Paper:
A Soft Needle Gripper Capable of Grasping and Piercing for Handling Food Materials
Zhongkui Wang, Yui Makiyama, and Shinichi Hirai
Ritsumeikan University
1-1-1 Noji-higashi, Kusatsu, Shiga 525-8577, Japan
Automation in the food industry is not as developed as in the automotive industry because of difficulties in handling food products with large variations in shape, size, and mechanical properties. In this paper, a pneumatic-driven soft needle gripper is proposed for handling food materials. It was constructed using a soft membrane and multiple rigid needle-like fingers. It can work under two operational modes: grasping and piercing. The grasping mode can be used to grasp shredded and chopped food materials. The piercing mode is for handling food products when only the top surface of the food product is available for handling. The needle gripper is fabricated using a multi-material 3D printer. Experimental tests on various food materials are conducted to validate grasping and piercing operations. The results of grasping tests suggest that the needle gripper can successfully grasp shredded and chopped food materials. A quantitative analysis shows that the relative standard deviation of the grasped food weight was within 20%. Although the results of piercing tests validate that the needle gripper can successfully handle various food materials, releasing the food materials involves certain difficulties.
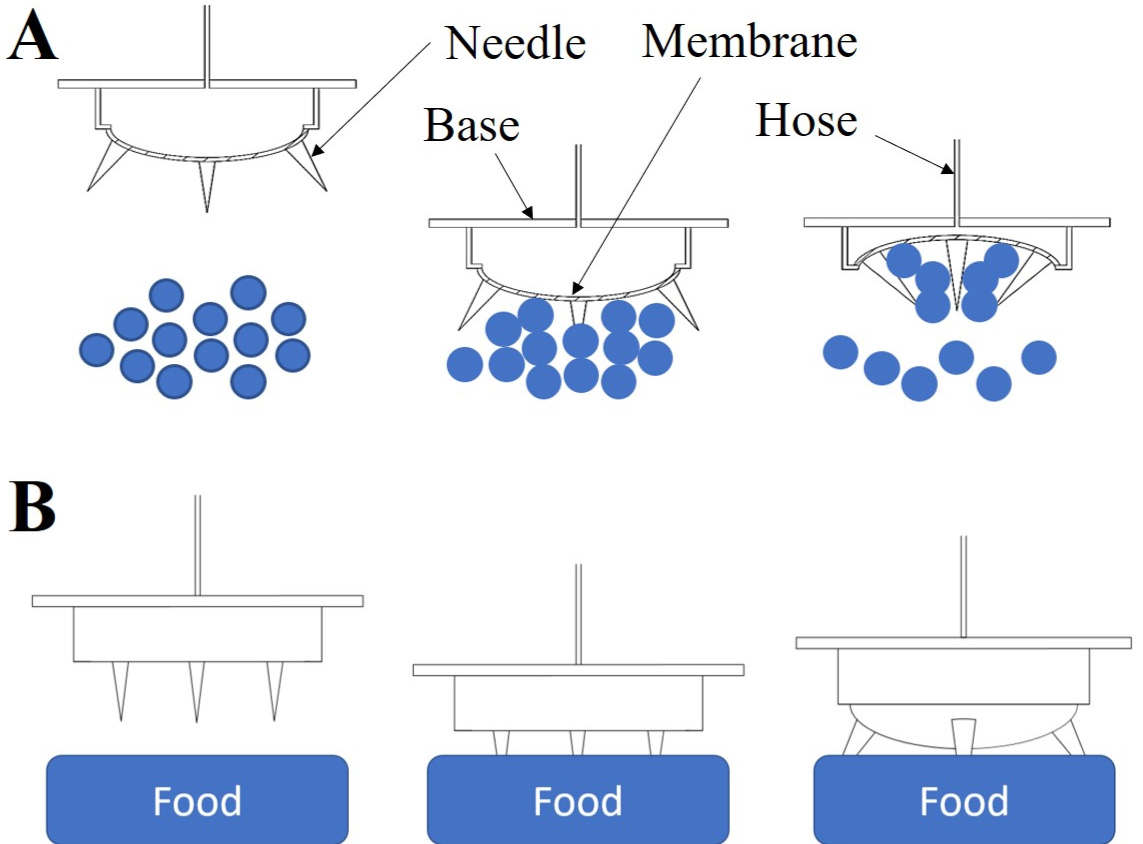
Needle gripper for grasping (A) and piercing (B) food materials
- [1] P. Y. Chua, T. Ilschner, and D. G. Caldwell, “Robotic manipulation of food products – a review,” Industrial Robot, Vol.30, No.4, pp. 345-354, 2003.
- [2] D. G. Caldwell, S. Caldwell, R. J. Moreno Masey, and J. O. Gray, “Automation in Food Processing,” S. Nof (Ed.), “Springer Handbook of Automation,” Springer, pp. 1041-1059, 2009.
- [3] F. Chen, K. Sekiyama, B. Sun, P. Di, J. Huang, H. Sasaki, and T. Fukuda, “Design and application of an intelligent robotic gripper for accurate and tolerant electronic connector mating,” J. Robot. Mechatron., Vol.24, No.3, pp. 441-451, 2012.
- [4] G. A. Nayik, K. Muzaffar, and A. Gull, “Robotics and food technology: a mini review,” J. of Nutrition and Food Sciences, Vol.5, No.4, 1000384, 2015.
- [5] M. Hamazawa, “Robot applications in the Japanese food industry,” Industrial Robot, Vol.26, No.4, pp. 274-277, 1999.
- [6] A. Pettersson, T. Ohlsson, S. Davis, J. O. Gray, and T. J. Dodd, “A hygienically designed force gripper for flexible handling of variable and easily damaged natural food products,” Innovative Food Science and Emerging Technologies, Vol.12, No.3, pp. 344-351, 2011.
