Paper:
Fabrication, Experiment, and Simulation of a Flexible Microvalve-Integrated Microarm for Microgrippers Using Electrorheological Fluid
Joon-Wan Kim*, Kazuhiro Yoshida*, Toru Ide**, and Shinichi Yokota***
*Laboratory for Future Interdisciplinary Research of Science and Technology (FIRST), Institute of Innovative Research (IIR), Tokyo Institute of Technology
4259 Nagatsuta, Midori-ku, Yokohama, Kanagawa 226-8503, Japan
**Department of Mechano-Micro Engineering, Interdisciplinary Graduate School of Science and Engineering, Tokyo Institute of Technology
4259 Nagatsuta, Midori-ku, Yokohama, Kanagawa 226-8503, Japan
***Precision and Intelligence Laboratory, Tokyo Institute of Technology
4259 Nagatsuta, Midori-ku, Yokohama, Kanagawa 226-8503, Japan
Because of the power density advantages of fluid power systems, many researchers have developed microactuators using homogeneous electrorheological (ER) fluids (ERFs) for applications to various micromachines. An ER valve, as a critical component of the ER actuator, can control ERF flow by the apparent viscosity increase resulting from the applied electric field without any mechanical moving parts. Hence, it is adequate for the miniaturization of a fluidic microactuator. However, it is not easy to integrate rigid ER valves into soft microrobots. To overcome these limitations, we developed a novel elastic ER microarm using flexible ER valves (FERVs) in this study. Each microarm consists of an FERV, a movable chamber, and a displacement constraint element, so that it bends with the inner pressure controlled by the FERV. We proposed and developed a micro-electromechanical system fabrication process for the FERV, movable chamber, and displacement constraint element. By utilizing the proposed method, we successfully fabricate a FERV-integrated microarm. The characteristics of the FERV were experimentally clarified. In addition, the bending motion of the FERV-integrated microarm was demonstrated by experiments and verified by finite-element method simulation. This ER microarm was shown to be feasible for an ER microgripper composed of multiple microarms.
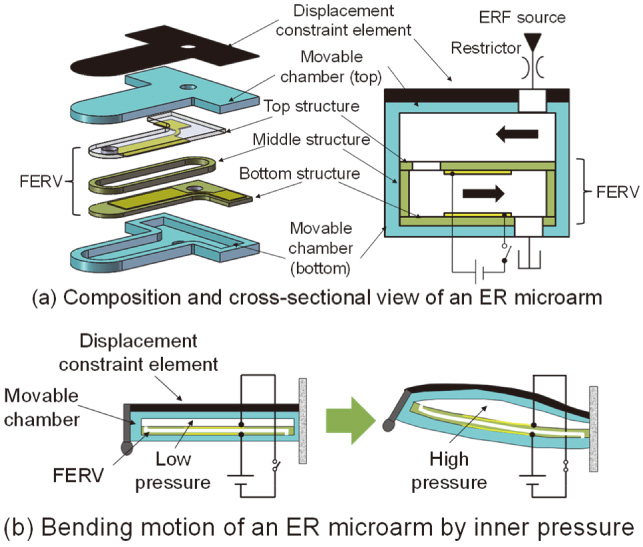
Proposed ER Microarm for the ER microgripper
- [1] M. A. Unger, H.-P. Chou, T. Thorsen, A. Scherer, and S. R. Quake, “Monolithic microfabricated valves and pumps by multilayer soft lithography,” Science, Vol.288, Issue 5463, pp. 113-116, 2000.
- [2] M. De Volder, J. Peris, D. Reynaerts, J. Coosemans, R. Puers, O. Smal, and B. Raucent, “Production and characterization of a hydraulic microactuator,” J. of Micromechanics and Microengineering, Vol.15, No.7, pp. S15-S21, 2005.
- [3] Y. Suzuki, Y. Okada, J. Ogawa, S. Sugiyama, and T. Toriyama, “Experimental study on mechanical power generation from MEMS internal combustion engine,” Sensors and Actuators A: Physical, Vol.141, Issue 2, pp. 654-661, 2008.
