Paper:
Hammering Acoustic Analysis Using Machine Learning Techniques for Piping Inspection
Kou Ikeda and Akiya Kamimura
National Institute of Advanced Industrial Science and Technology (AIST)
1-1-1 Umezono, Tsukuba, Ibaraki 305-8560, Japan
In Japan, the deterioration of industrial plants built during the period of high economic growth in the middle of the 20th century has recently become a social concern. Corrosion under insulation (CUI) of piping in such plants is a pressing problem. X-ray and ultrasound inspections are conventional methods for detecting CUI; however, these methods are time-consuming and expensive. Therefore, rapid and low-cost screening techniques for CUI are required. We develop a hammering-type inspection robot system that moves inside the piping and records hammering sounds. Furthermore, we propose an acoustic analysis method to identify anomalous parts from the hammering sound using machine learning techniques. Using three testing pipes, we can successfully identify anomalous parts through acoustic analysis using a deep neural network as a supervised learning method. However, in practical piping inspections, the detection of anomalies without training data is required for further applications. Therefore, we investigate unsupervised learning anomaly detection using an autoencoder and a variational autoencoder and report the results.
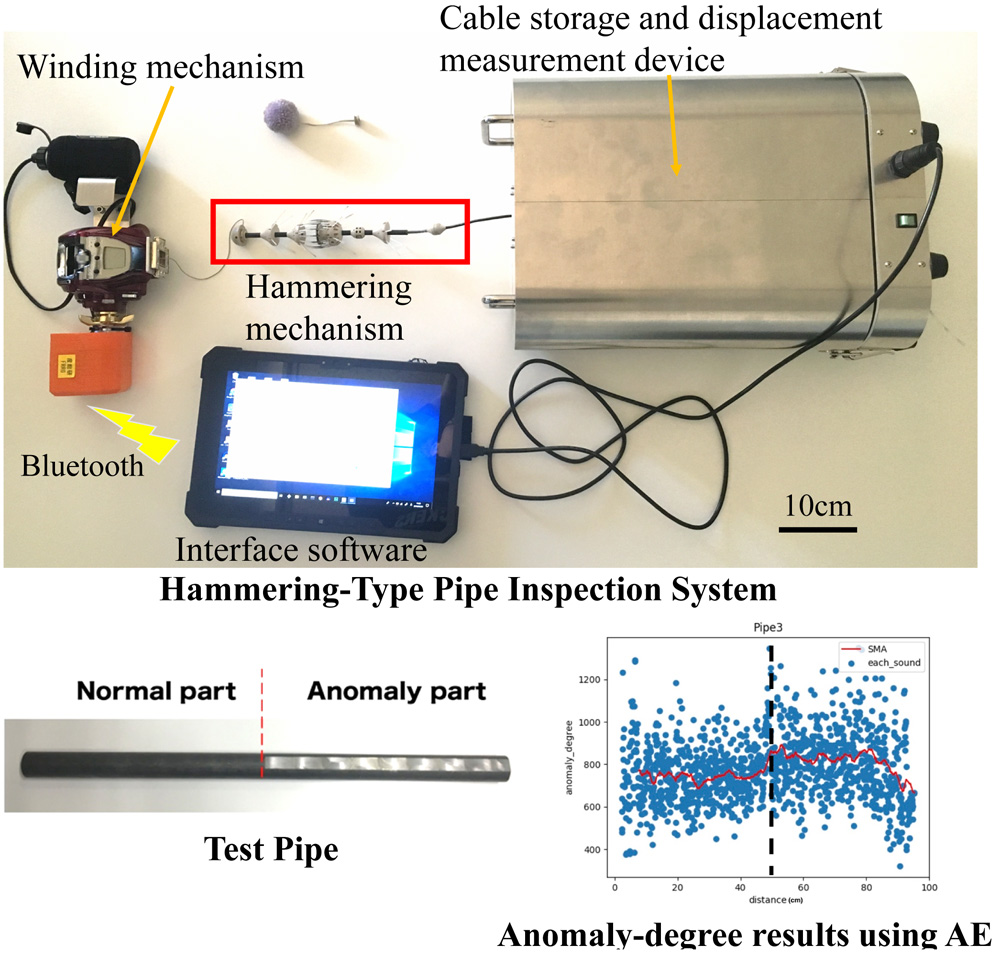
Developed hammering-type pipe inspection system and one of obtained anomaly-degree results
- [1] T. Kurihara, R. Miyake, N. Oshima, and M. Nakahara, “Investigation of the Actual Inspection Data for Corrosion Under Insulation (CUI) in Chemical Plant and Examination about Estimation Method for Likelihood of CUI,” Zairyo-to-Kankyo, Vol.59, pp. 291-297, 2010 (in Japanese).
