Development Report:
Free-Flow Tunnel Inspection Support Devices Aiming at Labor Saving of Visual Checking
Kazunori Hosotani and Hirofumi Yamamoto
National Institute of Technology, Tsuyama College
624-1 Numa, Tsuyama, Okayama 708-8509, Japan
Small and medium-sized hydroelectric power plants are scattered in mountainous areas of Japan. Many tunnels that have been constructed for the purpose of introducing water have been in operation for decades, and inspections to aging deterioration are indispensable, however checks and maintenance work within the tunnels where the ceiling is low and water is flowing is very burdensome. This research aims at labor saving of visual check work of an inspector who moves through a narrow tunnel and searches for a deformed portion, and a simple imaging support device with a camera on a walking aid and autonomous operation at a constant speed in the tunnel. In this article, a prototype of a walking assist type inspection device and a self-propelled monitoring robot that creates a developed image of the wall surface are described. The prototype device is tested in a free-flow tunnel at the Tsukuyone Hydroelectric Power Station in Tottori Prefecture where water intake into the tunnel is stopped due to renewal work from 2018 to 2019, and its practicality is evaluated.
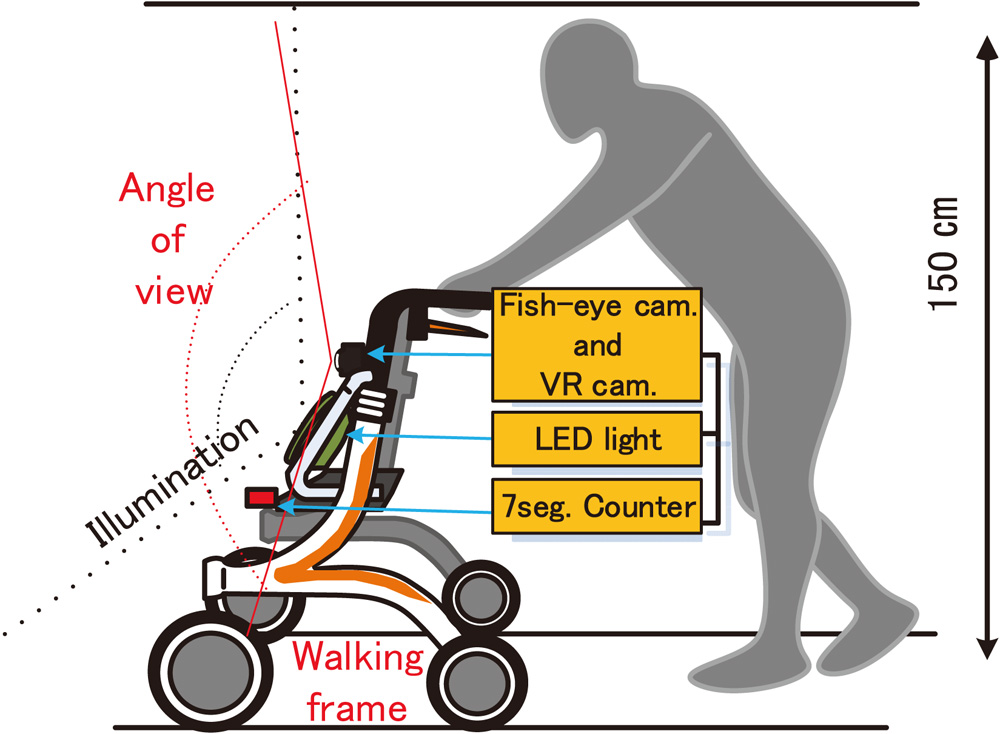
Walking-assistance-type inspection device
- [1] R. Montero, J. G. Victores, S. Martinez, A. Jardon, and C. Balaguer, “Past, present and future of robotic tunnel inspection,” Automation in Construction, Vol.59, pp. 99-112, 2015.
- [2] S. Nakamura, A. Yamashita, F. Inoue, D. Inoue, Y. Takahashi, N. Kamimura, and T. Ueno, “Inspection test of a tunnel with an inspection vehicle for tunnel lining concrete,” J. Robot. Mechatron., Vol.31, No.6, pp. 762-771, 2019.
