Paper:
Consideration of Multi-Degree of Freedom Vibration on Large-Sized Gantry Type Linear Motor Slider
Tetsuya Ojiro*, Toshiyuki Tachibana*, Hideki Honda*, Hiroshi Hamamatsu**, Kazuhiro Tsuruta***, and Tsuyoshi Hanamoto*
*Graduate School of Life Science and Systems Engineering, Kyushu Institute of Technology
2-4 Hibikino, Wakamatsu-ku, Kitakyushu, Fukuoka 808-0196, Japan
**National Institute of Technology, Kitakyushu College
5-20-1 Shii, Kokuraminami-ku, Kitakyushu, Fukuoka 802-0985, Japan
***Kyushu Sangyo University
2-3-1 Matsukadai, Higashi-ku, Fukuoka 813-8503, Japan
Many transport units for large production devices now incorporate large-sized gantry type linear motor sliders comprising two parallel linear sliders linked by a joint table. This type of linear motor slider develops a unique mechanical distortion, generating a repulsive force between the two axes that can raise the motor output forces higher than their rated limit. A previous study proposed a method to suppress the repulsive force. However, as feedback gains are set high, force references oscillate and the control system becomes unstable. In past study, yawing vibration suppression methods have been proposed. But, we consider that this vibration is not yawing vibration because the force references include same phase vibration with high gains. Therefore, the modal analysis is performed to analyze this vibration. As a result, it was found that the pitching vibration of the slider was greatly affected. This paper considers this vibration phenomenon, and suppression of the vibration by control method which is similar to impedance control is presented. Hence, it is shown that considering multi-degree of freedom vibration which means yawing vibration and pitching vibration included is important in order to control the large-sized gantry type linear motor sliders.
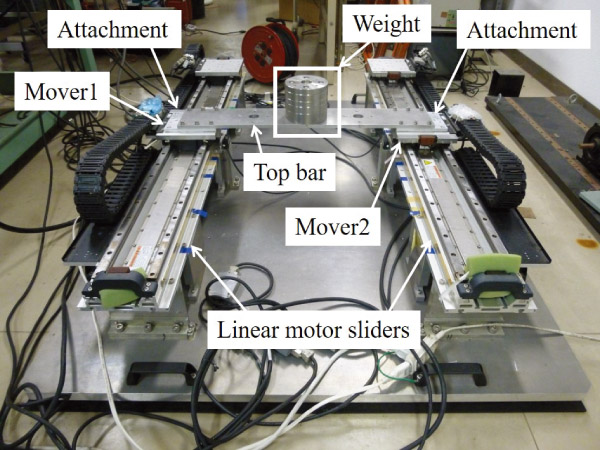
Gantry type linear motor slider
- [1] H. Yu and B. Fahimi, “Industrial servo applications of linear induction motors based on dynamic maximum force control,” 2010 25th Annual IEEE Applied Power Electronics Conf. and Exposition (APEC), pp. 1498-1502, 2010.
- [2] Y. Nakamura, K. Morimoto, and S. Wakui, “Position control of linear slider via feedback error learning,” 2011 3rd Pacific-Asia Conf. on Circuits, Communications and System (PACCS), pp. 1-4, 2011.
- [3] T. Yamada and K. Fujisaki, “Application of linear induction motor for tension supply and heating to thin sheet steel,” Electrical Engineering in Japan, Vol.168, No.2, pp. 38-47, 2009 (Denki Gakkai Ronbunshi, Vol.127-D, No.7, pp. 707-714, 2007).
- [4] M. Sogabe, Y. Iwashita, N. Sonoda, and Y. Kakino, “Study on the servo-stability of the tandem driven machine with linear motors,” J. of the Japan Society for Precision Engineering, Vol.73, No.5, pp. 605-610, 2007.
- [5] F. Terasaki, J. Kobayashi, R. Oguro, and F. Ohkawa, “A positioning control of a serial twin linear slider system with machine stand vibration,” 2006 IEEE Int. Conf. on Industrial Technology, pp. 2925-2930, 2011.
- [6] Y. Tomita, E. Kojima, S. Kawachi, Y. Koyanagawa, and S. Ootsuka, “Development and applications of sumitomo precision stage technologies for FPD process,” J. of the Japan Society for Precision Engineering, Vol.78, No.2, pp. 117-121, 2012.
- [7] T. Ojiro, H. Honda, K. Tsuruta, and T. Hanamoto, “Control Model for Large-Sized Gantry Type Linear Motor Slider,” Electrical Engineering in Japan, Vol.203, No.2, pp. 39-46, 2018 (Denki Gakkai Ronbunshi, Vol.137-D, No.10, pp. 746-752, 2017).
