Paper:
Hermetically-Sealed Flexible Mobile Robot “MOLOOP” for Narrow Terrain Exploration
Hitoshi Kimura*, Mokutaro Kataoka**, and Norio Inou**
*Tamagawa University
6-1-1 Tamagawagakuen, Machida city, Tokyo 194-8610, Japan
**Tokyo Institute of Technology
2-12-1 Ookayama, Meguro-ku, Tokyo 152-8550, Japan
Conventional mobile robots typically use a wheel or crawler mechanism for locomotion. However, these robots often get stuck in narrow spaces. To mitigate this issue, we propose an innovative flexible mobile robot named “MOLOOP” in this study. The proposed robot has double-looped and hermetically-sealed structure and all ground-contact-area moves to the same direction. Three synchronized flexible crawlers generate the driving force within the robot body. The crawler, named “HS crawler,” comprises of loop-connected flexible bags. The entire body of the robot is flexible; therefore, the robot can pass through narrow terrains with adaptive shape changes. However, in terms of power and size, performance improvement is necessary for the practical use of the robot. This paper describes the improvement of HS crawler performance, which directly affects the driving force, traveling speed, and size of the robot. For the purpose of high input pressure, this study reinforced the flexible bags of the crawler using fibrous materials. This reinforcement realizes the power-up and downsizing of the flexible bags. The new crawler achieves a performance of 3.43 Nm torque and 39.0 mm/s traveling speed, compared to a torque of 0.23 Nm and traveling speed of 3.0 mm/s of the previous crawler. Additionally, the width of the new MOLOOP changed to 270 mm from 420 mm because of the downsized crawler. Furthermore, a dedicated mechanical valve was developed. This valve achieves a flow rate of 2.39 L/min as compared to 0.92 L/min of a commercially available solenoid valve. Moreover, the traveling speed of MOLOOP increased from 3.0 mm/s to 9.0 mm/s. The prototype robot successfully passed through a narrow terrain with a minimum width of 200 mm (robot width: 270 mm).
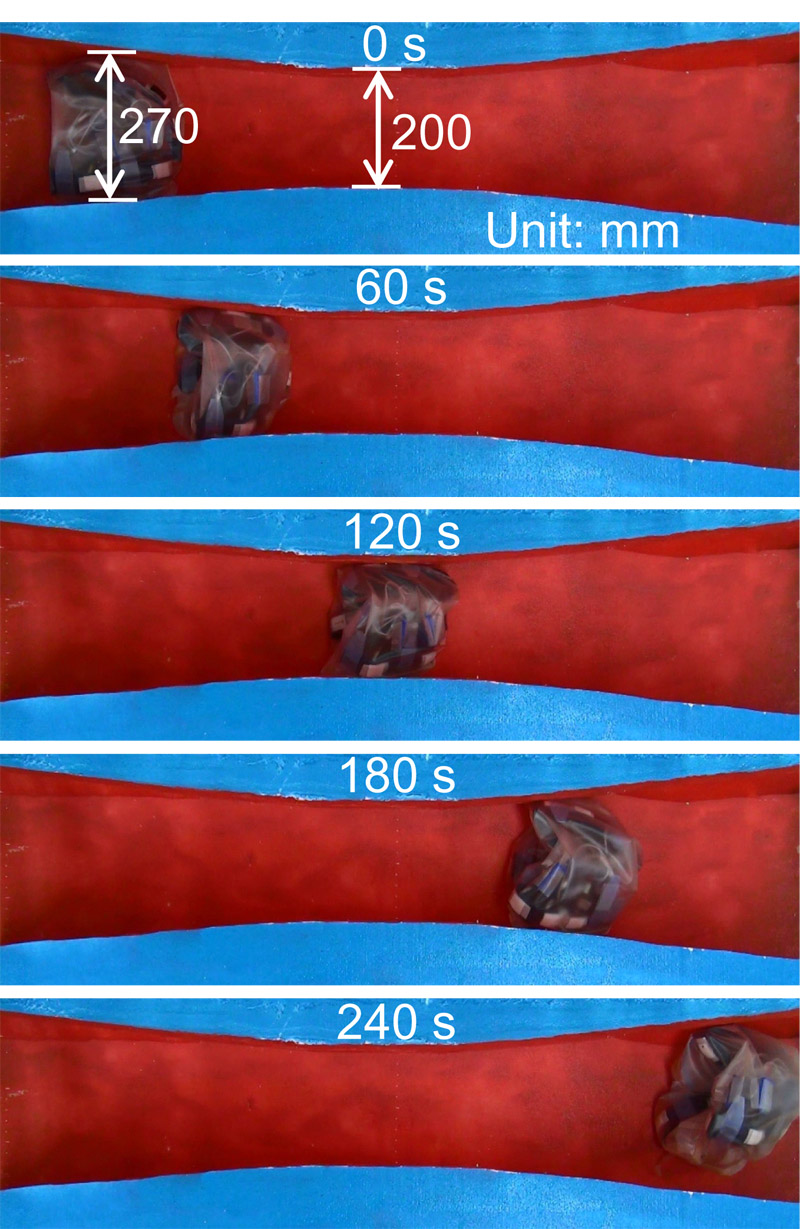
Driving experiment of MOLOOP in a narrow space