- [3] E. Menendez, J. G. Victores, R. Montero, S. Martinez, and C. Balaguer, “Tunnel structural inspection and assessment using an autonomous robotic system,” Automation in Construction, Vol.87, pp. 117-126, 2018.
- [4] F. Ikeda, S. Toyama, T. Kumota, and T. Yanagisawa, “360 Development of sewer pipe measurement vehicle robots equipped with integrated sensing system,” Proc. Dynamics & Design Conf., Vol.2012, 360, 2017.
- [5] G. Seet, S. H. Yeo, W. C. Law, Burhan, C. Y. Wong, S. Sapari, and K. K. Liau, “Design of tunnel inspection robot for large diameter sewers,” Procedia Computer Science, Vol.133, pp. 984-990, 2018.
- [6] T. Fujiwara, “Total Cost Reduction Using New Diagnostic Technique for Water Tunnel,” Water, Land and Environmental Engineering, Vol.82, No.4, pp. 305-308, 2014 (in Japanese).
- [7] M. Mori, T. Mori, M. Tokashiki, T. Nakaya, T. Fujiwara, and Y. Saito, “Development of diagnosis system of irrigation tunnel under water servicing,” Trans. Japanese Society of Irrigation, Drainage and Rural Engineering, Vol.80, No.2, pp. 87-95, 2013 (in Japanese).
- [8] T. Imaida, Y. Yoshinami, N. Kikuchi, and S. Endo, “Development of underwater robot camera for inspection of water-channel tunnels,” J. Japan Society of Civil Engineers (Safety Problem), Vol.4, 2009 (in Japanese).
- [9] C. H. Tan, M. Ng, D. S. B. Shaiful, S. K. H. Win, W. J. Ang, S. K. Yeung, H. B. Lim, M. N. Do, and S. Foong, “A smart unmanned aerial vehicle (UAV) based imaging system for inspection of deep hazardous tunnels,” Water Practice and Technology, Vol.13, No.4, pp. 991-1000, 2018.
- [10] M. Ogawa, W. Tsuru, and K. Yokota, “Behavior of a drone in a cylindrical duct,” Proc. Conf. of Kanto Branch (JSME), Vol.2019, No.25, 18B12, 2019.
- [11] Ministry of Agriculture, Forestry and Fisheries, “Land improvement project planning design standard technical document (design, waterway tunnel),” p. 620, 2014 (in Japanese).
- [12] Japan Federation of Construction and Constructors, “Renewal technology for hydroelectric civil engineering facilities,” p. 430, 2015 (in Japanese).
- [13] K. Hosotani and N. Hiraishi, “Pilot study of an internal inspection support system for culverts using a VR camera mounted walking frame,” Proc. JSME Annual Conf. on Robotics and Mechatronics (Robomec), Vol.2019, 1P1-D02, 2019 (in Japanese).
- [14] M. Ukai, “Image processing for detection of tunnel wall deformation with line scan camera,” Proc. Japan Joint Automatic Control Conf., Vol.48, I2-44, 2006.
- [15] K. Kawamura, M. Koga, J. Matsumoto, M. Shiozaki, and S. Sawamura, “A Study on panoramic images generation of tunnel wall,” J. Japan Society of Civil Engineers, F3 (Civil Engineering Informatics), Vol.72, No.2, pp. I_73-I_82, 2016 (in Japanese).
- [16] T. Murakami, N. Saito, Y. Komachi, K. Okamura, T. Michikawa, M. Sakashita, S. Kogure, K. Kase, S. Wada, and K. Midorikawa, “High Spatial Resolution Survey Using Frequency-Shifted Feedback Laser for Transport Infrastructure Maintenance,” J. Disaster Res., Vol.12, No.3, pp. 546-556, 2017.
- [17] F. Inoue, S. Kwon, S. Nakamura, and Y. Yanagihara, “Shape Adaptation of the Inspection Guide Frame in Tunnels to Avoid Obstacles Detected by a Laser Range Finder,” J. Robot. Mechatron., Vol.31, No.6, pp. 752-761, 2019.
- [18] “Research and Development Report on Applications of Artificial Intelligence to Infrastructure Maintenance,” SIP Infrastructure Program Coordinate Committee Organization for Promotion of Civil Engineering Technology, p. 175, 2019 (in Japanese).
This article is published under a Creative Commons Attribution-NoDerivatives 4.0 Internationa License.