Research Paper:
Condition Recognition Method with Information Granulation for Burden Distribution in Blast Furnace
Yuanfeng Huang*1,*2
, Sheng Du*1,*2,*3
, Jie Hu*1,*2,*3
, Witold Pedrycz*4,*5
, and Min Wu*1,*2,*3,

*1School of Automation, China University of Geosciences
No.388 Lumo Road, Hongshan District, Wuhan 430074, China
*2Hubei Key Laboratory of Advanced Control and Intelligent Automation for Complex Systems
No.388 Lumo Road, Hongshan District, Wuhan 430074, China
*3Engineering Research Center of Intelligent Technology for Geo-Exploration, Ministry of Education
No.388 Lumo Road, Hongshan District, Wuhan 430074, China
*4Department of Electrical and Computer Engineering, University of Alberta
Edmonton, Alberta T 2, Canada
*5Systems Research Institute, Polish Academy of Sciences
Warsaw , Poland
Corresponding author
The operating conditions influence the stability and consumption of a blast furnace. Recognizing these conditions makes changing the burden distribution parameters more efficient. The cooling stave temperature (CST) is a crucial state parameter that indicates the conditions of the process. Owing to the high data volume of the CST and the lack of methods for recognizing the stability of the slag crust, it is difficult for operators to recognize the conditions accurately according to the CST during the ironmaking process. Thus, in this study, a condition recognition method with information granulation for burden distribution in a blast furnace was presented. First, information granulation was employed to reduce the volume of the CST data and present it in a granular form. Then, considering the lack of a method for calculating the similarity of CST information granules, a novel fuzzy similarity calculation method was devised to calculate the membership grades of information granules belonging to different standard granules. Finally, the conditions were recognized according to the membership values. Experimental results based on industrial data demonstrated that the proposed method can be used to recognizes the conditions in the blast furnace.
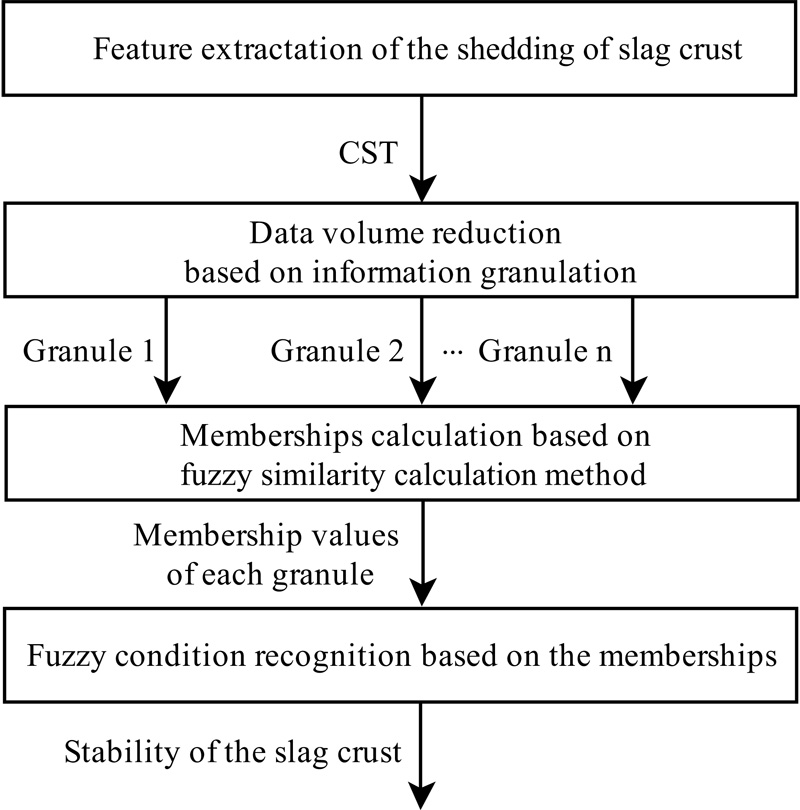
Condition recognition framework with information granulation for the blast furnace
- [1] Z. Zhang, Y. Lu, X. Wang, C. Cheng, and C. Gao, “A data-based compact high-order volterra model for complex blast furnace system,” IEEE Trans. on Industrial Informatics, Vol.18, No.9, pp. 5827-5837, 2022. https://doi.org/10.1109/TII.2021.3131604
- [2] P. Zhou, H. D. Song, H. Wang, and T. Y. Chai, “Data-driven nonlinear subspace modeling for prediction and control of molten iron quality indices in blast furnace ironmaking,” IEEE Trans. Control System Technology, Vol.25, No.5, pp. 1761-1774, 2017. https://doi.org/10.1109/TCST.2016.2631124
- [3] Y. Li, S. Zhang, J. Zhang, Y. Yin, W. Xiao, and Z. Zhang, “Data-Driven Multiobjective Optimization for Burden Surface in Blast Furnace with Feedback Compensation,” IEEE Trans. on Industrial Informatics, Vol.16, No.4, pp. 2233-2244, 2020. https://doi.org/10.1109/TII.2019.2908989
