Paper:
Development of a Cross-Platform Cockpit for Simulated and Tele-Operated Excavators
Masaru Ito*, Yusuke Funahara**, Seiji Saiki**, Yoichiro Yamazaki**, and Yuichi Kurita*
*Graduate School of Engineering, Hiroshima University
1-4-1 Kagamiyama, Higashi-hiroshima, Hiroshima 739-8527, Japan
**Global Engineering Center, Kobelco Construction Machinery Co., Ltd.
2-2-1 Itsukaichikou, Saeki-ku, Hiroshima 731-5161, Japan
Japan’s construction industry has a shortage of workers and skilled operators, and the number of operators of hydraulic excavators has actually been decreasing. In addition, the operation of hydraulic excavators is complicated and non-intuitive, so learning and maintaining the skill requires a considerable amount of time and experience. One technology that could solve this problem is the tele-operated hydraulic excavator, but the most common type of tele-operated system is difficult for ordinary hydraulic excavator operators to use. The introduction of operation simulators would be effective, but simulators have to be large and expensive if the interface is reproduced in life size. In this paper, we propose a cross-platform system for operating not only a tele-operated hydraulic excavator but also a hydraulic excavator operation simulator. The cross-platform system uses a tele-operated cockpit with feedback and an interface that gives the operator the sensation of sitting in an actual hydraulic excavator. The cockpit consists of a three-dimensional visual information system using stereo videos and a head mounted display, a motion simulator seat that reproduces the vibration and tilting of the operator’s seat of a hydraulic excavator, and a lever unit used in actual hydraulic excavators. With the cross-platform system, an actual hydraulic excavator can be remotely controlled, and the same cockpit can also be used as a training simulator. One can therefore use the system as an inexpensive means of acquiring and maintaining operation skills. We have successfully produced this proposed system and checked its functions, confirming that it works practically.
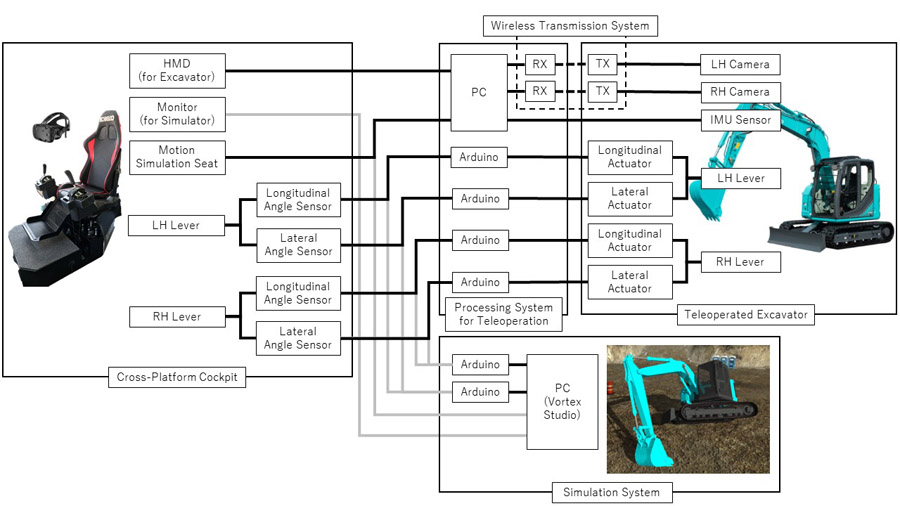
Configuration of cross-platform system
- [1] D. Zhao, Y. Xia, H. Yamada, and T. Muto, “Presentation of Realistic Mortion to the Operator in Operating a Tele-operated Construction Robot,” J. Robot. Mechatron., Vol.14, No.2, pp. 98-104, 2002.
- [2] H. Yamada, H. Kato, and T. Muto, “Master-Slave Control for Construction Robot Teleoperation,” J. Robot. Mechatron., Vol.15, No.1, pp. 54-60, 2003.
- [3] H. Yamada, G. Ming-de, and Z. Dingxuan, “Master-Slave Control for Construction Robot Teleoperation – Application of a Velocity Control with a Force Feedback Model –,” J. Robot. Mechatron., Vol.19, No.1, pp. 60-67, 2007.
- [4] A. A. Yusof, T. Kawamura, and H. Yamada, “Evaluation of Construction Robot Telegrasping Force Perception Using Visual, Auditory and Force Feedback Integration,” J. Robot. Mechatron., Vol.24, No.6, pp. 949-957, 2012.
- [5] L. Huang, T. Kawamura, and H. Yamada, “Construction Robot Operation System with Object’s Hardness Recognition Using Force Feedback and Virtual Reality,” J. Robot. Mechatron., Vol.24, No.6, pp. 958-966, 2012.
- [6] T. Hirabayashi, “Examination of Information Presentation Method for Teleoperation Excavator,” J. Robot. Mechatron., Vol.24, No.6, pp. 967-976, 2012.
- [7] H. Yoshinada, K. Okamura, and S. Yokota, “Master-Slave Control Method for Hydraulic Excavator,” J. Robot. Mechatron., Vol.24, No.6, pp. 977-984, 2012.
- [8] K. Ootsubo, D. Kato, T. Kawamura, and H. Yamada, “Support System for Slope Shaping Based on a Teleoperated Construction Robot,” J. Robot. Mechatron., Vol.28, No.2, pp. 149-157, 2016.
- [9] T. Tanimoto, R. Fukano, K. Shinohara, K. Kurashiki, D. Kondo, and H. Yoshinada, “Research on Superimposed Terrain Model for Teleoperation Work Efficiency,” J. Robot. Mechatron., Vol.28, No.2, pp. 173-184, 2016.
- [10] H. Yamada, N. Bando, K. Ootsubo, and Y. Hattori, “Teleoperated Construction Robot Using Visual Support with Drones,” J. Robot. Mechatron., Vol.30, No.3, pp. 406-415, 2018.
- [11] M. Moteki, K. Fujino, and S. Yuta, “Work Efficiency Evaluation on the Human Interface of the Unmanned Construction,” J. of the Robotics Society of Japan, Vol.33, No.6, pp. 32-35, 2015 (in Japanese).
- [12] A. Ishii, “Teleoperation of Construction Machinery and Double Arm Work Machine ASTACO,” J. of the Robotics Society of Japan, Vol.30, No.6, pp. 582-584, 2012 (in Japanese).
- [13] M. Moteki and H. Yamamoto, “Restoration Activities which is Quick and Safety by Unmanned Construction,” J. of the Society of Instrument and Control Engineers, Vol.55, No.6, pp. 495-500, 2016 (in Japanese).
- [14] K. Fukaya and T. Nakamura, “Development of a Small Sized Simulator to Simulate Hazards in Excavator Accidents,” Specific Research Reports of the National Institute of Industrial Safety, No.32, pp. 31-40, 2005 (in Japanese).
- [15] S. Hamasaki and T. Yakoh, “Implementation and Evaluation of Decorators for Delayed Live Streaming Video on Remote Control System,” Human-Agent Interaction Symp. 2008, 1F-1, 2008 (in Japanese).
This article is published under a Creative Commons Attribution-NoDerivatives 4.0 Internationa License.