Paper:
Cyber-Physical-Human Systems for Error Recovery in a Bin-Picking Task
Shunki Itadera
, Toshio Ueshiba
, Enrique Coronado
, and Yukiyasu Domae

Industrial Cyber-Physical Systems Research Center, National Institute of Advanced Industrial Science and Technology (AIST)
2-4-7 Aomi, Koto-ku, Tokyo 135-0064, Japan
This study presents an error recovery architecture for future variable-mix variable-volume production based on cyber-physical-human systems (CPHS). It focuses on bin picking, which is a crucial manufacturing process for handling bulk industrial parts during kitting. One of the main challenges in bin picking is efficiently introducing perturbations to arbitrarily placed parts and make all parts graspable and resolve deadlock situations. For example, a suction-type gripper is advantageous for handling objects stably without geometric models as it can easily adhere to flat surfaces. However, the success rate of bin picking using a suction gripper depends on the orientation of the target part. If its flat graspable surface does not face upward, the suction gripper cannot attach to and pick up the target object, resulting in a deadlock. In this case, an external force must be applied to change the orientation of the target object to resume the bin-picking process. A conventional, albeit inefficient, solution is a human worker or an additional mechanism that perturbs the container. Because applying such a perturbation by a versatile robot is challenging due to the limited physical information, a promising approach for efficient error recovery is a combination of human remote instruction and automated trajectory planning. This study developed a CPHS-based architecture to facilitate error recovery through smooth human-robot collaboration. We perform three experiments to demonstrate the feasibility of this approach for efficient error recovery.
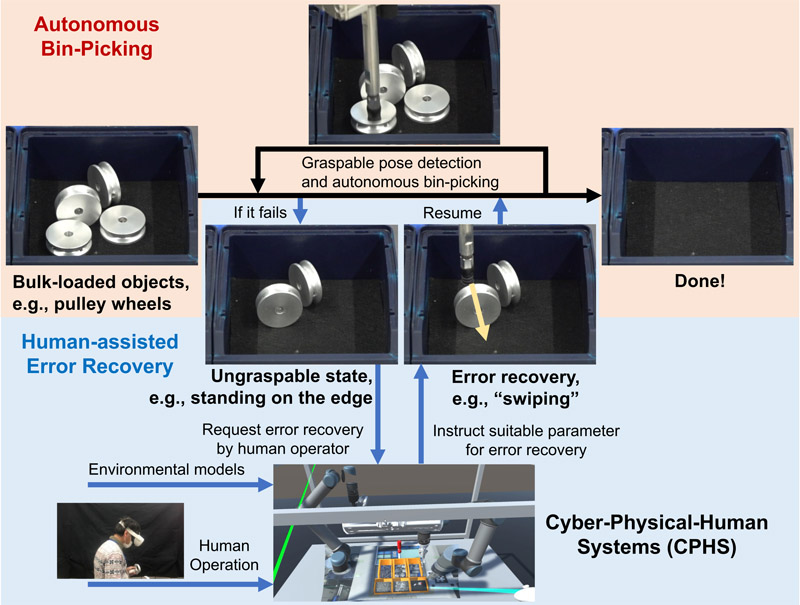
CPHS error recovery for pulley wheel picking
- [1] T. Cerquitelli, D. J. Pagliari, A. Calimera, L. Bottaccioli, E. Patti, A. Acquaviva, and M. Poncino, “Manufacturing as a data-driven practice: methodologies, technologies, and tools,” Proc. of the IEEE, Vol.109, No.4, pp. 399-422, 2021. https://doi.org/10.1109/JPROC.2021.3056006
- [2] M. Hattinger and K. Stylidis, “Transforming quality 4.0 towards resilient operator 5.0 needs,” Procedia CIRP, Vol.120, pp. 1600-1605, 2023. https://doi.org/10.1016/j.procir.2023.12.002
- [3] E. Coronado, T. Kiyokawa, G. A. G. Ricardez, I. G. Ramirez-Alpizar, G. Venture, and N. Yamanobe, “Evaluating quality in human-robot interaction: A systematic search and classification of performance and human-centered factors, measures and metrics towards an industry 5.0,” J. of Manufacturing Systems, Vol.63, pp. 392-410, 2022. https://doi.org/10.1016/j.jmsy.2022.04.007
- [4] S. Huang, B. Wang, X. Li, P. Zheng, D. Mourtzis, and L. Wang, “Industry 5.0 and society 5.0–Comparison, complementation and co-evolution,” J. of Manufacturing Systems, Vol.64, pp. 424-428, 2022. https://doi.org/10.1016/j.jmsy.2022.07.010
- [5] D. Romero and J. Stahre, “Towards the resilient operator 5.0: The future of work in smart resilient manufacturing systems,” Procedia Cirp, Vol.104, pp. 1089-1094, 2021. https://doi.org/10.1016/j.procir.2021.11.183
- [6] S. K. Sowe, E. Simmon, K. Zettsu, F. de Vaulx, and I. Bojanova, “Cyber-physical-human systems: Putting people in the loop,” IT Professional, Vol.18, pp. 10-13, 2016. https://doi.org/10.1109/MITP.2016.14
- [7] A. M. Annaswamy, P. P. Khargonekar, F. Lamnabhi-Lagarrigue, and S. K. Spurgeon, “Cyber-physical-human systems: Fundamentals and applications,” John Wiley & Sons, Inc., 2023.
