Review:
Current State of the Art of Multi-Axis Control Machine Tools and CAM System
Yoshimi Takeuchi
Chubu University, 1200 Matsumoto-cho, Kasugai, Aichi 487-8501, Japan
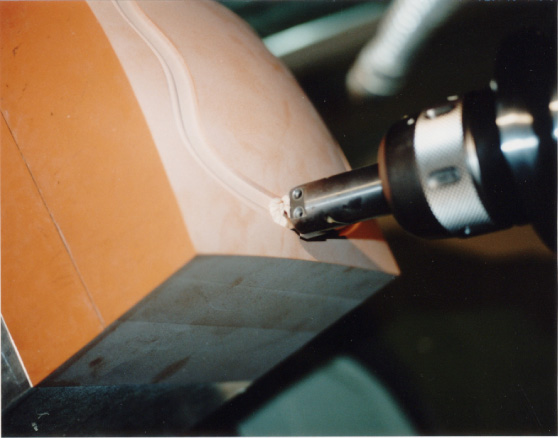
- [1] K. Nakamoto and K. Shirase, “Simulation Technologies for the Development of an Autonomous and Intelligent Machine Tools,” Int. J. of Automation Technology, Vol.7, No.1, pp. 6-15, 2013.
- [2] Y. Takeuchi and T. Idemura, “5-Axis Control Machining and Grinding Based on Solid Model,” Annals of the CIRP, Vol.40/1, pp. 455-458, 1991.
- [3] T. Lozano-Perez, “Special planning: a configuration space approach,” IEEE Trans. on Computers, Vol.32, No.2, pp. 108-120, 1983.
- [4] K. Morishige, K. Kase, and Y. Takeuchi, “Collision-Free Tool Path Generation Using 2-Dimensional C-Space for 5-Axis Control Machining,” Int. J. of Advanced Manufacturing Technology, Vol.13, No.6, pp. 393-400, 1997.
- [5] K. Morishige, Y. Takeuchi, and K. Kase, “Tool Path Generation Using C-Space for 5-Axis Control machining,” J. of Manufacturing Science and Engineering, Trans. of the ASME, Vol.121, No.1, pp. 144-149, 1999.
- [6] K. Morishige and Y. Takeuchi, “Strategic Tool Attitude Determination for Five-Axis Control Machining Based on Configuration Space,” CIRP-J. of Manufacturing Systems, Vol.31, No.3 pp. 247-252, 2002.
- [7] M. Morikawa, T. Ishida, K. Teramoto, and Y. Takeuch, “5-Axis Control Tool Path Generation Using Curved Surface Interpolation,” JSME Int. J. Series C, Vol.49, No.4, pp. 1209-1214, 2006.
- [8] T. Inoue, T. Ishida, and Y. Takeuchi, “Rapid 5-Axis Control Tool Path Generation by Means of Interference-free Space Concept,” Proc. of 4th Int. Conf. on LEM21, JSME, Fukuoka pp. 489-494, 2007.
- [9] Y. Takeuchi and T. Watanabe, “Generation of 5-Axis Control Collision-Free Tool Path and Postprocessing for NC Data,” Annals of the CIRP, Vol.41/1 pp. 539-542, 1992.
- [10] M. Sudo, “The Advanced Control Technologies for 5-axis Machining,” Proc. of 12th Int. Machine Tool Engineers’ Conf. (IMEC), Tokyo, pp. 248-257, 2006.
- [11] S. Takahashi, K. Morishige, and Y. Takeuchi, “NC Data Generation for Five-axis Control Machining Using Curved Interpolation (Application of Five-dimensional Non-Uniform B-Spline Curve),” J. of the Japan Society for Precision Engineering, Vol.65, No.12, pp. 1740-1744, 1999 (in Japanese).
- [12] K. Konishi, Y. Fukuda, and K. Iwata, “Development of CAM system for 5-Axis Controlled Machine Tool Using NURBS Interpolation,” Trans. of the Japan Society of Mechanical Engineers, Series C, Vol.67, No.657, pp. 1675-1681, 2001 (in Japanese).
