Paper:
Tracking and Visualizing Signs of Degradation for Early Failure Prediction of Rolling Bearings
Sana Talmoudi*, Tetsuya Kanada**, and Yasuhisa Hirata*
*Department of Robotics, Graduate School of Engineering, Tohoku University
6-6-1 Aramaki Aza Aoba, Aoba-ku, Sendai, Miyagi 980-8579, Japan
**D’isum Inc.
3-10-18 Takanawa, Minato-ku, Tokyo 108-0074, Japan
Predictive maintenance, which means detection of failure ahead of time, is one of the pillars of Industry 4.0. An effective method for this technique is to track early signs of degradation before failure occurs. This paper presents an innovative failure predictive scheme for machines. The proposed scheme combines the use of the full spectrum of vibration data from the machines and a data visualization technology. This scheme requires no training data and can be started quickly after installation. First, we proposed to use the full spectrum (as high-dimensional data vectors) with no cropping and no complex feature extraction and to visualize the data behavior by mapping the high-dimensional vectors into a two-dimensional (2D) map. This ensures simplicity of the process and less possibility of overlooking important information as well as provide a human-friendly and human-understandable output. Second, we developed a real-time data tracker that can predict failure at an appropriate time with sufficient allowance for maintenance by plotting real-time frequency spectrum data of the target machine on a 2D map created from normal data. Finally, we verified our proposal using vibration data of bearings from real-world test-to-failure measurements obtained from the IMS dataset.
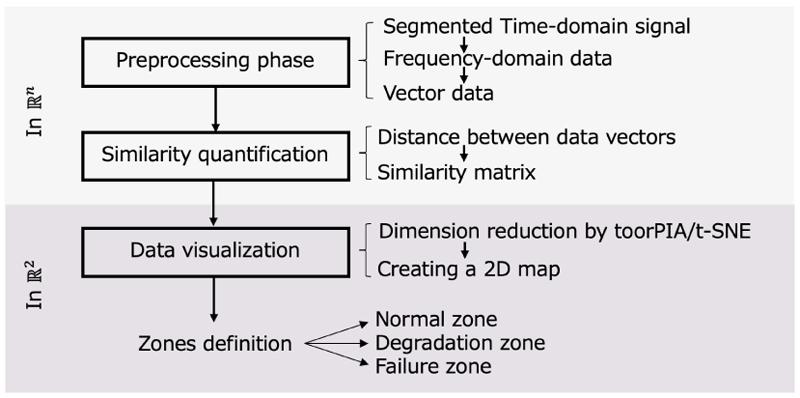
Process flow of the data analysis scheme
- [1] A. Bellini, F. Filippetti, C. Tassoni, and G.-A. Capolino, “Advances in diagnostic techniques for induction machines,” IEEE Trans. on Industrial Electronics, Vol.55, No.12, pp. 4109-4126, 2008.
- [2] A. H. Bonnett and C. Yung, “Increased efficiency versus increased reliability,” IEEE Industry Applications Magazine, Vol.14, No.1, pp. 29-36, 2008.
- [3] K. Ikeda and A. Kamimura, “Hammering acoustic analysis using machine learning techniques for piping inspection,” J. Robot. Mechatron., Vol.32, No.4, pp. 789-797, 2020.
- [4] J. Windau and L. Itti, “Inertial machine monitoring system for automated failure detection,” Proc. of the 2018 IEEE Int. Conf. on Robotics and Automation (ICRA), pp. 93-98, 2018.
- [5] Z. Zhang, Y. Wang, and K. Wang, “Fault diagnosis and prognosis using wavelet packet decomposition, Fourier transform and artificial neural network,” J. of Intelligent Manufacturing, Vol.24, No.6, pp. 1213-1227, 2013.
- [6] S. Talmoudi, T. Kanada, and Y. Hirata, “An iot-based failure prediction solution using machine sound data,” Proc. of the 2019 IEEE/SICE Int. Symp. on System Integration (SII), pp. 227-232, 2019.
