Paper:
Preliminary Design of a Three-Finger Underactuated Adaptive End Effector with a Breakaway Clutch Mechanism
Kuat Telegenov*, Yedige Tlegenov*, Shahid Hussain**, and Almas Shintemirov*
*Department of Robotics and Mechatronics, School of Science and Technology, Nazarbayev University
53 Kabanbay Batyr Avenue, Astana, Kazakhstan
**School of Mechanical, Materials and Mechatronic Engineering, University of Wollongong
Wollongong, New South Wales 2522, Australia
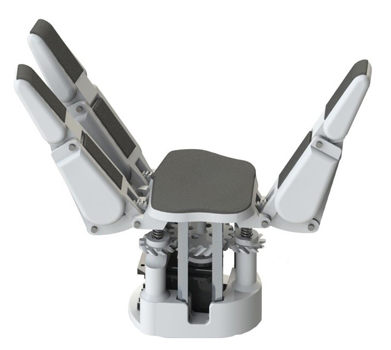
- [1] S. Jacobsen, E. Iversen, D. Knutti, R. Johnson, and K. Biggers, “Design of the Utah/M.I.T. Dextrous Hand,” Proc. of the 1986 IEEE Int. Conf. on Robotics and Automation, pp. 1520-1532, 1986.
- [2] M. Baril, T. Laliberte, C. Gosselin, and F. Routhier, “On the Design of a Mechanically Programmable Underactuated Anthropomorphic Prosthetic Gripper,” ASME J. of Mechanical Design, Vol.135, No.12, p. 121008, 2013.
- [3] T. Laliberte, L. Birglen, and C. Gosselin, “Underactuation in robotic grasping hands, Machine Intelligence & Robotic Control,” Vol.4, No.3, pp. 1-11, 2002.
- [4] Y. Ando, “Microgripper,” J. of Robotics and Mechatronics, Vol.2, No.3, pp. 214-216, 1990.
- [5] F. Chen, K. Sekiyama, B. Sun, P. Di, J. Huang, H. Sasaki, and T. Fukuda, “Design and Application of an Intelligent Robotic Gripper for Accurate and Tolerant Electronic Connector Mating,” J. of Robotics and Mechatronics, Vol.24, No.3, pp. 441-451, 2012.
- [6] S. Bachche and K. Oka, “Design, Modeling and Performance Testing of End-Effector for Sweet Pepper Harvesting Robot Hand,” J. of Robotics and Mechatronics, Vol.25, No.4, pp. 705-717, 2013.
- [7] G. Figliolini and M. Sorli, “Open-Loop Force Control of a Three-Finger Gripper Through PWM Modulated Pneumatic Digital Valves,” J. of Robotics and Mechatronics, Vol.12, No.4, pp. 480-493, 2000.
- [8] A. Namiki, Y. Imai, M. Kaneko, and M. Ishikawa, “Development of a High-Speed Multifingered Hand System,” Proc. of the 2003 IEEE/RSJ Int. Conf. on Intelligent Robots and Systems, pp. 2666-2671, 2004.
- [9] W. Townsend, “The Barret Hand grasper - programmably flexible part handling and assembly,” Industrial Robot, Vol.27, pp. 181-188, 2000.
- [10] L. U. Odhner et al., “A compliant, underactuated hand for robust manipulation,” Int. J. of Robotics Research, Vol.33, No.5, pp. 736-752, 2014.
- [11] S. J. Bartholet, “Reconfigurable end effector,” U.S. Patent No:5108140, 1992.
- [12] C. Gosselin, “Adaptive Robotic Mechanical Systems: A Design Paradigm,” ASME J. of Mechanical Design, Vol.128, No.1, pp. 192-198, 2005.
- [13] C. Beyer, “Strategic implications of current trends in additive manufacturing,” ASME J. of Manufacturing Science and Engineering, Vol.136, No.6, p. 064701, 2014.