- [8] S. Ohashi, “Levitation and propulsion for a magnetically levitated conveyance system using a two-phase linear motor,” Electrical Engineering in Japan, Vol.165, No.3, pp. 65-72, 2008 (Denki Gakkai Ronbunshi, Vol.126-D, No.6, pp. 812-817, 2006).
- [9] S. Watanabe, R. Oguro, J. Kobayashi, and F. Ohkawa, “A Decoupling Method for Serial Twin Linear Slider System with Machine Stand Vibration,” 2006 IEEE Int. Symp. on Industrial Electronics, pp. 3032-3037, 2006.
- [10] R. Nakashima, S. Hao, H. Honda, R. Oguro, H. Miyakawa, and T. Tsuji, “Position control for a linear slider with twin linear drives,” Electrical Engineering in Japan, Vol.147, No.4, pp. 68-76, 2004 (Denki Gakkai Ronbunshi, Vol.123-D, No.3, pp. 278-285, 2003).
- [11] K. Sato, K. Tsuruta, T. Kikuchi, and H. Honda, “A robust adaptive control for parallel linear sliders using decoupling model,” 2008 SICE Annual Conf., pp. 848-853, August 2008.
- [12] T. Ojiro, K. Tsuruta, and H. Honda, “Synchronization Error Suppression Control for Twin-drive Table System,” The 12th Int. Conf. on Motion and Vibration (MOVIC2014), 3A21, pp. 1-8, 2014.
- [13] K. Watanabe, K. Watariyou, and N. Kiyota, “Twin synchronization control method,” Japan patent, JP2004-326252A, 2004.
- [14] T. Ojiro, H. Honda, K. Tsuruta, and T. Hanamoto, “Study on control method of the large-sized gantry type liner motor slider with distortion,” 2016 19th Int. Conf. on Electrical Machines and Systems (ICEMS), pp. 1-4, 2016.
- [15] T. Ojiro, H. Honda, T. Hanamoto, and K. Tsuruta, “Consideration on control method of the large-sized gantry-type linear motor slider,” 2017 IEEE Int. Conf. on Mechatronics and Automation (ICMA), pp. 1198-1203, 2017.
- [16] S. Yamamoto and S. Wakui, “Application of Robust Control Law for Linear Slider,” Int. J. Automation Technol., Vol.2, No.1, pp. 34-42, 2008.
- [17] H. Miyagawa, A. Yamamoto, H. Hamamatsu, S. Goto, and M. Nakamura, “The mechanical resonance repression control for high-speed positioning of linear motor by using velocity estimated observer of center of gravity,” J. of the Japan Society for Precision Engineering, Vol.68, No.2, pp. 284-290, 2002.
- [18] K. Tsuruta, T. Ojiro, N. Ushimi, and T. Sakaki, “Vibration suppression compensator using nonlinear observer for table positioning systems,” 2013 10th Int. Conf. on Ubiquitous Robots and Ambient Intelligence (URAI), pp. 481-485, 2013.
- [19] K. Tsuruta, K. Sato, N. Ushimi, and T. Fujimoto, “High-speed and high-precision position control using a sliding mode compensator,” Electrical Engineering in Japan, Vol.174, No.2, pp. 65-71, 2011 (Denki Gakkai Ronbunshi, Vol.128-D, No.9, pp. 1114-1120, 2008).
- [20] H. Sano, K. Sato, K. Ohishi, and T. Miyazaki, “Robust design of vibration suppression control system for crane using sway angle observer considering friction disturbance,” Electrical Engineering in Japan, Vol.184, No.3, pp. 36-46, 2013 (Denki Gakkai Ronbunshi, Vol.132-D, No.3, pp. 357-365, 2012).
- [21] M. Hosaka and T. Murakami, “Vibration control of flexible arm by multiple observer structure,” Electrical Engineering in Japan, Vol.154, No.2, pp. 68-75, 2006 (Denki Gakkai Ronbunshi, Vol.124-D, No.7, pp. 693-698, 2004).
- [22] P. Song, Y. Yu, and X. Zhang, “Impedance Control of Robots: An Overview,” 2017 2nd Int. Conf. on Cybernetics, Robotics and Control (CRC2017), pp. 51-55, 2017.
- [23] T. Senoo, M. Koike, K. Murakami, and M. Ishikawa, “Impedance Control Design Based on Plastic Deformation for a Robotic Arm,” IEEE Robotics and Automation Letters, Vol.2, No.1, pp. 209-216, 2017.
- [24] F. Aghili, “Robust impedance control of manipulators carrying a heavy payload,” J. of Dynamic Systems, Measurement, and Control, Vol.132, No.5, 2010.
This article is published under a Creative Commons Attribution-NoDerivatives 4.0 Internationa License.