- [4] M. De Volder, F. Ceyssens, D. Reynaerts, and R. Puers, “Microsized piston-cylinder pneumatic and hydraulic actuators fabricated by lithography,” IEEE J. of Microelectromechical Systems, Vol.18, Issue 5, pp. 1100-1104, 2009.
- [5] K. Yoshida, K. Takahashi, and S. Yokota, “An in-pipe mobile micromachine using fluid power (A mechanism adaptable to pipe diameters),” JSME Int. J. Series B, Vol.43, Issue 1, pp. 29-35, 2000.
- [6] B. Gorissen, D. Reynaerts, S. Konishi, K. Yoshida, J.-W. Kim, and M. De Volder, “Elastic inflatable actuators for soft robotic applications,” Advanced Materials, Vol.29, No.43, 1604977, 2017.
- [7] K. Uchino, “Micro Walking Machines Using Piezoelectric Actuators,” J. Robot. Mechatron., Vol.1, No.2, pp. 124-127, 1989.
- [8] Y. Irie, H. Aoyama, J. Kubo, T. Fujioka, and T. Usuda, “Piezo-Impact-Driven X-Y Stage and Precise Sample Holder for Accurate Microlens Alignment,” J. Robot. Mechatron., Vol.21, No.5, pp. 635-641, 2009.
- [9] T. Niino, S. Egawa, H. Kimura, and T. Higuchi, “Electrostatic artificial muscle: compact, high-power linear actuators with multiple-layer structures,” Proc. IEEE Micro Electro Mechanical Systems An Investigation of Micro Structures, Sensors, Actuators, Machines and Robotic Systems, Oiso, Japan, pp. 130-135, 1994.
- [10] M. Miyake, K. Suzumori, and K. Uzuka, “Design and Evaluation of Electromagnetic Wobble Motor,” J. Robot. Mechatron., Vol.24, No.3, pp. 480-486, 2012.
- [11] M. Nishida, H. O. Wang, and K. Tanaka, “Development and Control of a Small Biped Walking Robot Using Shape Memory Alloys,” J. Robot. Mechatron., Vol.20, No.5, pp. 793-800, 2008.
- [12] S. Yokota, “A review on micropumps from the viewpoint of volumetric power density,” Mechanical Engineering Reviews, Vol.1, No.2, DSM0014, 2014.
- [13] J.-W. Kim, T. V. X. Nguyen, K. Edamura, and S. Yokota, “Triangular prism and slit electrode pair for ECF jetting fabricated by thick micromold and electroforming as micro hydraulic pressure source for soft microrobots,” Int. J. Automation Technol., Vol.10, No.4, pp. 470-478, 2016.
- [14] J.-W. Kim, Y. Yamada, and S. Yokota, “Micro ECF (electro-conjugate fluid) hydraulic power sources based on the modular design of TPSEs (triangular prism and slit electrode pairs),” The Int. J. of Advanced Manufacturing Technology, Vol.106, Issue 1, pp. 627-639, 2020.
- [15] O. C. Jeong, and S. Konishi, “Fabrication of a peristaltic micro pump with novel cascaded actuators,” J. of Micromechanics and Microengineering, Vol.18, No.2, 025022, 2008.
- [16] C. Moraes, Y. Sun, and C. A. Simmons, “Solving the shrinkage-induced PDMS alignment registration issue in multilayer soft lithography,” J. of Micromechanics and Microengineering, Vol.19, No.6, 065015, 2009.
- [17] M. De Volder, K. Yoshida, S. Yokota, and D. Reynaerts, “The use of liquid crystals as electrorheological fluids in microsystems: model and measurements,” J. of Micromechanics and Microengineering, Vol.16, No.3, pp. 612-619, 2006.
- [18] S. B. Choi, C. C. Cheong, J. M. Jung, and Y. T. Choi, “Position control of an er valve-cylinder system via neural network controller,” Mechatronics, Vol.7, Issue 1, pp. 37-52, 1997.
- [19] M. Kohl, “Fluidic actuation by electrorheological microdevices,” Mechatronics, Vol.10, Issues 4-5, pp. 583-594, 2000.
