Research Paper:
Giant Magnetostrictive Actuators for Ultracompact Electric Vehicles: Analysis of Output Characteristics
Taro Kato*1,
, Kentaro Sawada*2, Wenbao Wu*3
, Ikkei Kobayashi*3, Jumpei Kuroda*3
, Daigo Uchino*4
, Kazuki Ogawa*5
, Keigo Ikeda*6
, Ayato Endo*7
, Xiaojun Liu*8
, Hideaki Kato*2
, Takayoshi Narita*2
, and Mitsuaki Furui*1
*1Department of Mechanical Engineering, Tokyo University of Technology
1404-1 Katakura, Hachioji, Tokyo 192-0982, Japan
Corresponding author
*2Course of Mechanical Engineering, Tokai University
4-1-1 Kitakaname, Hiratsuka, Kanagawa 259-1292, Japan
*3Course of Science and Technology, Tokai University
4-1-1 Kitakaname, Hiratsuka, Kanagawa 259-1292, Japan
*4Department of Mechanical Engineering, National Institute of Technology, Numazu College
3600 Ooka, Numazu, Shizuoka 410-0022, Japan
*5Department of Electronic Robotics, Aichi University of Technology
50-2 Manori, Nishi-hasama, Gamagori, Aichi 443-0047, Japan
*6Department of Mechanical Engineering, Hokkaido University of Science
7-Jo 15-4-1 Maeda, Teine, Sapporo, Hokkaido 006-8585, Japan
*7Department of Electrical Engineering, Fukuoka Institute of Technology
3-30-1 Wajiro-higashi, Higashi-ku, Fukuoka, Fukuoka 811-0295, Japan
*8OMRON Corporation
801 Higashifudomachi, Shiokojidori, Horikawahigashiiru, Shimogyo-ku, Kyoto, Kyoto 600-8530, Japan
Ultracompact electric vehicles have compact, lightweight bodies with low outer-plate rigidity. This results in the transmission of road noise from the tires and wind noise (caused by the projection shape of the vehicle) into the cabin. Interior acoustic control systems require devices that can produce sound waves. Next-generation mobility uses giant magnetostrictive actuators (GMAs) for sound production. This is a foundational study for designing GMAs that can be used in such interior acoustic control systems. Magnetostriction forces are generated when a magnetic field deforms giant magnetostrictive materials. The output characteristics were analyzed by electromagnetic-field analysis. Further, the GMA magnetostriction force was analyzed using the finite element method (FEM)—across varying frequency ranges of piezoelectrically controlled amplifiers. The FEM results indicated that the GMA output performance was sufficient to generate sound waves for active noise control in the low-frequency range, 100–500 Hz (road noise). Further optimization is required to expand the frequency range—to accommodate music playback, etc.—including modification of the actuator size, weight, shape, and components and using materials with higher magnetic permeability.
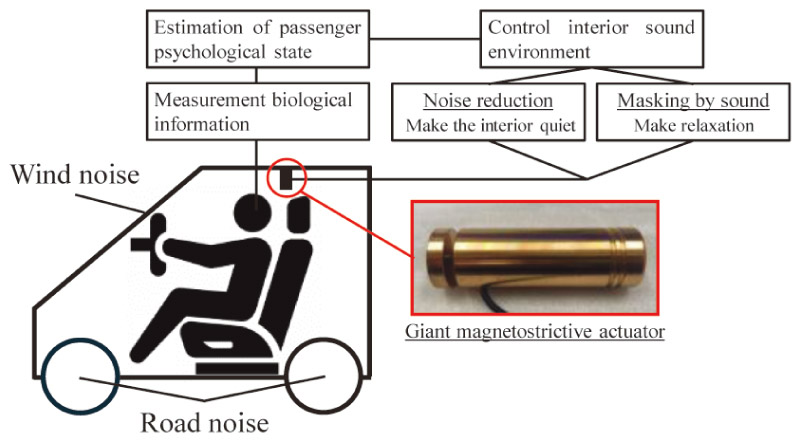
Proposed interior acoustic control system for the ultracompact EV using a GMA
- [1] L. X. Hui, G. Lei, W. Yan, S. Haoran, and H. Yong, “Micro-displacement amplifier of giant magnetostrictive actuator using flexure hinges,” J. of Magnetism and Magnetic Materials, Vol.556, Article No.169415, 2022. https://doi.org/10.1016/j.jmmm.2022.169415
- [2] Z. Zhou, Z. He, G. Xue, J. Zhou, C. Rong, and G. Liu, “Analysis of working characteristics of giant magnetostrictive actuator for direct-drive fuel injector,” AIP Advances, Vol.12, No.7, Article No.075216, 2022. ttps://doi.org/10.1063/5.0098073