- [7] Y. Koizumi, S. Saito, H. Uematsu, N. Harada, and K. Imoto, “Toyadmos: A dataset of miniature-machine operating sounds for anomalous sound detection,” Proc. of the 2019 IEEE Workshop on Applications of Signal Processing to Audio and Acoustics (WASPAA), pp. 313-317, 2019.
- [8] H. Qiu, J. Lee, J. Lin, and G. Yu, “Wavelet filter-based weak signature detection method and its application on rolling element bearing prognostics,” J. of Sound and Vibration, Vol.289, No.4, pp. 1066-1090, 2006.
- [9] P. Nectoux, R. Gouriveau, K. Medjaher, E. Ramasso, B. Chebel-Morello, N. Zerhouni, and C. Varnier, “Pronostia: An experimental platform for bearings accelerated degradation tests,” Proc. of the IEEE Int. Conf. on Prognostics and Health Management, pp. 1-8, 2012.
- [10] D. Fernandez-Francos, D. Martinez, O. Fontenla-Romero, and A. Alonso-Betanzos, “Automatic bearing fault diagnosis based on one-class v-svm,” Computers and Industrial Engineering, Vol.64, pp. 357-365, 2013.
- [11] H. Huang, H. Ouyang, H. Gao, L. Guo, D. Li, and J. Wen, “A feature extraction method for vibration signal of bearing incipient degradation,” Measurement Science Review, Vol.16, Issue 3, pp. 149-159, 2016.
- [12] M. Diaz, P. Henriquez, M. A. Ferrer, G. Pirlo, J. B. Alonso, C. Carmona-Duarte, and D. Impedovo, “Stability-based system for bearing fault early detection,” Expert Systems with Applications, Vol.79, pp. 65-75, 2017.
- [13] R. Zhang, Z. Peng, L. Wu, B. Yao, and Y. Guan, “Fault diagnosis from raw sensor data using deep neural networks considering temporal coherence,” Sensors, Vol.17, 549, 2017.
- [14] R. B. Amil, S. T. Gul, and A. Q. Khan, “A comparative analysis of classical and one class svm classifiers for machine fault detection using vibration signals,” Proc. of the 2016 Int. Conf. on Emerging Technologies (ICET), pp. 1-6, 2016.
- [15] Y. Zhang, X. Li, L. Gao, and P. Li, “A new subset based deep feature learning method for intelligent fault diagnosis of bearing,” Expert Systems with Applications, Vol.110, pp. 125-142, 2018.
- [16] T. Berredjem and M. Benidir, “Bearing faults diagnosis using fuzzy expert system relying on an improved range overlaps and similarity method,” Expert Systems with Applications, Vol.108, pp. 134-142, 2018.
- [17] S. Gul, M. Imran, and A. Khan, “An online incremental support vector machine for fault diagnosis using vibration signature analysis,” Proc. of the 2018 IEEE Int. Conf. on Industrial Technology (ICIT), pp. 1467-1472, 2018.
- [18] P. S. Ambika, P. K. Rajendrakumar, and R. Ramchand, “Vibration signal based condition monitoring of mechanical equipment with scattering transform,” J. of Mechanical Science and Technology, Vol.33, pp. 3095-3103, 2019.
- [19] H. Huang, Q. Fan, J. Wei, and D. Huang, “An intelligent fault identification method of rolling bearings based on svm optimized by improved gwo,” Systems Science and Control Engineering, Vol.7, pp. 289-303, 2019.
- [20] H. Qiu, J. Lee, J. Lin, and G. Yu, “Robust performance degradation assessment methods for enhanced rolling element bearing prognostics,” Advanced Engineering Informatics, Vol.17, pp. 127-140, 2003.
- [21] H. Qiu and J. Lee, “Feature fusion and degradation using self-organizing map,” Proc. of the 2004 Int. Conf. on Machine Learning and Applications, pp. 107-114, 2004.
- [22] H. Liao, W. Zhao, and H. Guo, “Predicting remaining useful life of an individual unit using proportional hazards model and logistic regression model,” Annual Reliability and Maintainability Symp., pp. 127-132, 2006.