- [2] T. Hamada and M. Katayama, “Novel System for Inspection of Piping Corrosion and Defects,” Toshiba Review, Vol.61, No.6, pp. 68-71, 2006 (in Japanese).
- [3] S. Abdul-Majid and A. Bal-Amesh, “Imaging Corrosion Under Insulation by Gamma Ray Backscattering Method,” Proc. of 18th World Conf. on Nondestructive Testing, 448, 2012.
- [4] J. E. Coulter, M. O. Robertson, and D. M. Stevens, “Acoustic emission for detection of corrosion under insulation,” U.S. Patent 5526689, 1996.
- [5] T. Zhang, H. Feng, and Z. Zeng, “Acoustic Emission Based Tank Bottom Floor Corrosion Detection,” Int. J. Automation Technol., Vol.7, No.2, pp. 205-210, 2013.
- [6] Y. Kawaguchi, I. Yoshida, and K. Kikuta, “Development of Internal Gas Pipe Inspection Robot,” J. Robot. Mechatron., Vol.7, No.5, pp. 371-376, 1995.
- [7] S. Kobayashi and K. Taguchi, “Development of a Wall Moving In-Pipe Robot,” J. Robot. Mechatron., Vol.15, No.2, pp. 238-243, 2003.
- [8] A. Bertetto and M. Ruggiu, “Low Cost Pipe-crawling Pneumatic Robot,” J. Robot. Mechatron., Vol.14, No.4, pp. 400-407, 2002.
- [9] S. Wakimoto, K. Suzumori, M. Takata, and J. Nakajima, “In-Pipe Inspection Micro Robot Adaptable to Changes in Pipe Diameter,” J. Robot. Mechatron., Vol.15, No.6, pp. 609-615, 2003.
- [10] R. Chalapathy and S. Chawla, “Deep Learning for Anomaly Detection: A Survey,” arXiv:1901.03407, 2019.
- [11] Y. Koizumi, S. Saito, H. Uematsum Y. Kawachi, and N. Harada, “Unsupervised Detection of Anomalous Sound based on Deep Learning and the Neyman-Pearson Lemma,” IEEE/ACM Trans. on Audio, Speech, and Language Processing, Vol.27, No.1, pp. 212-224, 2019.
- [12] Y. Kawachi, Y. Koizumi, and N. Harada, “Complementary Set Variational Autoencoder for Supervised Anomaly Detection,” Proc. of 2018 IEEE Int. Conf. on Acoustics, Speech and Signal Processing (ICASSP), pp. 2366-2370, 2018.
- [13] M. Yamaguchi, Y. Koizumi, and N. Harada, “AdaFlow: Domain-Adaptive Density Estimator with Application to Anomaly Detection and Unpaired Cross-Domain Translation,” Proc. of 2019 IEEE Int. Conf. on Acoustics, Speech and Signal Processing (ICASSP), pp. 3647-3651, 2019.
- [14] J. Ye, M. Iwata et al., “Statistical Impact-Echo Analysis Based on Grassmann Manifold Learning: Its Preliminary Results for Concrete Condition Assessment,” Proc. of 7th European Workshop on Structural Health Monitoring, pp. 1349-1356, 2014.
- [15] J. Y. L. Kasahara, H. Fujii, A. Yamashita, and H. Asama, “Clustering of Spatially Relevant Audio Data using Mel-Frequency Cepstrum for Diagnosis of Concrete Structure by Hammering Test,” Proc. of IEEE/SICE Int. Symp. on System Integration, pp. 787-792, 2017.
- [16] M. Sakurada and T. Yairi, “Anomaly detection using autoencoders with nonlinear dimensionality reduction,” Proc. Workshop on Machine Learning for Sensory Data Analysis (MLSDA), pp. 4-11, 2014.
- [17] D. P. Kingma and M. Welling, “Auto-Encoding Variational Bayes,” arXiv:1312.6114, 2013.
This article is published under a Creative Commons Attribution-NoDerivatives 4.0 Internationa License.