- [3] C. Chu, R. Zhu, and X. Jia, “Controller design of a brake-by-wire system based on giant-magnetostrictive material for an intelligent vehicle,” Sustainability, Vol.14, No.17, Article No.11057, 2022. https://doi.org/10.3390/su141711057
- [4] Y. Matsui, “Giant magnetostrictive actuator,” Trans. of the Japan Society of Mechanical Engineers, Vol.111, No.1072, pp. 188-189, 2008 (in Japanese). https://doi.org/10.3390/su141711057
- [5] M. Yamagata, “Development of vibration-powered generation unit which is unused energy of vehicle driving,” The J. of the Institute of Electrical Installation Engineers of Japan, Vol.42, No.7, pp. 469-471, 2022 (in Japanese). https://doi.org/10.14936/ieiej.42.469
- [6] N. Uechi and T. Takanashi, “Behavioural control of plautia stali (hemiptera: pentatomidae) using vibrations, and its application in pest management,” J. of The Japanese Society of Applied Entomology & Zoology, Vol.65, No.1, pp. 13-20, 2021 (in Japanese). https://doi.org/10.1303/jjaez.2021.13
- [7] F. Maehara, T. Kitamura, D. Uchino, K. Ogawa, T. Kato, K. Ikeda, A. Endo, H. Kato, and T. Narita, “Acoustic control system using boundary vibration with giant magnetostrictive actuator (comparative consideration of noise reduction volume by changing actuator excitation position),” J. of the Japan Society of Applied Electromagnetics and Mechanics, Vol.31, No.2, pp. 244-250, 2023. https://doi.org/10.14243/jsaem.31.244
- [8] K. Ishizuka, T. Kato, H. Kato, T. Narita, A. Kojima, and H. Moriyama, “Active noise control for ultra-compact vehicle using giant magnetostrictive actuator (comfort evaluation of the vehicle interior noise by EEG),” J. of Applied Electromagnetic and Mechatronics, Vol.25, No.2, pp. 88-93, 2017 (in Japanese). https://doi.org/10.14243/jsaem.25.88
- [9] T. Kato, R. Suzuki, R. Miyao, T. Kato, H. Kato, and T. Narita, “Fundamental consideration of active noise control by small actuator for ultra-compact EV,” Actuators, Vol.7, No.3, Article No.49, 2018. https://doi.org/10.3390/act7030049
- [10] D. Flor, D. Pena, L. Pena, V. A. de Sousa Jr., and A. Martins, “Characterization of noise level inside a vehicle under different conditions,” Sensors, Vol.20, No.9, Article No.2471, 2020. https://doi.org/10.3390/s20092471
- [11] Z. Jia, X. Zheng, Q. Zhou, Z. Hao, and Y. Qiu, “A hybrid active noise control system for the attenuation of road noise inside a vehicle cabin,” Sensors, Vol.20, No.24, Article No.7190, 2020. https://doi.org/10.3390/s20247190
- [12] Y. He, S. Schroder, Z. Shi, R. Blumrich, Z. Yang, and J. Wiedemann, “Wind noise source filtering and transmission study through a side glass of DrivAer model,” Applied Acoustics, Vol.160, Article No.107161, 2020. https://doi.org/10.1016/j.apacoust.2019.107161
- [13] R. Akimatsu, A. Tomido, R. Kobayashi, and S. Kato, “Applying perforated panel sound-absorbing structures to HVAC,” Trans. of Society of Automotive Engineers of Japan, Vol.54, No.6, pp. 1145-1150, 2023 (in Japanese). https://doi.org/10.11351/jsaeronbun.54.1145