- [14] R. R. Ma, L. U. Odhner, and A. M. Dollar, “A modular, open-source 3D printed underactuated hand,” Proc. of the 2013 IEEE Int. Conf. on Robotics and Automation, pp. 2737-2743, 2013.
- [15] Z. Kappassov, Y. Khassanov, A. Saudabayev, A. Shintemirov, and H. A. Varol, “Semi-anthropomorphic 3D printed multigrasp hand for industrial and service robots,” Proc. of the 2013 IEEE Int. Conf. on Mechatronics and Automation, pp. 1697-1702, 2013.
- [16] Y. Tlegenov, K. Telegenov, and A. Shintemirov, “An open-source 3D printed underactuated robotic gripper,” Proc. of the 10th IEEE/ASME Int. Conf. on Mechatronic and Embedded Systems and Applications, pp. 1-6, 2014.
- [17] C. Chen, “Mechatronics Design of Multi-Finger Robot Hand,” 12th Int. Conf. on Control, Automation and Systems, pp. 1491-1496, 2012.
- [18] C. Liu, H. Qiao, J. Su, and P. Zhang, “Vision-based 3-D grasping of 3-D objects with a simple 2-D gripper,” IEEE Trans. on Systems, Man, and Cybernetics: Systems, Vol.44, pp. 605-620, 2014.
- [19] J. M. Romano, K. Hsiao, G. Niemeyer, S. Chitta, and K. J. Kuchenbecker, “Human-inspired robotic grasp control with tactile sensing,” IEEE Trans. on Robotics, Vol.27, pp. 1067-1079, 2011.
- [20] T. Laliberte and C. Gosselin, “Actuation system for highly underactuated gripping mechanism,” U.S. Patent No:6505870, 2003.
- [21] L. J. Caron and C. Deguire, “Mechanical Finger,” PCT Patent WO2010/142043 A1, 2010.
- [22] T. Laliberte and C. Gosselin, “Underactuation in space robotic hands,” Int. Symposium on Artificial Intelligence, Robotics and Automation in Space, pp. 18-21, 2001.
- [23] S. Montambault and C. Gosselin, “Analysis of Underactuated Mechanical Grippers,” ASME J. of Mechanical Design, Vol.123, No.3, pp. 367-374, 2001.
- [24] L. Birglen and C. Gosselin, “Geometric design of three-phalanx underactuated fingers,” ASME J. of Mechanical Design, Vol.128, No.2, pp. 356-364, 2005.
- [25] L. Birglen and C. Gosselin, “Kinetostatic analysis of underactuated fingers,” IEEE Trans. on Robotics and Automation, Vol.20, No.2, pp. 211-221, 2004.
- [26] I. A. Bonev, D. Zlatanov, and C. Gosselin, “Singularity Analysis of 3-DOF Planar Parallel Mechanisms via Screw Theory,” ASME J. of Mechanical Design, Vol.125, No.3, p. 537-581, 2003.
- [27] L. Birglen and C. Gosselin, “Force analysis of connected differential mechanisms: application to grasping,” Int. J of Robotics Research, Vol.25, No.10, pp. 1033-1046, 2006.
- [28] R. R. Ma, L. U. Odhner, and A. M. Dollar, “A modular, open-source 3D printed underactuated hand,” Proc. of the 2013 IEEE Int. Conf. on Robotics and Automation, pp. 2737-2743, 2013.
- [29] K. Telegenov, Y. Tlegenov, and A. Shintemirov, “An underactuated adaptive 3D printed robotic gripper,” Proc. of the 10th France-Japan/8th Europe-Asia Congress on Mechatronics, pp. 110-115, 2014.
- [30] N. T. Ulrich, “Methods and apparatus for mechanically intelligent grasping,” U.S. Patent No:4957320, 1990.
- [31] S. Hussain, Q. Xie, and P. K. Jamwal, “Control of a Robotic Orthosis for Gait Rehabilitation,” Robotics and Autonomous Systems, Vol.61. No.911-919, 2013.
This article is published under a Creative Commons Attribution-NoDerivatives 4.0 Internationa License.