- [20] M. Nakano, T. Katou, A. Satou, K. Miyata, and K. Matsushita, “Three-ports micro ER valve for ER suspension fabricated by photolithography,” J. of Intelligent Material Systems and Structures, Vol.13, Issues 7-8, pp. 503-508, 2002.
- [21] W. Wen, X. Huang, S. Yang, K. Lu, and P. Sheng, “The giant electrorheological effect in suspensions of nanoparticles,” Nature Materials, Vol.2, Issue 11, pp. 727-730, 2003.
- [22] K. Yoshida, M. Kikuchi, J.-H. Park, and S. Yokota, “Fabrication of micro electro-rheological valves (ER valves) by micromachining and experiments,” Sensors and Actuators A: Physical, Vol.95, Issues 2-3, pp. 227-233, 2002.
- [23] J.-W. Kim, K. Yoshida, K. Kouda, and S. Yokota, “A flexible electro-rheological microvalve (FERV) based on SU-8 cantilever structures and its application to microactuators,” Sensors and Actuators A: Physical, Vol.156, Issue 2, pp. 366-372, 2009.
- [24] K. Yoshida, N. Tsukamoto, J.-W. Kim, and S. Yokota, “A study on a soft microgripper using MEMS-based divided electrode type flexible electro-rheological valves,” Mechatronics, Vol.29, pp. 103-109, 2015.
- [25] H. Lorenz, M. Despont, N. Fahrni, N. LaBianca, P. Renaud, and P. Vettiger, “SU-8: a low-cost negative resist for MEMS,” J. of Micromechanics and Microengineering, Vol.7, No.3, pp. 121-124, 1997.
- [26] C. J. Robin, A. Vishnoi, and K. N. Jonnalagadda, “Mechanical Behavior and Anisotropy of Spin-Coated SU-8 Thin Films for MEMS,” J. of Microelectromechanical Systems, Vol.23, Issue 1, pp. 168-180, 2014.
- [27] M. N. M. Zubir, B. Shirinzadeh, and Y. Tian, “Development of a novel flexure-based microgripper for high precision micro-object manipulation,” Sensors and Actuators A: Physical, Vol.150, Issue 2, pp. 257-266, 2009.
- [28] M. Leester-Schadel, B. Hoxhold, C. Lesche, S. Demming, and S. Buttgenbach, “Micro actuators on the basis of thin SMA foils,” Microsystem Technologies, Vol.14, No.4, pp. 697-704, 2008.
- [29] F. Krecinic, T. Chu Duc, G. K. Lau, and P. M. Sarro, “Finite element modeling and experimental characterization of an electro-thermally actuated silicon-polymer micro gripper,” J. of Micromechanics and Microengineering, Vol.18, No.6, 064007, 2008.
- [30] R. Lumia and M. Shahinpoor, “IPMC microgripper research and development,” J. of Physics: Conf. Series, Vol.127, 012002, 2008.
- [31] S. Guo, T. Fukuda, and K. Asaka, “A new type of fish-like underwater microrobot,” IEEE/ASME Trans. on Mechatronics, Vol.8, pp. 136-141, 2003.
- [32] K. Yoshida, T. Muto, J.-W. Kim, and S. Yokota, “An ER microactuator with built-in pump and valve,” Int. J. Automation Technol., Vol.6, No.4, pp. 468-475, 2012.
- [33] D. Han, K. Yoshida, and J.-W. Kim, “A Novel Hybrid Removal Technology for High-Aspect-Ratio SU-8 Micromolds in ECF (Electro-Conjugate Fluid) Micropumps Fabrication by UV-LIGA,” J. of Microelectromechanical Systems, Vol.27, Issue 5, pp. 818-826, 2018.
- [34] M. Takeda, “Applications of MEMS to industrial inspection,” Technical Digest. MEMS 2001. Proc. of 14th IEEE Int. Conf. on Micro Electro Mechanical Systems (Cat. No.01CH37090), Interlaken, Switzerland, pp. 182-191, 2001.
This article is published under a Creative Commons Attribution-NoDerivatives 4.0 Internationa License.