- [1] T. Takayama and S. Hirose, “Development of “Souryu I & II” – connected crawler vehicle for inspection of narrow and winding space,” J. Robot. Mechatron., Vol.15, No.1, pp. 61-69, 2003.
- [2] H. Kimura, K. Shimizu, and S. Hirose, “Development of Genbu: Active-wheel passive-joint snake-like mobile robot,” J. Robot. Mechatron., Vol.16, No.3, pp. 293-303, 2004.
- [3] B. Klaassen and K. L. Paap, “GMD-SNAKE2: a snake-like robot driven by wheels and a method for motion control,” Proc. of the 1999 IEEE Int. Conf. on Robotics and Automation, Vol.4, pp. 3014-3019, 1999.
- [4] S. A. Wainwright, W. D. Biggs, J. D. Currey, and J. M. Gosline, “Mechanical Design in Organisms,” Princeton University Press, 1982.
- [5] H. Kimura, F. Kajimura, D. Maruyama, M. Koseki, and N. Inou, “Flexible hermetically-sealed mobile robot for narrow spaces using hydrostatic skeleton driving mechanism,” Proc. of the 2006 IEEE/RSJ Int. Conf. on Intelligent Robots and Systems, pp. 4006-4011, 2006.
- [6] F. Kasagami, H. Wang, M. Araya, I. Sakuma, and T. Dohi, “Development of a robot to assist patient transfer,” Proc. of the 2004 IEEE Int. Conf. on Systems, Man and Cybernetics, Vol.5, pp. 4383-4388, 2004.
- [7] J. Borenstein and A. Borrell, “The OmniTread OT-4 serpentine robot,” Proc. of the Int. Conf. on Robotics and Automation (ICRA 2008), pp. 1766-1767, 2008.
- [8] J.-Y. Nagase, K. Suzumori, and N. Saga, “Cylindrical crawler unit based on worm rack mechanism for rescue robot,” Proc. of the 2012 19th Int. Conf. on Mechatronics and Machine Vision in Practice (M2VIP), pp. 218-221, 2012.
- [9] D. W. Hong, M. Ingram, and D. Lahr, “Whole skin locomotion inspired by amoeboid motility mechanisms,” J. of Mechanisms and Robotics, Vol.1, No.1, 011015, 2009.
- [10] M. Showalter, M. Ingram, and D. W. Hong, “Feasibility experiments for the biologically inspired whole skin locomotion mechanism,” Proc. of the 2006 IEEE Int. Conf. on Robotics and Automation, pp. 15-19, 2006.
- [11] M. Kurata, T. Takayama, and T. Omata, “Helical rotation in-pipe mobile robot,” Proc. of the 2010 3rd IEEE RAS and EMBS Int. Conf. on Biomedical Robotics and Biomechatronics (BioRob), pp. 313-318, 2010.
