Paper:
Energy-Saving High-Speed Pick-and-Place Robot Using In-Frame Parallel Spring
Jumpei Arata*1, Yuji Isogai*2, Junya Sumida*2, Masamichi Sakaguchi*2, Ryu Nakadate*3, Susumu Oguri*4, and Makoto Hashizume*3
*1Department of Mechanical Engineering, Faculty of Engineering, Kyushu University
744 Motooka, Nishi-ku, Fukuoka 819-0395, Japan
*2Department of Engineering Physics, Electronics and Mechanics, Graduate School of Engineering, Nagoya Institute of Technology
Gokiso-cho, Showa-ku, Nagoya 466-8555, Japan
*3Center for Advanced Medical Innovation, Kyushu University
3-1-1 Maidashi, Higashi-ku, Fukuoka 812-8582, Japan
*4Innovation Center for Medical Redox Navigation, Kyushu University
3-1-1 Maidashi, Higashi-ku, Fukuoka 812-8582, Japan
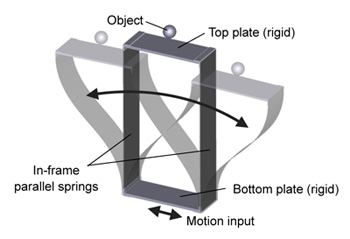
Concept prototype
- [1] Research and Development Association for Future Electron Devices, “Actual state and near-future trend survey of power consumption of electric devices,” p. 42, 2009 (in Japanese).
- [2] N. Takesue, T. Ikematsu, H. Murayama, and H. Fujimoto, “Design and Prototype of Variable Gravity Compensation Mechanism (VGCM),” J. of Robotics and Mechatronics, Vol.23, No.2, pp. 249-257, 2011.
- [3] M. Plooij and M. Wisse, “A Novel Spring Mechanism to Reduce Energy Consumption of Robotic Arms,” Proc. of Int. Conf. on Intelligent Robots And Systems, pp. 2901-2908, 2012.
- [4] G. Lu, S. Kawamura, and M. Uemura, “Proposal of an Energy Saving Control Method for SCARA Robots,” J. of Robotics and Mechatronics, Vol.24, No.1, pp. 115-122, 2012.
- [5] V. I. Babitsky and A. V. Shipilov, “Resonant Robotic Systems,” Springer, 2003. ISBN: 978-3-540-36380-4
- [6] L. L. Howell, “Compliant mechanisms,” Wiley-Interscience, 2001.
- [7] S. T. Smith, “Flexures Elements of Elastic Mechanisms,” CRC Press, 2000.
- [8] N. Lobontiu, “Compliant mechanisms,” CRC Press, 2002.
- [9] H. Kozuka, J. Arata, K. Okuda, A. Onaga, M. Ohno, A. Sano, and H. Fujimoto, “A Bio-Inspired Compliant-Parallel Mechanism for High Precision Robot,”Proc. of Int. Conf. on Robotics and Automation, pp. 3122-3127, 2012.
- [10] H. Kozuka, J. Arata, K. Okuda, A. Onaga, M. Ohno, A. Sano, and H. Fujimoto, “Compliant-Parallel Mechanism for High Precision Machine with a Wide Range of Working Area,” Proc. of Int. Conf. on Intelligent Robots And Systems, pp. 2519-2524, 2012.
- [11] J. P. Merlet, “Parallel Robots Second Edition,” Springer, 2006. ISBN: 1-4020-4132-2
- [12] Y. Muranaka, M. Inaba, T. Asano, and E. Furukawa, “Parasitic Rotation in Parallel Spring Movements,” J. Japan Society for Precision Engineering, pp. 1671-1676, 1990 (in Japanese).
This article is published under a Creative Commons Attribution-NoDerivatives 4.0 Internationa License.