Paper:
Skill Implemented Motion Planning for Precision Assembly Task of Part Mating Gears
Takahito Yamashita
, Hikaru Suzuki
, and Ryosuke Tasaki

Department of Mechanical Engineering, College of Science and Engineering, Aoyama Gakuin University
5-10-1 Fuchinobe, Chuo-ku, Sagamihara, Kanagawa 252-5258, Japan
Corresponding author
This study aims to realize a precision assembly robot system. This system focuses on the mating of precision parts, which is difficult with the current technology, and uses workpiece movements and the sensation of human fingertips as a reference to eliminate assembly failures, such as shaft and hole biting. This approach solves the limitations in robotizable tasks, long teaching times, and possible assembly failures by robots. The proposed method involves measuring human task data, analyzing the movement of assembly parts using averaging (a simple feature extraction method), and deriving the corresponding robot movements. Furthermore, a system is developed to predict decisive assembly failures from force information obtained during tasks by analyzing the force sensation of the human fingertips using a support vector machine (a type of machine learning). Equipped with the prediction system and the derived workpiece motion, the robot performs assembly tasks that typically require human skills.
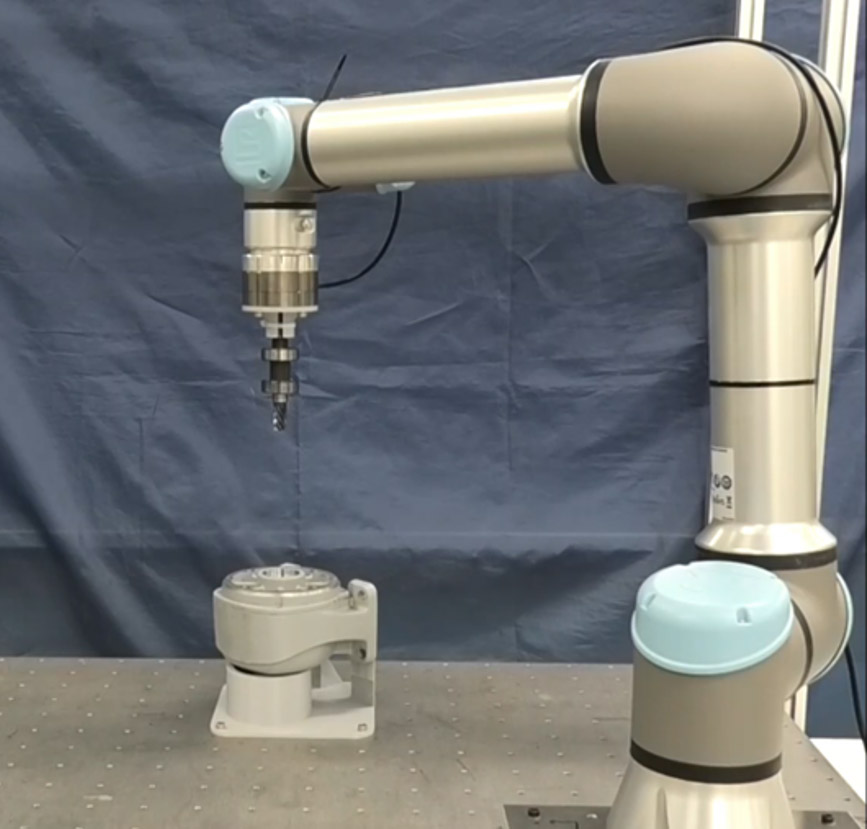
We propose an assembly system based on human tasks
- [1] Y. Takenaka, “The influence of the declining birth-rate on lifestyle formation,” Bull. Cent. Res. 21st Century Soc., Vol.10, pp. 103-117, 2019 (in Japanese). https://doi.org/10.34480/00000017
- [2] R. Zhang et al., “A reinforcement learning method for human-robot collaboration in assembly tasks,” Robot. Comput.-Integr. Manuf., Vol.73, Article No.102227, 2019. https://doi.org/10.1016/j.rcim.2021.102227
- [3] T. Ren, Y. Dong, D. Wu, and K. Chen, “Learning-based variable compliance control for robotic assembly,” J. Mech. Robot., Vol.10, No.6, Article No.061008, 2018. https://doi.org/10.1115/1.4041331
- [4] F. Li, Q. Jiang, S. Zhang, M. Wei, and R. Song, “Robot skill acquisition in assembly process using deep reinforcement learning,” Neurocomputing, Vol.345, pp. 92-102, 2019. https://doi.org/10.1016/j.neucom.2019.01.087
- [5] Y.-L. Kim, K.-H. Ahn, and J.-B. Song, “Reinforcement learning based on movement primitives for contact tasks,” Robot. Comput.-Integr. Manuf., Vol.62, Article No.101863, 2020. https://doi.org/10.1016/j.rcim.2019.101863