- [14] K. Shibahashi, T. Kanazawa, S. Tanabe, and T. Toi, “Sound design of background noise in the electric vehicle interior based on the perception of electric vehicle powertrain noise,” Trans. of Society of Automotive Engineers of Japan, Vol.54, No.2, pp. 278-283, 2023 (in Japanese). https://doi.org/10.11351/jsaeronbun.54.278
- [15] A. Y. Atmoji, Z. Masfuri, M. Sabrina, A. Basuki, Y. Feriadi, Suwarjono, and Sugianto, “BBTA3-BPPT 1st prototype of active noise control for vehicle cabin noise,” J. of Physics: Conf. Series, Vol.1951, Article No.012030, 2021. https://doi.org/10.1088/1742-6596/1951/1/012030
- [16] S. Kim and M. E. Altinsoy, “Active control of road noise considering the vibro-acoustic transfer path of a passenger car,” Applied Acoustics, Vol.192, Article No.108741, 2022. https://doi.org/10.1016/j.apacoust.2022.108741
- [17] S. Zhang, L. Zhang, D. Meng, and X. Pi, “Active control of vehicle interior engine noise using a multi-channel delayed adaptive notch algorithm based on FxLMS structure,” Mechanical Systems and Signal Processing, Vol.186, Article No.109831, 2023. https://doi.org/10.1016/j.ymssp.2022.109831
- [18] T. Kitamura, F. Maehara, T. Kato, D. Uchino, K. Ogawa, K. Ikeda, A. Endo, T. Narita, and H. Kato, “A study on masking system using 1/f fluctuation to improve comfort in ultra-compact EVs,” Int. J. of Applied Electromagnetics and Mechanics, Vol.71, No.1, pp. S373-S382, 2023. https://doi.org/10.3233/JAE-220180
- [19] T. Kato, H. Nakayama, H. Kato, and T. Narita, “A basic study on sound control system for ultra-compact electric vehicle by using masking,” Applied Sciences, Vol.10, No.10, Article No.3412, 2020. https://doi.org/10.3390/app10103412
- [20] T. Kato, T. Kitamura, F. Maehara, D. Uchino, K. Ogawa, K. Ikeda, A. Endo, H. Kato, T. Narita, and M. Furui, “Calculation of 1/f fluctuation from sound signal and comfort evaluation,” Applied Sciences, Vol.12, No.19, Article No.9425, 2022. https://doi.org/10.3390/app12199425
- [21] T. Mori, “Investigation of power metallurgical RFe2 compound and their applications,” J. of the Japan Society for Precision Engineering, Vol.60, No.12, pp. 1691-1694, 1994 (in Japanese). https://doi.org/10.2493/jjspe.60.1691
- [22] T. Kobayashi and I. Sasaki, “Giant magnetostrictive material and actuator application,” J. of the Japan Society for Precision Engineering, Vol.60, No.12, pp. 1695-1698, 1994 (in Japanese). https://doi.org/10.2493/jjspe.60.1691
- [23] B. Yoo, K. Hirata, and A. Oonishi, “Coupled electro-magneto-mechanical-acoustic analysis method developed by using 2D finite element method for flat panel speaker driven by magnetostrictive-material-based actuator,” IEEJ Trans. on Industry Applications, Vol.130, No.12, pp. 1315-1322, 2010. https://doi.org/10.1541/ieejias.130.1315
- [24] M. Sugasawa and M Arai, “Evaluation of eddy current characteristics for applied high frequency voltage to the giant magnetostrictive material,” Trans. of the Japan Society for Computational Method in Engineering, Vol.7, No.2, pp. 235-238, 2008 (in Japanese).
- [25] T. Mori, “Giant magnetostrictive actuator,” J. of the Robotics Society of Japan, Vol.15, No.3, pp. 334-337, 1997 (in Japanese). https://doi.org/10.7210/jrsj.15.334
This article is published under a Creative Commons Attribution-NoDerivatives 4.0 Internationa License.