- [4] P. Zhou, Y. Lv, H. Wang, and T. Chai, “Data-driven robust RVFLNs modeling of a blast furnace iron-making process using Cauchy distribution weighted M-estimation,” IEEE Trans. on Industrial Electronics, Vol.64, No.9, pp. 7141-7151, 2017. https://doi.org/10.1109/TIE.2017.2686369
- [5] P. Zhou, R. Zhang, J. Xie, J. Liu, H. Wang, and T. Chai, “Data-driven monitoring and diagnosing of abnormal furnace conditions in blast furnace ironmaking: An integrated PCA-ICA method,” IEEE Trans. on Industrial Electronics, Vol.68, No.1, pp. 622-631, 2021. https://doi.org/10.1109/TIE.2020.2967708
- [6] J. Hu, M. Wu, X. Chen, S. Du, P. Zhang, W. Cao, and J. She, “A Multilevel Prediction Model of Carbon Efficiency Based on the Differential Evolution Algorithm for the Iron Ore Sintering Process,” IEEE Trans. on Industrial Electronics, Vol.65, No.11, pp. 8778-8787, 2018. https://doi.org/10.1109/TIE.2018.2811371
- [7] M. Wu, K. Zhang, J. An, J. She, and K.-Z. Liu, “An energy efficient decision-making strategy of burden distribution for blast furnace,” Control Engineering Practice, Vol.78, pp. 196-195, 2018. https://doi.org/10.1016/j.conengprac.2018.06.019
- [8] C. Yilmaz and T. Tureka, “Modeling and simulation of the use of direct reduced iron in a blast furnace to reduce carbon dioxide emissions,” J. of Cleaner Production, Vol.164, pp. 1519-1530, 2017. https://doi.org/10.1016/j.jclepro.2017.07.043
- [9] P. Azadi, J. Winz, E. Leo, R. Klock, and S. Engell, “A hybrid dynamic model for the prediction of molten iron and slag quality indices of a large-scale blast furnace,” Computers and Chemical Engineering, Vol.156, Article No.107573, 2022. https://doi.org/10.1016/j.compchemeng.2021.107573
- [10] Y. Huang, X. Lai, K. Zhang, J. An, and M. Wu, “Two-stage decision-making method for burden distribution based on recognition of conditions in blast furnace,” IEEE Trans. on Industrial Electronics, Vol.68, No.5, pp. 4199-4208, 2021. https://doi.org/10.1109/TIE.2020.2982121
- [11] Y. Hu, C. Ji, Q. Zhang, L. Chen, P. Zhan, and X. Li, “A novel multi-resolution representation for time series sensor data analysis,” Soft Computing, Vol.24, pp. 10535-10560, 2020. https://doi.org/10.1007/s00500-019-04562-7
- [12] T.-Y. Lee and H.-W. Shen, “Efficient local statistical analysis via integral histograms with discrete wavelet transform,” IEEE Trans. on Visualization and Computer Graphics, Vol.19, No.12, pp. 2693-2702, 2013. https://doi.org/10.1109/TVCG.2013.152
- [13] W. Lu, X. Chen, W. Pedrycz, X. Liu, and J. Yang, “Using interval information granules to improve forecasting in fuzzy time series,” Int. J. of Approximate Reasoning, Vol.57, 2015. https://doi.org/10.1016/j.ijar.2014.11.002
- [14] S. Du, M. Wu, L.-F. Chen, and W. Pedrycz, “Operating performance assessment based on granular clustering for iron ore sintering process,” Acta Automation Sinica, Vol.49, No.2, 2023. https://doi.org/10.16383/j.aas.c200267
