Research Paper:
Single Neuron PID-Based Heave Compensation Control for Drill String System in Oceanic Drilling
Jing Ren*1,*2,*3
, Chengda Lu*2,*3,*4,
, Chenxuan Wang*1,*2,*3
, Zhejiaqi Ma*2,*3,*4
, Chao Gan*2,*3,*4
, Fulong Ning*2,*3,*5
, and Min Wu*1,*2,*3,*4

*1School of Future Technology, China University of Geosciences
No.388 Lumo Road, Hongshan District, Wuhan, Hubei 430074, China
*2Hubei Key Laboratory of Advanced Control and Intelligent Automation for Complex Systems
No.388 Lumo Road, Hongshan District, Wuhan, Hubei 430074, China
*3Engineering Research Center of Intelligent Technology for Geo-Exploration, Ministry of Education
No.388 Lumo Road, Hongshan District, Wuhan, Hubei 430074, China
*4School of Automation, China University of Geosciences
No.388 Lumo Road, Hongshan District, Wuhan, Hubei 430074, China
*5Faculty of Engineering, China University of Geosciences
No.388 Lumo Road, Hongshan District, Wuhan, Hubei 430074, China
Corresponding author
During offshore exploration operations, vessels experience six degrees of freedom motion due to wind, waves, and currents. Among these motions, heave is particularly challenging to compensate for and significantly impacts the drilling process. This paper presents an active heave compensation control method for drill string systems in offshore exploration. To address parameter uncertainties, a single-neuron PID control approach based on a quadratic performance index is proposed. A simulation analysis was conducted using MATLAB software. The results demonstrate that the proposed controller provides smoother outputs than alternative controllers, highlighting its effectiveness in heave compensation.
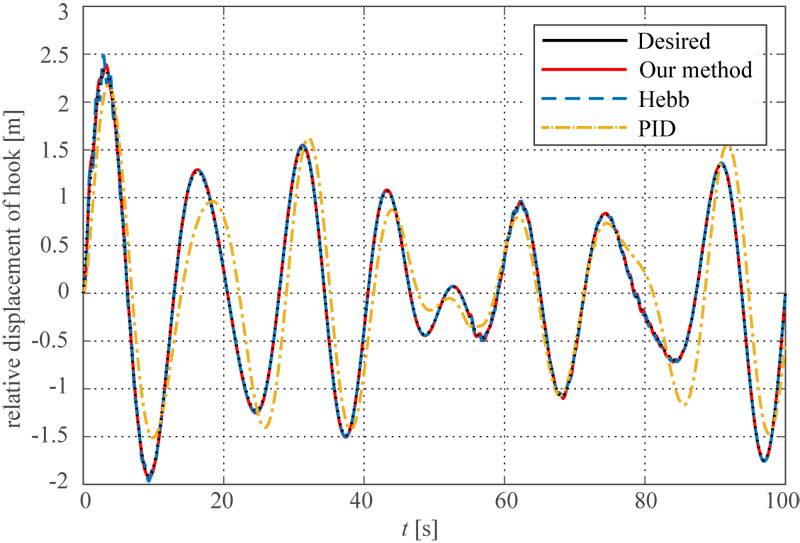
Tracking performance of different controllers
- [1] Q. He and P. Wang, “Current situation and prospect of deep-sea energy development,” Ocean Development and Management, Vol.34, No.12, pp. 66-71, 2017.