- [23] W. Caesarendra, A. Widodo, and B.-S. Yang, “Application of relevance vector machine and logistic regression for machine degradation assessment,” Mechanical Systems and Signal Processing, Vol.24, pp. 1161-1171, 2010.
- [24] A. Mahamad, S. Saon, and T. Hiyama, “Predicting remaining useful life of rotating machinery based artificial neural network,” Computers and Mathematics with Applications, Vol.60, pp. 1078-1087, 2010.
- [25] J. Yu, “Bearing performance degradation assessment using locality preserving projections and gaussian mixture models,” Mechanical Systems and Signal Processing, Vol.25, No.7, pp. 2573-2588, 2011.
- [26] A. Widodo and B.-S. Yang, “Application of relevance vector machine and survival probability to machine degradation assessment,” Expert Syst. Appl., Vol.38, No.3, pp. 2592-2599, 2011.
- [27] J. Yu, “A hybrid feature selection scheme and self-organizing map model for machine health assessment,” Applied Soft Computing, Vol.11, No.5, pp. 4041-4054, 2011.
- [28] J. Yu, “Local and nonlocal preserving projection for bearing defect classification and performance assessment,” IEEE Trans. on Industrial Electronics, Vol.59, No.5, pp. 2363-2376, 2012.
- [29] J. Yu, “Health condition monitoring of machines based on hidden Markov model and contribution analysis,” IEEE Trans. on Instrumentation and Measurement, Vol.61, pp. 2200-2211, 2012.
- [30] S. Dong and T. Luo, “Bearing degradation process prediction based on the pca and optimized ls-svm model,” Measurement, Vol.46, pp. 3143-3152, 2013.
- [31] J. Ben Ali, N. Fnaiech, L. Saidi, B. Chebel-Morello, and F. Fnaiech, “Application of empirical mode decomposition and artificial neural network for automatic bearing fault diagnosis based on vibration signals,” Applied Acoustics, Vol.89, pp. 16-27, 2015.
- [32] A. Soualhi, H. Razik, C. Guy, and D. D. Doan, “Prognosis of bearing failures using hidden Markov models and the adaptive neuro-fuzzy inference system,” IEEE Trans. on Industrial Electronics, Vol.61, 2013.
- [33] J. B. Ali, B. Chebel-Morello, L. Saidi, S. Malinowski, and F. Fnaiech, “Accurate bearing remaining useful life prediction based on weibull distribution and artificial neural network,” Mechanical Systems and Signal Processing, Vols.56-57, pp. 150-172, 2015.
- [34] Y. Qian, R. Yan, and R. Gao, “A multi-time scale approach to remaining useful life prediction in rolling bearing,” Mechanical Systems and Signal Processing, Vol.83, pp. 549-567, 2016.
- [35] R. Hasani, G. Wang, and R. Grosu, “An automated auto-encoder correlation-based health-monitoring and prognostic method for machine bearings,” arXiv, 2017.
- [36] N. Zhang, L. Wu, Z. Wang, and Y. Guan, “Bearing remaining useful life prediction based on naive bayes and weibull distributions,” Entropy, Vol.20, 944, 2018.
- [37] L. van der Maaten and G. Hinton, “Visualizing data using t-sne,” J. of Machine Learning Research, Vol.9, No.86, pp. 2579-2605, 2008.
- [38] G. E. Hinton and S. Roweis, “Stochastic neighbor embedding,” S. Becker, S. Thrun, and K. Obermayer (Eds.), “Advances in Neural Information Processing Systems,” Vol.15, pp. 857-864. MIT Press, 2003.
- [39] F. Pedregosa, G. Varoquaux, A. Gramfort, V. Michel, B. Thirion, O. Grisel, M. Blondel, P. Prettenhofer, R. Weiss, V. Dubourg, J. Vanderplas, A. Passos, D. Cournapeau, M. Brucher, M. Perrot, and É. Duchesnay, “Scikit-learn: Machine learning in python,” J. of Machine Learning Research, Vol.12, No.85, pp. 2825-2830, 2011.
This article is published under a Creative Commons Attribution-NoDerivatives 4.0 Internationa License.