Development Report:
Development of the Servo Valve with High Durability Using Split-Type Sleeve – Reduction of Wear with Ceramic Material –
Koki Sakakibara, Shunya Suzuki, Kazushi Shibata, Yuto Sawada, Satoshi Ashizawa, and Takeo Oomichi
Meijo University
1-501 Shiogamaguchi, Tempaku-ku, Nagoya, Aichi 468-8502, Japan
Reduction of leakage is a major problem in water hydraulic systems. With a servo valve, it is possible to reduce the internal leakage by reducing the clearance between a spool and a sleeve. However, because the clearance is reduced, wear tends to occur easily between the spool and sleeves when the servo valve is driven. As a result, the durability of the servo valve is reduced. Attention is paid to the durability against wear of ceramic materials, and the wear can be suppressed by using ceramics as the materials of the spool and sleeve. Thus, one can check whether the wear between the spool and sleeve can be suppressed, thereby improving the durability of the servo valve.
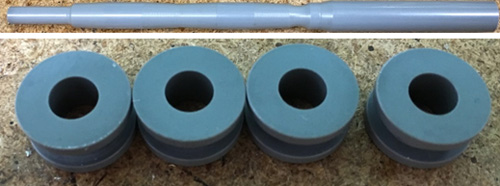
Picture of ceramics spool and sleeve
- [1] K. Yoshida, “Kensetsu kikai ni okeru yuatu gijutu no sinpo [Advances in hydraulic technology in construction machinery],” Trans. of the JSME, Vol.78, No.677, pp. 305-310, 1975 (in Japanese).
- [2] T. Ohgi and Y. Yokokohji, “Control of Hydraulic Actuator Systems Using Feedback Modulator,” J. Robot. Mechatron., Vol.20, No.5, pp. 695-708, 2008.
- [3] K. Izawa and S.-H. Hyon, “Prototyping Force-Controlled 3-DOF Hydraulic Arms for Humanoid Robots,” J. Robot. Mechatron., Vol.28, No.1, pp. 95-103, 2016.
- [4] A. Irawan and K. Nonami, “Compliant Walking Control for Hydraulic Driven Hexapod Robot on Rough Terrain,” J. Robot. Mechatron., Vol.23, No.1, pp. 149-162, 2011.
- [5] H. Kuwano, “Damping Control of Direct-Driven Servo Valve Using an Observer,” J. Robot. Mechatron., Vol.1, No.3, pp. 168-173, 1989.
- [6] M. Paloniitty and M. Linjama, “High-Linear Digital Hydraulic Valve Control by an Equal Coded Valve System and Novel Switching Schemes,” Proc. of the Institution of Mechanical Engineers, Part I, J. of Systems and Control Engineering, Vol.232, No.3, pp. 258-269, 2018.
- [7] K. Iwata, K. Suzumori, and S. Wakimoto, “A Method of Designing and Fabricating Mckibben Muscles Driven by 7 MPa Hydraulics,” Int. J. Automation Technol., Vol.6, No.4, pp. 482-487, 2012.
- [8] T. Kikuchi, R. Fujino, K. Igarashi, and K. Koganezawa, “Non-Energized Above Knee Prosthesis Enabling Stairs Ascending and Descending with Hydraulic Flow Controller,” J. Robot. Mechatron., Vol.30, No.6, pp. 892-899, 2018.
- [9] E. Urata, S. Miyagawa, C. Yamashina, Y. Nakao, Y. Usami, and M. Sinoda, “Development of a Water Hydraulic Servo Valve,” JSME Int. J. Ser. B, Fluids and Thermal Engineering, Vol.41, No.2, pp. 286-294, 1998.
- [10] M. A. Elgami, S. A. Kassem, and H. Kanai, “Performance of Single Stage Four Nozzles Pintle Type Hydraulic Servovalves,” JSME Int. J. Ser. C, Mechanical Systems, Machine Elements and Manufacturing, Vol.42, No.2, pp. 328-334, 1999.
