Paper:
Application and Mechanical Evaluation of Polyarylate Fiber Rope in Wire Drive Mechanism of Robotic Surgical Instruments
Kanta Nojima*, Kotaro Tadano**
, and Daisuke Haraguchi*

*National Institute of Technology, Tokyo College
1220-2 Kunugida-machi, Hachioji, Tokyo 193-0997, Japan
**Tokyo Institute of Technology
4259 Nagatsuta-cho, Midori-ku, Yokohama, Kanagawa 226-8503, Japan
In this study, a polyarylate fiber rope, which is a high-strength synthetic fiber rope, is used in the wire drive mechanism of a multi-degree of freedom (DOF) robotic forceps to evaluate its mechanical practicability. Using a nonconducting material for the drive wire, different from typical use of metallic wires made of stainless steel and tungsten, a technology is developed to simplify the insulation structure significantly, decrease the diameter of the robotic surgical instrument, and lower its cost. In this study, first, a prototype of the multi-DOF robotic forceps equipped with a polyetheretherketone (PEEK) resin flexible wrist joint part with an external diameter of 5 mm is manufactured. The prototype is used to evaluate the assembling of a polyarylate fiber rope with a diameter of 0.34 mm in a multi-DOF mechanism and examine the endurance of the rope to mechanical motions under a single-use assumption. As fastening structures to assemble the rope – a crimp terminal using a hollow pipe and a thread knot – are examined individually by assembling them in the prototype robotic forceps and conducting strength tests of the tension generated by the drive. The test results show that the thread knot method exerts a stabler fastening strength than the hollow pipe method. However, a problem of the former is that the wire may break because of its strong contact with the edge of the hole of the wire guide. Subsequently, to evaluate the endurance of the rope to single-use operation motion, operation tests are conducted by implementing reciprocating bending motions of the flexible wrist joint part of the robotic forceps 1,000 times. The assembled rope endures the sliding within the flexible wrist joint part and the contact loading with the guide part and the fixed structure within the cartridge repeatedly. The endurance operation test results confirm that the drive transmission of the polyarylate fiber rope has sufficient mechanical endurance to 1,000 reciprocating bending motions of the PEEK flexible wrist joint part.
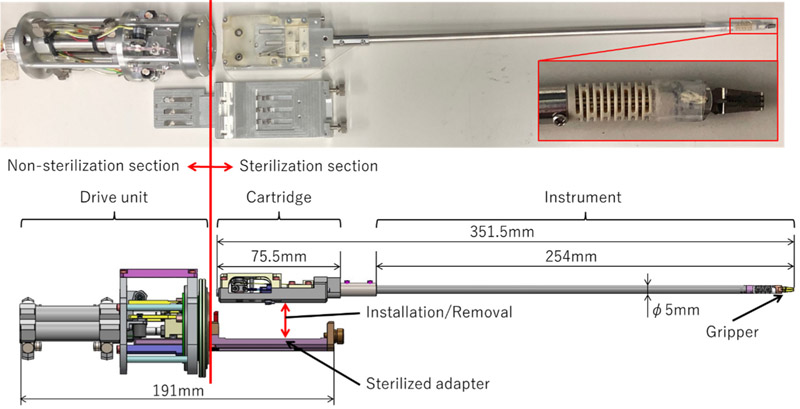
Robotic forceps with polyarylate fiber rope applied
- [1] K. Aizawa, D. Haraguchi, and K. Tadano, “Load Reduction Control on Tool-Insertion Port for Laparoscopic Surgical Robot Using Semi-Active Joints,” J. Robot. Mechatron., Vol.32, No.5, pp. 1000-1009, 2020. https://doi.org/10.20965/jrm.2020.p1000
- [2] M. Suzuki, T. Takahashi, and S. Aoyagi, “Fabrication and Characterization of a Biodegradable Hollow Microneedle from Chitosan,” J. Robot. Mechatron., Vol.32, No.2, pp. 401-407, 2020. https://doi.org/10.20965/jrm.2020.p0401
- [3] S. V. Bandara and J. Arata, “3.5mm Soft Robotic Forceps for Minimally Invasive Surgery,” Systems, Control and Information, Vol.63, No.10, pp. 420-423, 2019. https://doi.org/10.11509/isciesci.63.10_420
- [4] C. Ishii, K. Kobayashi, Y. Kamei, and Y. Nishitani, “Robotic Forceps Manipulator With a Novel Bending Mechanism,” IEEE/ASME Trans. on Mechatronics, Vol.15, No.5, pp. 671-684, 2010. https://doi.org/10.1109/TMECH.2009.2031641
- [5] C. Forbrigger et al., “Cable-less, Magnetically-Driven Forceps For Minimally Invasive Surgery,” IEEE Robotics and Automation Letters, Vol.4, No.2, pp. 1202-1207, 2019. https://doi.org/10.1109/LRA.2019.2894504
- [6] M. Bazman, N. Yilmaz, and U. Tumerdem, “Dexterous and back-drivable parallel robotic forceps wrist for robotic surgery,” 2018 IEEE 15th Int. Workshop on Advanced Motion Control (AMC), pp. 153-159, 2018. https://doi.org/10.1109/AMC.2019.8371079