- [2] L. Ma, Y.-L. Wang, and Q.-L. Han, “Event-triggered dynamic positioning for mass-switched unmanned marine vehicles in network environments,” IEEE Trans. on Cybernetics, Vol.52, No.5, pp. 3159-3171, 2020. https://doi.org/10.1109/TCYB.2020.3008998
- [3] W. H. C. Sánchez, E. L. F. Fortaleza, A. B. Neto, and J. A. R. Vargas, “Effects of nonlinear friction of passive heave compensator on drilling operation—Part II: Active robust control,” Ocean Engineering, Vol.227, Article No.108837, 2021. https://doi.org/10.1016/j.oceaneng.2021.108837
- [4] J. K. Woodacre, R. J. Bauer, and R. A. Irani, “A review of vertical motion heave compensation systems,” Ocean Engineering, Vol.104, pp. 140-154, 2015. https://doi.org/10.1016/j.oceaneng.2015.05.004
- [5] B. Helian, C. Zheng, and B. Yao, “Energy-saving and accurate motion control of a hydraulic actuator with uncertain negative loads,” Chinese J. of Aeronautics, Vol.34, No.5, pp. 253-264, 2021. https://doi.org/10.1016/j.cja.2020.12.025
- [6] F. Zhao, Y. Zhong, and Z. Fu, “Active and passive heave compensation system based on feedback linearization sliding mode variable structure control,” Ocean Engineering, Vol.305, Article No.117962, 2024. https://doi.org/10.1016/j.oceaneng.2024.117962
- [7] Z. Xu, C. Sun, X. Hu, Q. Liu, and J. Yao, “Barrier Lyapunov function-based adaptive output feedback prescribed performance controller for hydraulic systems with uncertainties compensation,” IEEE Trans. on Industrial Electronics, Vol.70, No.12, pp. 12500-12510, 2023. https://doi.org/10.1109/TIE.2023.3236114
- [8] W. Yang, S. Li, Z. Li, and X. Luo, “Highly accurate manipulator calibration via extended Kalman filter-incorporated residual neural network,” IEEE Trans. on Industrial Informatics, Vol.19, No.11, pp. 10831-10841, 2023. https://doi.org/10.1109/TII.2023.3241614
- [9] Y. Zhang, Y. Sun, Z. Hu, B. Fang, Y. Xie, L. Chen, and Y. Teng, “Control performance analysis of mining ship heave compensation system based on fuzzy logic algorithm,” J. Européen des Systèmes Automatisés, Vol.55, No.2, pp. 213-220, 2022. https://doi.org/10.18280/jesa.550208
- [10] X. Yan, F. Yan, D. Zhao, and S. Li, “Speed control of secondary regulation heave compensation based on fuzzy PID,” J. of Physics: Conf. Series, Vol.2419, No.1, Article No.012058, 2023. https://doi.org/10.1088/1742-6596/2419/1/012058
- [11] L. Hu, M. Zhang, Z.-M. Yuan, H. Zheng, and W. Lv, “Predictive control of a heaving compensation system based on machine learning prediction algorithm,” J. of Marine Science and Engineering, Vol.11, No.4, Article No.821, 2023. https://doi.org/10.3390/jmse11040821
- [12] P. Zhu, Q. Zhang, Z. Zhao, and B. Yang, “BP fuzzy neural network PID based constant tension control of traction winch,” Measurement and Control, Vol.56, Nos.3-4, pp. 857-873, 2023. https://doi.org/10.1177/00202940221094850
- [13] J. Liu and X. Chen, “Adaptive control based on neural network and beetle antennae search algorithm for an active heave compensation system,” Int. J. of Control, Automation and Systems, Vol.20, No.2, pp. 515-525, 2022. https://doi.org/10.1007/s12555-020-0615-2
- [14] J. Lei, H. Li, W. Tang, Y. Tian, Q. Yang, and S. Cao, “AMESim-based study on control method and simulation of drill string compensation system,” Chinese Hydraulics & Pneumatics, Vol.0, No.10, p. 83, 2019. https://doi.org/10.11832/j.issn.1000-4858.2019.10.014
- [15] W. H. C. Sánchez, A. B. Neto, and E. L. F. Fortaleza, “Effects of nonlinear friction of passive heave compensator on drilling operation—Part I: Modeling and analysis,” Ocean Engineering, Vol.213, Article No.107743, 2020. https://doi.org/10.1016/j.oceaneng.2020.107743
- [16] J. Xu, B. Yi, and Y. Zhan, “Review of heave compensation systems: Design and control strategies,” 2023 IEEE 11th Int. Conf. on Computer Science and Network Technology (ICCSNT), pp. 406-413. 2023. https://doi.org/10.1109/ICCSNT58790.2023.10334591
- [17] T. Xu, Q. Liu, J. Dai, and W. Li, “Design and simulation analysis of new semi-active and multiplication process heave compensation device,” China Mechanical Engineering, Vol.27, No.5, p. 663, 2016.
- [18] H. Li, J. Fu, S. Fan, T. Chen, P. Li, and W. Zheng, “Simulation on drill string compensation device based on heave prediction,” China Petroleum Machinery, Vol.49, No.3, pp. 57-64, 2021.
- [19] F. Ding, W. Zhang, X. Luo, L. Hu, Z. Zhang, M. Wang, H. Li, M. Peng, X. Wu, L. Hu, and T. Zhang, “Gain self-adjusting single neuron PID control method and experiments for longitudinal relative position of harvester and transport vehicle,” Computers and Electronics in Agriculture, Vol.213, Article No.108215, 2023. https://doi.org/10.1016/j.compag.2023.108215
- [20] P. Rezaei, H. P. Aria, and M. Ayati, “LQR based optimal passive fault-tolerant nonlinear fractional-order PID,” 2021 16th Int. Conf. on Engineering of Modern Electric Systems (EMES), pp. 1-4. 2021. https://doi.org/10.1109/EMES52337.2021.9484123
This article is published under a Creative Commons Attribution-NoDerivatives 4.0 Internationa License.