- [12] T. Takayama, H. Takeshima, T. Hori, and T. Omata, “A twisted bundled tube locomotive device proposed for in-pipe mobile robot,” IEEE/ASME Trans. on Mechatronics, Vol.20, No.6, pp. 2915-2923, 2015.
- [13] E. Steltz, A. Mozeika, N. Rodenberg, E. Brown, and H. M Jaeger, “JSEL: Jamming skin enabled locomotion,” Proc. of the 2009 IEEE/RSJ Int. Conf. on Intelligent Robots and Systems (IROS 2009), pp. 5672-5677, 2009.
- [14] R. F. Shepherd, F. Ilievski, W. Choi, S. A. Morin, A. A. Stokes, A. D. Mazzeo, X. Chen, M. Wang, and G. M. Whitesides, “Multigait soft robot,” Proc. of the National Academy of Sciences of the United States of America, Vol.108, No.51, pp. 20400-20403, 2011.
- [15] H. Kimura, T. Higashi, M. Kataoka, and N. Inou, “Flexible mobile robot for narrow terrain with ciliary actuators,” Proc. of the 2nd IFToMM Asian Conf. on Mechanism and Machine Science (Asian MMS 2012), ID92, 2012.
- [16] H. Kimura, M. Kataoka, T. Higashi, and N. Inou, “Development of flexible ciliary actuators and their application to mobile robots,” J. of of Aero Aqua Bio-Mechanisms, Vol.4, No.1, pp. 71-77, 2015.
- [17] K. Suzumori, “Applying flexible microactuators to pipeline inspection robots,” Robotics, Mechatronics and Manufacturing Systems, pp. 515-520, 1993.
- [18] K. Suzumori, T. Maeda, H. Wantabe, and T. Hisada, “Fiberless flexible microactuator designed by finite-element method,” IEEE/ASME Trans. on Mechatronics, Vol.2, No.4, pp. 281-286, 1997.
- [19] H. Tsukagoshi, S. Kase, T. Kato, T. Suzuki, and A. Kitagawa, “Wearable fluid power composed of flat tubes to activate the body,” Proc. of the 7th JFPS Int. Symp. on Fluid Power, Vol.7, pp. 203-206, 2008.
- [20] D. Maruyama, H. Kimura, M. Koseki, and N. Inou, “A flexible mechanical system using a hydrostatic skeleton (evaluation of driving force and structural strength of the system),” Proc. of the 1st Int. Symp. on Robotics and Mechatronics (ISRM 2009), 25, 2009.
- [21] D. Maruyama, H. Kimura, M. Koseki, and N. Inou, “Driving force and structural strength evaluation of a flexible mechanical system with a hydrostatic skeleton,” J. of Zhejiang University Science A, Vol.11, No.4, pp. 255-262, 2010.
- [22] M. Kataoka, H. Kimura, and N. Inou, “ Hermetically-sealed flexible mobile robot “MOLOOP” for narrow terrain exploration – improvement of flexible bags with fibrous material –,” Proc. of the 39th Annual Conf. of the IEEE Industrial Electronics Society (IECON 2013), pp. 4156-4161, 2013.
- [23] M. Arai, Y. Tanaka, S. Hirose, H. Kuwahara, and S. Tsukui, “Development of “Souryu-IV” and “Souryu-V:” serially connected crawler vehicles for in-rubble searching operations,” J. of Field Robotics, Vol.25, Nos.1-2, pp. 31-65, 2008.
- [24] H. Kimura, M. Kataoka, T. Higashi, and N. Inou, “Development of flexible ciliary actuators and their application to mobile robots,” J. of Aero Aqua Bio-Mechanisms, Vol.4, No.1, pp. 71-77, 2015.
- [25] H. Kimura, M. Kataoka, S. Suzuki, D. Akimoto, and N. Inou, “A flexible robotic arm with hydraulic skeleton,” J. of Advanced Mechanical Design, Systems, and Manufacturing, Vol.6, No.7, pp. 1107-1120, 2012.
This article is published under a Creative Commons Attribution-NoDerivatives 4.0 Internationa License.