- [7] F. Feng, W. Hong, and L. Xie, “Design of 3D-Printed Flexible Joints With Presettable Stiffness for Surgical Robots,” IEEE Access, Vol.8, pp. 79573-79585, 2020. https://doi.org/10.1109/ACCESS.2020.2991092
- [8] J. Arata, M. Mitsuishi, S. Warisawa, K. Tanaka, T. Yoshizawa, and M. Hashizume, “Development of a dexterous minimally-invasive surgical system with augmented force feedback capability,” 2005 IEEE/RSJ Int. Conf. on Intelligent Robots and Systems, pp. 3207-3212, 2005. https://doi.org/10.1109/IROS.2005.1545551
- [9] D. Haraguchi, K. Tadano, and K. Kawashima, “Development of a Pneumatically-Driven Robotic Forceps with a Flexible Wrist Joint,” Procedia CIRP, Vol.5, pp. 61-65, 2013. https://doi.org/10.1016/j.procir.2013.01.012
- [10] M. B. Hong and Y.-H. Jo, “Design of a Novel 4-DOF Wrist-Type Surgical Instrument With Enhanced Rigidity and Dexterity,” IEEE/ASME Trans. on Mechatronics, Vol.19, No.2, pp. 500-511, 2014. https://doi.org/10.1109/TMECH.2013.2245143
- [11] S. Jin, S. K. Lee, J. Lee, and S. Han, “Kinematic Model and Real-Time Path Generator for a Wire-Driven Surgical Robot Arm with Articulated Joint Structure,” Applied Sciences, Vol.9, No.19, Article No.4114, 2019. https://doi.org/10.3390/app9194114
- [12] J.-W. Suh and K.-Y. Kim, “Harmonious Cable Actuation Mechanism for Soft Robot Joints Using a Pair of Noncircular Pulleys,” ASME. J. Mechanisms Robotics, Vol.10, No.6, 2018. https://doi.org/10.1115/1.4041055
- [13] T. Kato, I. Okumura, S.-E. Song, A. J. Golby, and N. Hata, “Tendon-Driven Continuum Robot for Endoscopic Surgery: Preclinical Development and Validation of a Tension Propagation Model,” IEEE/ASME Trans. on Mechatronics, Vol.20, No.5, pp. 2252-2263, 2015. https://doi.org/10.1109/TMECH.2014.2372635
- [14] S. Xu, B. He, Y. Zhou, Z. Wang, and C. Zhang, “A Hybrid Position/Force Control Method for a Continuum Robot With Robotic and Environmental Compliance,” IEEE Access, Vol.7, pp. 100467-100479, 2019. https://doi.org/10.1109/ACCESS.2019.2928572
- [15] K. Takikawa, R. Miyazaki, T. Kanno, G. Endo, and K. Kawashima, “Pneumatically Driven Multi-DOF Surgical Forceps Manipulator with a Bending Joint Mechanism Using Elastic Bodies,” J. Robot. Mechatron., Vol.28, No.4, pp. 559-567, 2016. https://doi.org/10.20965/jrm.2016.p0559
- [16] D. Zhou, K. Sanada, and D. Haraguchi, “Robotic Forceps with a Flexible Wrist Joint Made of Super Engineering Plastic,” Sens. Mater., Vol.32, No.3, pp. 1027-1039, 2020. https://doi.org/10.18494/SAM.2020.2655
- [17] A. Horigome, G. Endo, A. Takata, and Y. Wakabayashi, “Development of New Terminal Fixation Method for Synthetic Fiber Ropes,” IEEE Robotics and Automation Letters, Vol.3, No.4, pp. 4321-4328, 2018. https://doi.org/10.1109/LRA.2018.2851033
- [18] A. Horigome and G. Endo, “Investigation of Repetitive Bending Durability of Synthetic Fiber Ropes,” IEEE Robotics and Automation Letters, Vol.3, No.3, pp. 1779-1786, 2018. https://doi.org/10.1109/LRA.2018.2800129
- [19] D. Asane, A. Schmitz, Y. Wang, and S. Sugano, “A Study on the Elongation Behaviour of Synthetic Fibre Ropes under Cyclic Loading,” 2020 IEEE/RSJ Int. Conf. on Intelligent Robots and Systems (IROS), pp. 6326-6331, 2020. https://doi.org/10.1109/IROS45743.2020.9341407
- [20] D. Zhou, K. Tadano, and D. Haraguchi, “Motion Control and External Force Estimation of a Pneumatically Driven Multi-DOF Robotic Forceps,” Applied Sciences, Vol.10, No.11, Article No.3679, 2020. https://doi.org/10.3390/app10113679
- [21] K.-Y. Lei, W.-J. Xie, S.-Q. Fu et al., “A comparison of the da Vinci Xi vs. da Vinci Si surgical systems for radical prostatectomy,” BMC Surg, Vol.21, Article No.409, 2021. https://doi.org/10.1186/s12893-021-01406-w
- [22] M. Golda-Cepaa, K. Engvall, M. Hakkarainen, and A. Kotarba, “Recent progress on parylene C polymer for biomedical applications: A review,” Progress in Organic Coatings, Vol.140, Article No.105493, 2020. https://doi.org/10.1016/j.porgcoat.2019.105493
This article is published under a Creative Commons Attribution-NoDerivatives 4.0 Internationa License.