- [6] B. Ti, Y. Gao, M. Shi, and J. Zhao, “Generalization of orientation trajectories and force–torque profiles for learning human assembly skill,” Robot. Comput.-Integr. Manuf., Vol.76, Article No.102325, 2022. https://doi.org/10.1016/j.rcim.2022.102325
- [7] H. Asada and Y. Asari, “The identification of tool suspension impedance via the measurement of expert motions and its application to robot teaching,” Trans. Soc. Instrum. Control Eng., Vol.24, No.12, pp. 1292-1298, 1988 (in Japanese). https://doi.org/10.9746/sicetr1965.24.1292
- [8] H. Asada and H. Izumi, “Teaching and program generation for the hybrid position/force control via the measurement of human manipulation tasks,” J. Robot. Soc. Jpn., Vol.5, No.6, pp. 452-459, 1987 (in Japanese). https://doi.org/10.7210/jrsj.5.452
- [9] Y. Fukumoto and K. Harada, “Force controlled assembly of a ring-shaped elastic part based on dynamic characteristics of skilled workers,” J. Robot. Soc. Jpn., Vol.36, No.2, pp. 159-167, 2018 (in Japanese). https://doi.org/10.7210/jrsj.36.159
- [10] Y. Fukumoto, N. Yamanobe, W. Wan, and K. Harada, “Force control design for robots based on correlation in human demonstration data,” Trans. JSME, Vol.85, No.874, Article No.18-00489, 2019 (in Japanese). https://doi.org/10.1299/transjsme.18-00489
- [11] J. Huang, T. Fukuda, and T. Matsuno, “Model-based intelligent fault detection and diagnosis for mating electric connectors in robotic wiring harness assembly systems,” IEEE/ASME Trans. Mechatron., Vol.13, No.1, pp. 86-94, 2008. https://doi.org/10.1109/TMECH.2007.915063
- [12] J. Huang, P. Di, T. Fukuda, and T. Matsuno, “Robust model-based online fault detection for mating process of electric connectors in robotic wiring harness assembly systems,” IEEE Trans. Control Syst. Technol., Vol.18, No.5, pp. 1207-1215, 2010. https://doi.org/10.1109/TCST.2009.2034735
- [13] S. Amemiya, T. Fuse, H. Okamoto, J. Tomita, and Y. Ozaki, “Anomaly judgment method in automation of assembling process,” Proc. of 2015 JSPE Spring Conf., pp. 953-954, 2015 (in Japanese). https://doi.org/10.11522/pscjspe.2015S.0_953
- [14] T. Matsuno, K. Shiratsuchi, J. Huang, and T. Fukuda, “Fault detection algorithm for thread fastening by robotic manipulator,” J. Robot. Soc. Jpn., Vol.30, No.8, pp. 804-812, 2012 (in Japanese). https://doi.org/10.7210/jrsj.30.804
- [15] Y. Yamada, K. Suita, K. Imai, H. Ikeda, and N. Sugimoto, “A robot system with safe contact detection and stopping capabilities based on human pain tolerance,” Trans. Jpn. Soc. Mech. Eng., Ser. C, Vol.63, No.614, pp. 3552-3557, 1997 (in Japanese). https://doi.org/10.1299/kikaic.63.3552
This article is published under a Creative Commons Attribution-NoDerivatives 4.0 Internationa License.