- [11] E. Urata and C. Yamashina, “Influence of Flow Force on the Flapper of a Water Hydraulic Servovalve,” JSME Int. J. Ser. B, Fluids and Thermal Engineering, Vol.41, No.2, pp. 278-285, 1998.
- [12] E. Urata and Y. Nakao, “Study of a Flapper-Nozzle System for a Water Hydraulic Servovalve,” JSME Int. J. Ser. B, Fluids and Thermal Engineering, Vol.41, No.2, pp. 270-277, 1998.
- [13] K. Suzuki, S. Akazawa, and Y. Nakao, “Development of Cam-Drive Type Proportional Valve for Water Hydraulics,” Int. J. Automation Technol., Vol.6, No.4, pp. 450-456, 2012.
- [14] F. Majdič, J. Pezdirnik, and M. Kalin, “Comparative tribological investigations of continuous control valves for water hydraulics,” The 10th Scadinavian Int. Conf. on Fluid Power (SICFP’07), Tempere, Finland, May 21-23, 2007.
- [15] M. Takashima, K. Saki, A. Yuge, and A. Tanaka, “Development of High Performance Components for Pollution Free Water Hydraulic System,” Proc. of the JFPS Int. Symp. on Fluid Power, Vol.1996, No.3, pp. 49-54, 1996.
- [16] P. N. Pham, K. Ito, and S. Ikeo, “Energy Saving for Water Hydraulic Pushing Cylinder in Meat Slicer,” Int. J. of Fluid Power System, Vol.10, No.2, pp. 24-29, 2017.
- [17] T. Oomichi and A. Tanaka, “Development of Water hydraulic Sensor Control System Considering Water Characteristics,” Thesis of Japan Society of Mechanical Engineers, Ser. C, Vol.62, No.599, pp. 96-103, 1996.
- [18] T. Watanabe, T. Inayama, and T. Oomichi, “Development of the Small Flow Rate Water Hydraulic Servo Valve,” J. Robot. Mechatron., Vol.22, No.3, 2010.
- [19] T. Watanabe, I. Tomokazu, and T. Oomichi, “Design Concept of small flow rate servo valve for water hydraulic system,” 2009 IEEE/SICE Int. Symp. on System Integration (SII), pp. 1-6, 2009.
- [20] P. N. Pham, K. Ito, and S. Ikeo, “Control and energy performances of water hydraulic FST and PMT systems,” Mechanical Engineering J., Vol.1, No.4, FE003, 2014.
- [21] H.-C. Wong, N. Umehara, K. Kato, and K. Nii, “Fundamental Study of Water-Lubricated Ceramic Bearings,” Trans. of the Japan Society of Mechanical Engineers, C, Vol.61, Issue 590, pp. 4027-4032, 1995.
- [22] Y. Mizutani, Y. Shimura, Y. Yahagi, and S. Horita, “Tribology in ceramics,” R&D Review of Toyota CRDL, Vol.27, No.2, pp. 11-21, 1992 (in Japanese).
- [23] Japanese Society of Tribologists, “Seramikkusu no toraiboroji [Tribology in ceramics],” Yokendo Co., Ltd., pp. 13-14, 2003 (in Japanese).
- [24] H. Hashimoto, “Kiso kara manabu toraibooroji [Tribology learned from the basics],” Morikita Publishing Co., Ltd., pp. 53-56, 2006 (in Japanese).
- [25] Y. Kamiya, K. Sakamoto, and T. Oomichi, “Research of the low leakage servo valve by long overlapfor water hydraulic system,” SICE System Integration Division, 1D1-6, 2011.
- [26] S. Ashizawa, T. Watanabe, Y. Kamiya, H. Aoki, and T. Oomichi, “Development of the Energy Simulator for the Water Hydraulic System Under Flow Condithion Changes,” J. Robot. Mechatron., Vol.23, No.3, pp. 416-425, 2011.
This article is published under a Creative Commons Attribution-NoDerivatives 4.0 Internationa License.