- [8] “A design framework for cyber-physical-human-systems,” Advances in Transdisciplinary Engineering, Vol.41, pp. 23-32, 2023. https://doi.org/10.3233/ATDE230594
- [9] G. Fantoni, M. Santochi, G. Dini, K. Tracht, B. Scholz-Reiter, J. Fleischer, T. K. Lien, G. Seliger, G. Reinhart, J. Franke, H. N. Hansen, and A. Verl, “Grasping devices and methods in automated production processes,” CIRP Annals, Vol.63, pp. 679-701, 2014. https://doi.org/10.1016/j.cirp.2014.05.006
- [10] J. Aldrini, I. Chihi, and L. Sidhom, “Fault diagnosis and self-healing for smart manufacturing: A review,” J. of Intelligent Manufacturing, Vol.35, pp. 2441-2473, 2024. https://doi.org/10.1007/s10845-023-02165-6
- [11] P. Loborg, “Error recovery in automation–an overview,” AAAI Spring Symposium on Detecting and Resolving Errors in Manufacturing Systems, pp. 94-100, 1994.
- [12] J. S. Laursen, U. P. Schultz, and L.-P. Ellekilde, “Automatic error recovery in robot assembly operations using reverse execution,” 2015 IEEE/RSJ Int. Conf. on Intelligent Robots and Systems (IROS), Vol.2015-December, pp. 1785-1792, 2015. https://doi.org/10.1109/IROS.2015.7353609
- [13] C. M. Baydar and K. Saitou, “Automated generation of robust error recovery logic in assembly systems using genetic programming,” J. of Manufacturing Systems, Vol.20, pp. 55-68, 2001. https://doi.org/10.1016/S0278-6125(01)80020-0
- [14] G. Boschetti, T. Sinico, and A. Trevisani, “Improving robotic bin-picking performances through human–robot collaboration,” Applied Sciences, Vol.13, No.9, Article No.5429, 2023. https://doi.org/10.3390/app13095429
- [15] K. N. Kaipa, A. S. Kankanhalli-Nagendra, N. B. Kumbla, S. Shriyam, S. S. Thevendria-Karthic, J. A. Marvel, and S. K. Gupta, “Addressing perception uncertainty induced failure modes in robotic bin-picking,” Robotics and Computer-Integrated Manufacturing, Vol.42, pp. 17-38, 2016. https://doi.org/10.1016/j.rcim.2016.05.002
- [16] F. von Drigalski, C. Nakashima, Y. Shibata, Y. Konishi, J. C. Triyonoputro, K. Nie, D. Petit, T. Ueshiba, R. Takase, Y. Domae, T. Yoshioka, Y. Ijiri, I. G. Ramirez-Alpizar, W. Wan, and K. Harada, “Team o2as at the world robot summit 2018: An approach to robotic kitting and assembly tasks using general purpose grippers and tools,” Advanced Robotics, Vol.34, Nos.7-8, pp. 514-530, 2020. https://doi.org/10.1080/01691864.2020.1734481
- [17] F. von Drigalski, C. C. Beltran-Hernandez, C. Nakashima, Z. Hu, S. Akizuki, T. Ueshiba, M. Hashimoto, K. Kasaura, Y. Domae, W. Wan, and K. Harada, “Team o2ac at the world robot summit 2020: Towards jigless, high-precision assembly,” Advanced Robotics, Vol.36, No.22, pp. 1213-1227, 2022. https://doi.org/10.1080/01691864.2022.2138541
- [18] Y. Domae, H. Okuda, Y. Taguchi, K. Sumi, and T. Hirai, “Fast graspability evaluation on single depth maps for bin picking with general grippers,” 2014 IEEE Int. Conf. on Robotics and Automation (ICRA), pp. 1997-2004, 2014. https://doi.org/10.1109/ICRA.2014.6907124
- [19] E. Coronado, S. Itadera, and I. G. Ramirez-Alpizar, “Integrating virtual, mixed, and augmented reality to human–robot interaction applications using game engines: A brief review of accessible software tools and frameworks,” Applied Sciences, Vol.13, Article No.1292, 2023. https://doi.org/10.3390/app13031292
- [20] E. Coronado, T. Ueshiba, and I. G. Ramirez-Alpizar, “A path to industry 5.0 digital twins for human–robot collaboration by bridging nep+ and ros,” Robotics, Vol.13, No.2, Article No.28, 2024. https://doi.org/10.3390/robotics13020028
- [21] S. Itadera and Y. Domae, “Simulation-based motion priority optimization for manufacturing and tele-recovery robot cooperation,” 2024 IEEE Int. Conf. on Advanced Robotics and Its Social Impacts (ARSO), pp. 25-30, 2024. https://doi.org/10.1109/ARSO60199.2024.10557804
This article is published under a Creative Commons Attribution-NoDerivatives 4.0 Internationa License.