61, No.9, pp. 997-1007, doi: 10.1016/j.robot.2013.05.005, 2013.
- [8] X. Lu, R. Qiu, G. Liu, and F. Huang, “The design of an inspection robot for boiler tubes inspection,” Int. Conf. on Artificial Intelligence and Computational Intelligence (AICI) 2009, pp. 313-317, doi: 10.1109/AICI.2009.333, 2009.
- [9] M. Suzuki, T. Yukawa, Y. Satoh, and H. Okano, “Mechanisms of autonomous pipe-surface inspection robot with magnetic elements,” IEEE Int. Conf. on Systems, Man and Cybernetics (SMC) 2006, pp. 3286-3291, doi: 10.1109/ICSMC.2006.384625, 2006.
- [10] P. Kriengkomol, K. Kamiyama, M. Kojima, M. Horade, Y. Mae, and T. Arai, “A New Close-Loop Control Method for an Inspection Robot Equipped with Electropermanent-Magnets,” J. Robot. Mechatron., Vol.28, No.2, pp. 185-193, doi: 10.20965/jrm.2016.p0185, 2016.
- [11] S.-M. Moon, J. Huh, D. Hong, S. Lee, and C.-S. Han, “Vertical motion control of building façade maintenance robot with built-in guide rail,” Robotics and Computer-Integrated Manufacturing, Vol.31, pp. 11-20, doi: 10.1016/j.rcim.2014.06.006, 2015.
- [12] M. Sarieva, L. Yao, K. Sugawara, and T. Egami, “Synchronous Position Control of Robotics System for Infrastructure Inspection Moving on Rope Tether,” J. Robot. Mechatron., Vol.31, No.2, pp. 317-328, doi: 10.20965/jrm.2019.p0317, 2019.
- [13] F.-Y. Xu, X.-S. Wang, and L. Wang, “Climbing model and obstacle-climbing performance of a cable inspection robot for a cable-stayed bridge,” Trans. of the Canadian Society for Mechanical Engineering, Vol.35, No.2, pp. 269-289, doi: 10.1139/tcsme-2011-0016, 2011.
- [14] H.-B. Yun, S.-H. Kim, L. Wu, and J.-J. Lee, “Development of inspection robots for bridge cables,” The Scientific World J., Vol.2013, No.967508, p. 17, doi: 10.1155/2013/967508, 2013.
- [15] D. G. Lee, S. Oh, and H. I. Son, “Wire-driven parallel robotic system and its control for maintenance of offshore wind turbines,” IEEE Int. Conf. on Robotics and Automation (ICRA) 2016, pp. 902-908, doi: 2016, 10.1109/ICRA.2016.7487221, 2016.
- [16] M. Jeon, B. G. Kim, S. Park, and D. Hong, “Maintenance robot for wind power blade cleaning,” Proc. of the 29th Int. Symp. of Automation and Robotics in Construction (ISARC) 2012, 0081, 2012.
- [17] N. Elkmann, T. Felsch, and T. Förster, “Robot for rotor blade inspection,” Int. Conf. on Applied Robotics for the Power Industry (CARPI) 2010, pp. 1-5, doi: 10.1109/CARPI.2010.5624444, 2010.
- [18] H. Tsukagoshi, K. Fuchigami, E. Watari, and A. Kitagawa, “Deformable Anchor Ball for Thrown Referring to Octopus Suckers,” J. Robot. Mechatron., Vol.26, No.4, pp. 477-485, doi: 10.20965/jrm.2014.p0477, 2014.
- [19] S. Horii and T. Nakamura, “An In-Pipe Mobile Robot for Use as an Industrial Endoscope Based on an Earthworm’s Peristaltic Crawling,” J. Robot. Mechatron., Vol.24, No.6, pp. 1054-1062, doi: 10.20965/jrm.2012.p1054, 2012.
- [20] T. Kishi, M. Ikeuchi, and T. Nakamura, “Development of a Peristaltic Crawling Inspection Robot for Half-Inch Pipes Using Pneumatic Artificial Muscles,” SICE J. of Control, Measurement, and System Integration, Vol.8, No.4, pp. 256-264, doi: 10.9746/jcmsi.8.256, 2015.
- [21] Y. Fujihira, K. Buriya, S. Kaneko, T. Tsukida, N. Hanajima, and M. Mizukami, “Evaluation of Whole Circumference Image Acquisition System for a Long Cylindrical Structures Inspection Robot,” Proc. of the SICE Annual Conf. 2017, pp. 1108-1110, doi: 10.23919/SICE.2017.8105494, 2017.
- [22] H. Li, D. Harada, N. Hanajima, H. Kajiwara, K. Kurashige, Y. Fujihira, and M. Mizukami, “Application and performance evaluation of a lifting device with alternating rotation hoist,” 2016 IEEE/SICE Int. Symp. on System Integration (SII) 2016, pp. 385-390, doi: 10.1109/SII.2016.7844029, 2016.
This article is published under a Creative Commons Attribution-NoDerivatives 4.0 Internationa License.