- [13] Y. Tominaga, K. Teramoto, T. Ishida, H. Honda, and Y. Takeuchi, “Curved Interpolation CL Data Creation for 5-axis Control Machining Expressed by Non-Uniform B-Spline,” Trans. of the Japan Society of Mechanical Engineers, Series C, Vol.72, No.719, pp. 2286-2292, 2006 (in Japanese).
- [14] Y. Ueda, T. Ishida, and Y. Takeuchi, “Development of CAM System for 5-axis NURBS Interpolated Machining (NC Data Generation by Generalized Post-Processor),” Trans. of the Japan Society of Mechanical Engineers, Series C, Vol.75, No.749, pp. 216-222, 2009 (in Japanese).
- [15] K. Morishige, T. Nasu, and Y. Takeuchi, “Five-Axis Control Sculptured Surface Machining Using Conicoid End Mill,” G. J. Olling, B. K. Choi, and R. B. Jerard (Eds.), Machining Impossible Shapes, pp. 366-375, 1998.
- [16] S. Ishizuka, K.Morishige, K. Kase, and Y. Takeuchi, “Development of Tool Grinding System for Conicoid EndMill,” J. of JSPE, Vol.64, No.10, pp. 1456-1460, 1998 (in Japanese).
- [17] H. Suzuki, Y. Kuwano, K. Goto, Y. Takeuchi, and M. Sato, “Development of CAM System for 5-Axis Controlled Machine Tools,” Proc. 23rd North American Metal Research Conf., NAMRI/SME pp. 187-192, 1995.
- [18] T. Umehara, K. Nakamoto, T. Ishida, and Y. Takeuchi, “Development of a Process Planning System for 3+2 Control Rough Milling,” Proc. of Int. Symp. on Flexible Automation, CD-ROM (JPL2660), pp. 1-6, 2010.
- [19] T. Moriwaki, “Multi-functional Machine Tool,” Annals of the CIRP, Vol.57/2, pp. 736-749, 2008.
- [20] Y. f. Chen, Z. d. Huang, L. p. Chen, and Q. f. Wang, “Parametric Process Planning Based on Feature Parameters of Parts,” Int. J. of Advanced Manufacturing Technology, Springer, Vol.28, No.78, pp. 727-736, 2006.
- [21] K. Kubota, T. Kotani, K. Nakamoto, T. Ishida, and Y. Takeuchi, “Development of CAM System for Multi-Tasking Machine Tools,” J. of Adv. Mech. Design, Systems, and Manuf., JSME, Vol.4, No.5, pp. 816-826, 2010.
- [22] K. Nakamoto, K. Kubota, T. Ishida, and Y. Takeuchi, “Development of 5-axis Control CAM System for Multi-tasking Machine Tools,” Proc. of 45st CIRP Conf. onManufacturing Systems (CIRPCMS2012), Athens, pp. 266-270, 2012.
- [23] K. Nakamoto, D. Hamada, and Y. Takeuchi, “Development of CAPP System for Multi-tasking Machining of Complex Shapes,” Proc. of 6th Int. Conf. on LEM21, JSME, Matsushima, SD-Card, pp. 527-530, 2013.
- [24] Y. Takeuchi, M. Sato, and H. Suzuki, “New Concept of Machining by Means of Six-Axis Control,” Annals of the CIRP, Vol.43/1, pp. 341-344, 1994.
- [25] F. H. Japitana, K. Morishige, and Y. Takeuchi, “6-Axis Controlled Ultrasonic Vibration Cutting in Fabrication of Sharp Corner,” Int. J. of Advanced Manufacturing Technology, Vol.21, No.8, pp. 564-570, 2003.
- [26] F. H. Japitana, K.Morishige, and Y. Takeuchi, “6-Axis Control Cutting of Overhanging Curved Grooves by Means of Non-Rotational Tool with Application of Ultrasonic Vibrations,” Int. J. of Machine Tools & Manufacture, Vol.44, pp. 479-486, 2004.
- [27] F. H. Japitana, K. Morishige, and Y. Takeuchi, “Highly efficient manufacture of groove with sharp corner on adjoining surfaces by 6-axis control ultrasonic vibration cutting,” Precision Engineering, Vol.29, pp. 431-439, 2005.
This article is published under a Creative Commons Attribution-NoDerivatives 4.0 Internationa License.