- [15] Y. Zhou, H. Ren, Z. Li, and W. Pedrycz, “An anomaly detection framework for time series data: An interval-based approach,” Knowledge-Based Systems, Vol.228, Article No.107153, 2021. https://doi.org/10.1016/j.knosys.2021.107153
- [16] Y. Zhou, H. Ren, Z. Li, and W. Pedrycz, “Anomaly detection based on a granular markov model,” Expert Systems with Applications, Vol.187, Article No.115744, 2022. https://doi.org/10.1016/j.eswa.2021.115744
- [17] J. An, X. Shen, M. Wu, and J. She, “A multi-time-scale fusion prediction model for the gas utilization rate in a blast furnace,” Control Engineering Practice, Vol.92, Article No.104120, 2019. https://doi.org/10.1016/j.conengprac.2019.104120
- [18] Y. Zhang, P. Zhou, D. Lv, S. Zhang, G. Cui, and H. Wang, “Inverse calculation of burden distribution matrix using b-spline model based pdf control in blast furnace burden charging process,” IEEE Trans. on Industrial Informatics, Vol.19, No.1, 2023. https://doi.org/10.1109/TII.2022.3157641
- [19] N. Nath, “Simulation of gas flow in blast furnace for different burden distribution and cohesive zone shape,” Materials and Manufacturing Processes, Vol.17, No.5, pp. 671-681, 2002. https://doi.org/10.1081/AMP-120016090
- [20] Y. C. Liu, “Analysis of blast furnace slag fall-off,” China Metallurgy, Vol.24, No.12, pp. 32-35, 2007. https://doi.org/10.13228/j.boyuan.issn1006-9356.20140017
- [21] D. Wang, W. Pedrycz, and Z. Li, “Design of granular interval-valued information granules with the use of the principle of justifiable granularity and their applications to system modeling of higher type,” Soft Computing, Vol.20, No.6, pp. 2119-2134, 2016. http://doi.org/10.1007/s00500-015-1904-1
- [22] W. Pedrycz and W. Homenda, “Building the fundamentals of granular computing: A principle of justifiable granularity,” Applied Soft Computing, Vol.13, No.10, pp. 4209-4218, 2013. https://doi.org/10.1016/j.asoc.2013.06.017
- [23] J. A. Hartigan and M. A. Wong, “Algorithm AS 136: A K-means clustering algorithm,” J. of the Royal Statistical Society, Vol.28, No.1, pp. 100-108, 1979. https://doi.org/10.2307/2346830
- [24] S. Peng, C. Zhou, M. Hepburn, M. D. Judd, and W. H. Siew, “Application of K-means method to pattern recognition in on-line cable partial discharge monitoring,” IEEE Trans. on Dielectrics and Electrical Insulation, Vol.20, No.3, pp. 754-761, 2013. https://doi.org/10.1109/TDEI.2013.6518945
- [25] E. Mohamed and T. Celik, “Early detection of failures from vehicle equipment data using K-means clustering design,” Computers and Electrical Engineering, Vol.103, Article No.108351, 2022. https://doi.org/10.1016/j.compeleceng.2022.108351
- [26] Y. Ren, L. F. Chen, Y. Feng, J. Hu, and M. Wu, “Pressure control of pre-chamber based on operating mode recognition in coke dry quenching process,” The 32nd Chinese Process Control Conf., 2021. https://doi.org/10.26914/c.cnkihy.2021.047428
This article is published under a Creative Commons Attribution-NoDerivatives 4.0 Internationa License.