- [7] S. Davis, J. O. Gray, and D. G. Caldwell, “An end effector based on the Bernoulli principle for handling sliced fruit and vegetables,” Robotics and Computer-Integrated Manufacturing, Vol.24, Issue 2, pp. 249-257, 2008.
- [8] R. Sam and S. Nefti, “Design and feasibility tests of flexible gripper for handling variable shape of food products,” Proc. of 9th WSEAS Int. Conf. on Signal Processing, Robotics, and Automation, pp. 329-335, 2010.
- [9] G. Endo and N. Otomo, “Development of a food handling gripper considering an appetizing presentation,” Proc. of 2016 IEEE Int. Conf. on Robotics and Automation, pp. 4901-4906, 2016.
- [10] S. Bachche and K. Oka, “Design, modeling and performance testing of end-effector for sweet pepper harvesting robot hand,” J. Robot. Mechatron., Vol.25, No.4, pp. 705-717, 2013.
- [11] T. Tamamoto, K. Takeuchi, and K. Koganezawa, “Development of gripper to achieve envelope grasping with underactuated mechanism using differential gear,” J. Robot. Mechatron., Vol.30, No.6, pp. 855-862, 2018.
- [12] A. Pettersson, S. Davis, J. O. Gray, T. J. Dodd, and T. Ohlsson, “Design of a magnetorheological robot gripper for handling of delicate food products with varying shapes,” J. of Food Engineering, Vol.98, Issue 3, pp. 332-338, 2010.
- [13] S. Li, J. J. Stampfli, H. J. Xu, E. Malkin, E. V. Diaz, D. Rus, and R. J. Wood, “A vacuum-driven origami “magic-ball” soft gripper,” Proc. of 2019 Int. Conf. on Robotics and Automation, pp. 7401-7408, 2019.
- [14] S. Ma, L. Du, E. Tsuchiya, and M. Fuchimi, “Paper-made grippers for soft food grasping,” Proc. of 17th Int. Conf. on Ubiquitous Robots, pp. 362-367, 2020.
- [15] T. Nishimura, Y. Suzuki, T. Tsuji, and T. Watanabe, “Fluid pressure monitoring-based strategy for delicate grasping of fragile objects by a robotic hand with fluid fingertips,” Sensor, Vol.19, No.4, 782, 2019.
- [16] A. Gafer, D. Heymans, D. Prattichizzo, and G. Salvietti, “The quad-spatula gripper: a novel soft-rigid gripper for food handling,” Proc. of 3rd IEEE Int. Conf. on Soft Robotics, pp. 39-45, 2020.
- [17] J. Zhou, S. Chen, and Z. Wang, “A soft-robotic gripper with enhanced object adaptation and grasping reliability,” IEEE Robotics and Automation Letters, Vol.2, No.4, pp. 2287-2293, 2017.
- [18] Y. Yamanaka, S. Katagiri, H. Nabae, K. Suzumori, and G. Endo, “Development of a food handling soft robot hand considering a high-speed pick-and-place task,” Proc. of IEEE/SICE Int. Symp. on System Integration, pp. 87-92, 2020.
- [19] Z. Wang, D. S. Chathuranga, and S. Hirai, “3D printed soft gripper for automatic lunch box packing,” Proc. of IEEE Int. Conf. on Robotics and Biomimetics, pp. 503-508, 2016.
- [20] Z. Wang, Y. Torigoe, and S. Hirai, “A prestressed soft gripper: design, modeling, fabrication, and tests for food handling,” IEEE Robotics and Automation Letters, Vol.2, No.4, pp. 1909-1916, 2017.
- [21] Z. Wang, K. Or, and S. Hirai, “A dual-mode soft gripper for food packaging,” Robotics and Autonomous Systems, Vol.125, 103427, 2020.
- [22] Y. Kuriyama, Y. Okino, Z. Wang, and S. Hirai, “A wrapping gripper for packaging chopped and granular food materials,” Proc. of 2nd IEEE Int. Conf. on Soft Robotics, pp. 114-119, 2019.
- [23] Z. Wang, R. Kanegae, and S. Hirai, “Circular shell gripper for handling food products,” Soft Robotics, doi: 10.1089/soro.2019.0140, 2020.
- [24] R. Kanegae, Z. Wang, and S. Hirai, “Easily Fabricatable Shell Gripper for Packaging Multiple Cucumbers Simultaneously,” Proc. of 2020 IEEE Int. Conf. on Real-time Computing and Robotics (RCAR 2020), pp. 188-192, 2020.
- [25] Z. Wang, H. Furuta, S. Hirai, and S. Kawamura, “A scooping-binding robotic gripper for handling various food products,” Frontiers in Robotics and AI, Vol.8, 43, doi: 10.3389/frobt.2021.640805, 2021.
- [26] Y. Makiyama, Z. Wang, and S. Hirai, “A pneumatic needle gripper for handling shredded food products,” Proc. of 2020 IEEE Int. Conf. on Real-time Computing and Robotics (RCAR 2020), pp. 183-187, 2020.
- [27] Design Principles, “Hygienic design principles,” European Hygienic Engineering and Design Group (EHEDG), 2018.
- [28] R. Nishino, S. Aoyagi, M. Suzuki, A. Ueda, Y. Okumura, T. Takahashi, R. Hosomi, K. Fukunaga, D. Uta, T. Takazawa, and T. Fujii, “Development of artificial skin using keratin film for evaluation of puncture performance of microneedle,” J. Robot. Mechatron., Vol.32, No.2, pp. 351-361, 2020.
This article is published under a Creative Commons Attribution-NoDerivatives 4.0 Internationa License.